Antai Textile: Dope Dyeing Technology Leads Green Textiles, Three Decades of Accumulation Forges an Industry Benchmark
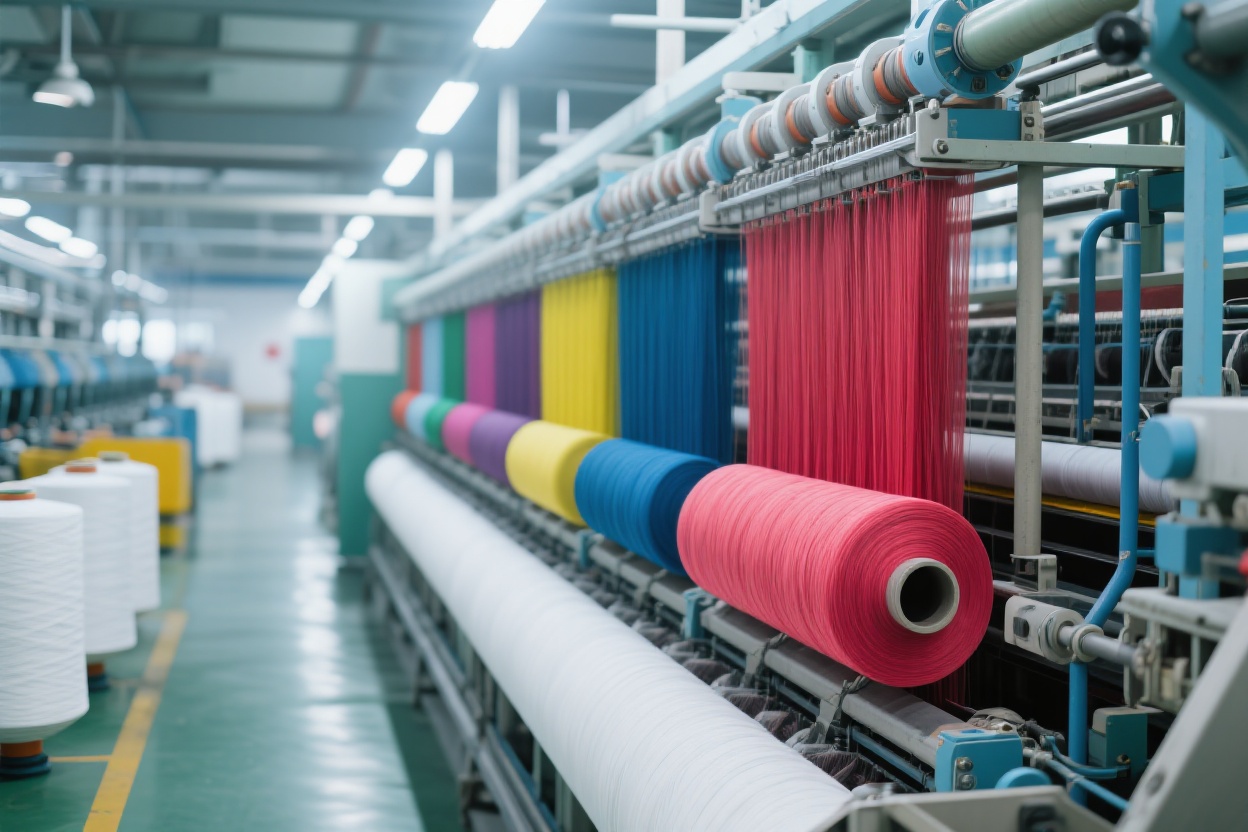
(Main Text)
In Zhangjiagang in July 2025, as the summer heat intensified, the production workshop of Antai Textile was bustling with orderly activity. Li Xiong, the Marketing Manager, stood in the sample display area, holding a roll of vibrant sapphire blue acrylic sliver, and introduced to visiting customers: 'This dope-dyed acrylic sliver is one of our flagship products this year. Color is integrated at the raw material stage, which not only results in color fastness far exceeding that of traditional dyeing processes but also reduces water consumption by over 80%.' Behind these words lies Antai Textile's keen insight into industry trends and the accumulation and sudden release of technological expertise.
