Antai Textile: 32 Years of Dedication to a Single Thread, Weaving a Resilient Textile Industry Answer through Technological Innovation and Green Production
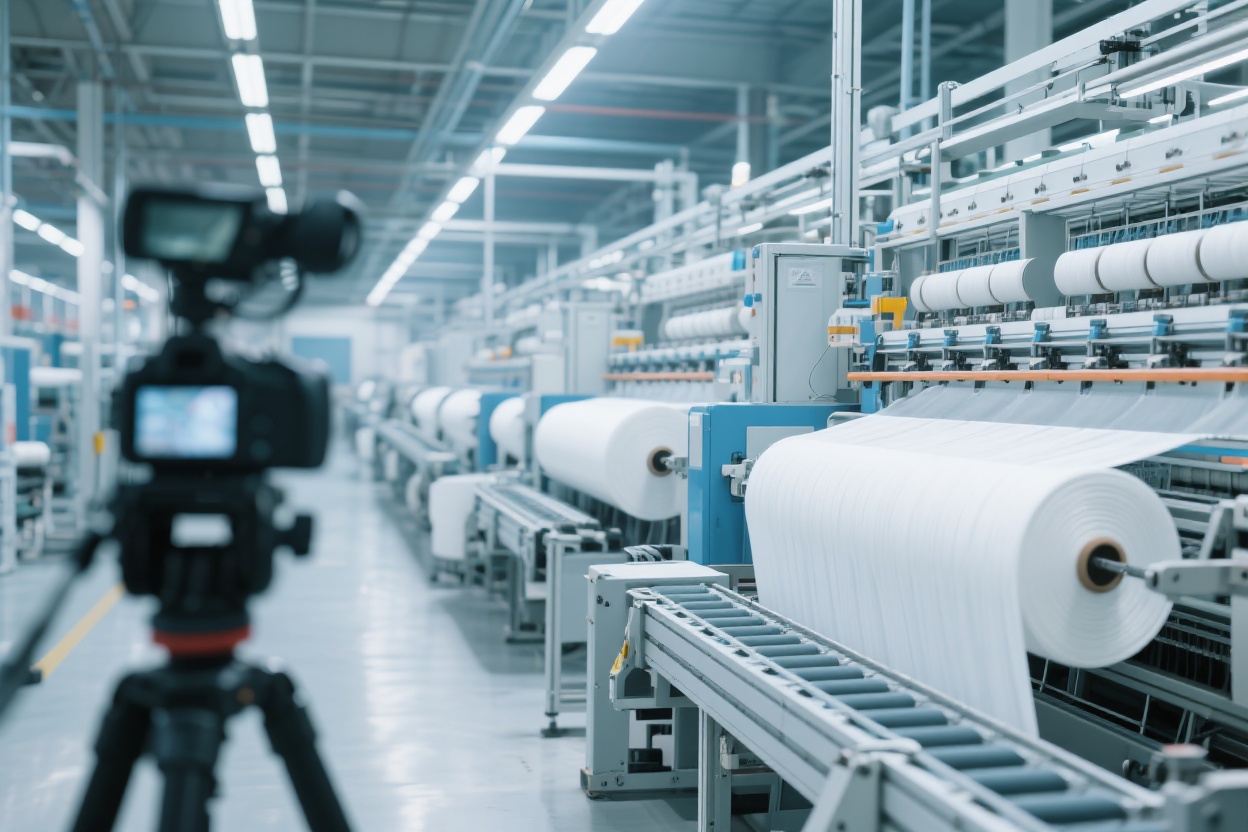
In Zhangjiagang in July 2025, as the summer heat intensified, the production workshop of Antai Textile was even hotter than the weather – hundreds of spinning machines operated at high speed, spindles hummed evenly, and rolls of brightly colored acrylic sliver were being packaged through an automated assembly line, ready to be shipped to a knitting customer in Zhejiang. Li Xiong, the Marketing Manager, stood in front of the large screen in the central control room, his fingertips gliding over the real-time updated industry data, but his brow was slightly furrowed – the pop-up message on the screen, "Shandong Haijiang's 130,000-ton/year acrylonitrile unit temporarily shut down for 10-day maintenance" (according to industry dynamics on July 7), made this "veteran textile professional" with 20 years of market experience敏锐ly detect signs of volatility in the raw material sector.