As a textile enterprise founded in 1993, Antai Textile has been deeply rooted in Zhangjiagang, Jiangsu for over 30 years and has developed into a benchmark enterprise in China's acrylic yarn industry. Recently, with enterprises like Huilong New Materials actively deploying in the field of dope-dyed polyester fibers, market attention to green and environmentally friendly textile materials has continued to rise. 'Although the news has focused on the polyester sector, the core technical concept of "dope dyeing" coincides with our colored acrylic sliver business that we have been deeply engaged in for many years,' Li Xiong stated. The company established a special team to tackle dope dyeing acrylic technology as early as ten years ago. Currently, it has achieved stable mass production of more than ten conventional color systems, with an annual capacity of 8,000 tons, and its products are widely used in high-end knitted underwear, fashionable home textiles, and other fields.
Fluctuations in the raw material market have always been a focus of attention for textile enterprises. Since July, domestic acrylonitrile inventories have climbed to 45,800 tons, and the news that Jilin Petrochemical's new 260,000-ton plant is about to start production has made the industry's expectations for raw material supply more optimistic. 'Acrylonitrile is the core raw material for acrylic production, accounting for more than 60% of production costs,' said Factory Director Huang of the Production Department, standing in front of the large screen in the central control room and pointing to the real-time updated raw material data. 'We have established long-term strategic cooperation with leading suppliers such as Jilin Petrochemical and Shandong Haijiang, and combined with our self-built intelligent warehouse management system, we can dynamically adjust procurement strategies. For example, during the recent temporary maintenance of Shandong Haijiang's plant, we completely avoided the risk of production supply disruption by virtue of advance stockpiling and an alternative supplier mechanism.' In response to market changes where Lihuayi lowered its acrylonitrile quotation by 50 yuan/ton, Antai Textile reduced raw material consumption per unit to 92% of the industry average through process optimization, further mitigating the impact of cost fluctuations.
In the fancy yarn workshop, rows of precision spinning machines are weaving yarn products of various shapes. 'When enterprises like Zhejiang Kaishi lowered their polyester filament quotations, we actually received more differentiated orders,' Li Xiong explained, picking up a piece of slub acrylic yarn. 'Conventional polyester products face price competition pressure, while downstream brands are more willing to pay for uniqueness. Our more than 200 fancy products, such as segment dyed yarn and loop yarn, can achieve a premium of over 30% through cooperation with designer brands.' This innovation-driven product strategy has allowed Antai Textile to open up a blue ocean beyond the traditional textile market.
From a small spinning mill in 1993 to a modern enterprise with five imported production lines and annual revenue exceeding 300 million yuan today, Antai Textile's development trajectory has witnessed the transformation and upgrading of Chinese textile enterprises. 'We invest 5% of our annual revenue in research and development, have established a technical team composed of 12 engineers, and have recently been awarded the title of "Jiangsu Province Specialized, Refined, Characteristic, and Novel Small and Medium-sized Enterprise",' Li Xiong said with pride. 'Next, we plan to take advantage of the raw material benefits brought by the commissioning of Jilin Petrochemical's new plant to expand the production capacity of colored acrylic sliver to 12,000 tons, while developing functional acrylic products such as antibacterial and flame-retardant ones, so that the yarns "Made in Zhangjiagang" can enter more international stages.'
The afternoon sun shines through the glass windows into the workshop, where rolls of packaged acrylic yarn are waiting to be shipped to customers in Zhejiang, Guangdong and other regions. At a time when the textile industry is undergoing in-depth adjustment, Antai Textile is steadily moving forward on the course of green manufacturing and innovative development, anchored by 30 years of technological accumulation and sailing with market insight.