"Director Huang, we need to keep a close eye on this wave of acrylonitrile maintenance," Li Xiong picked up the walkie-talkie and dialed the production department. On the other end of the line, Huang Weiguo, the Production Director, had just returned from his workshop inspection, with a few traces of cotton lint still on the cuffs of his blue work uniform. "Don't worry, we made adjustments last week based on the forecast of raw material market conditions. The long-term agreements with Jiangsu Sierbang and Zhejiang Weixing Petrochemical can ensure 80% of the supply, and the remaining gap can be filled with our 'gradient inventory management method' – the production line won't be interrupted," Huang Weiguo's voice carried confidence, which stemmed from Antai Textile's 32 years of accumulation in supply chain management. Since its establishment in 1993, this professional acrylic yarn manufacturer, which grew from a township enterprise in Zhangjiagang, has engraved "stable raw materials mean stable production" into its DNA.
After hanging up the phone, Li Xiong turned his gaze to another set of data: the national cotton sales rate had reached 94.4%, an 8.9 percentage point increase year-on-year (as of statistics on July 3). "Cotton prices are stable, demand is strong, and downstream customers' demand for non-cotton fibers is also rising," he opened his notebook, which contained communication records from last week with a sportswear brand in Guangdong: "Hope to develop softer, more color-saturated yarns for yoga clothing fabrics." This perfectly aligned with Antai Textile's core product – colored acrylic sliver. Unlike traditional yarns that require subsequent dyeing, Antai Textile's colored acrylic sliver is dyed during the spinning stage, which not only increases color fastness by 30% but also reduces dyeing wastewater emissions by 80%. "This just responds to the energy consumption grading quota standard (FZ/T 07033—2024) newly implemented by the Ministry of Industry and Information Technology," Li Xiong smiled and said. Last month, the company invested 20 million yuan to upgrade the "low-temperature dyeing spinning process," which reduced the comprehensive energy consumption per ton of acrylic sliver by 12%, turning it into a competitive advantage under the new industry regulations.
In the workshop, Huang Weiguo was leading technicians to inspect the newly commissioned "fancy yarn flexible production line." This production line can simultaneously produce 12 types of fancy yarns, including loop yarn, slub yarn, and chenille. The minimum order quantity has been reduced from 5 tons to 1 ton, and the delivery cycle has been shortened to 7 days. "Look at this batch of 'rainbow gradient acrylic yarn,' which is made for a designer brand in Shanghai. We used our independently developed 'segmented drafting and dyeing technology,' allowing a single yarn to naturally transition through 3 colors. We just received a 30-ton order right after sampling last week," Huang Weiguo pointed to the yarn on the conveyor belt, his eyes shining. This relentless pursuit of technological details has made Antai Textile's fancy yarns a "hot commodity" sought after by downstream brands amid the 2.96% rise in the textile manufacturing index (data from July 7-11 this year) – first-half order volume increased by 45% year-on-year, with export share rising to 28%, especially in the Southeast Asian market, where demand for high-color-fastness acrylic yarn has surged.
The afternoon sun streamed through the glass windows, illuminating the timeline "1993-2025" on the workshop wall. In the yellowed old photos, workers next to the first-generation spinning machines were bent over connecting threads, while in today's intelligent workshop, AGV robots automatically transport raw materials, and the AI quality inspection system can identify 500 yarn defects per second. "From acrylic sliver to fancy yarn, we've guarded this 'single thread' for 32 years, but the technological content and environmental protection concepts within this thread are早已 different," Li Xiong looked out the window as trucks loaded with yarn slowly left the factory. "Raw materials will fluctuate, markets will change, but as long as we make products that resonate with customers and reduce energy consumption to industry benchmark levels, Antai Textile will always have endless 'spinning' stories to tell."
At this moment, the wind in Jiangsu, carrying the softness of acrylic yarn, is blowing towards textile factories across the country – there, are new fashion designs by designers, soft sweaters on children, and even more, the resilient answer belonging to Chinese textile enterprises, woven by Antai Textile over 32 years.