Off-Season Not Dull! Antai Spinning's Smart Production Orders Scheduled Until August, Green Innovation Leads New Trends in Yarns
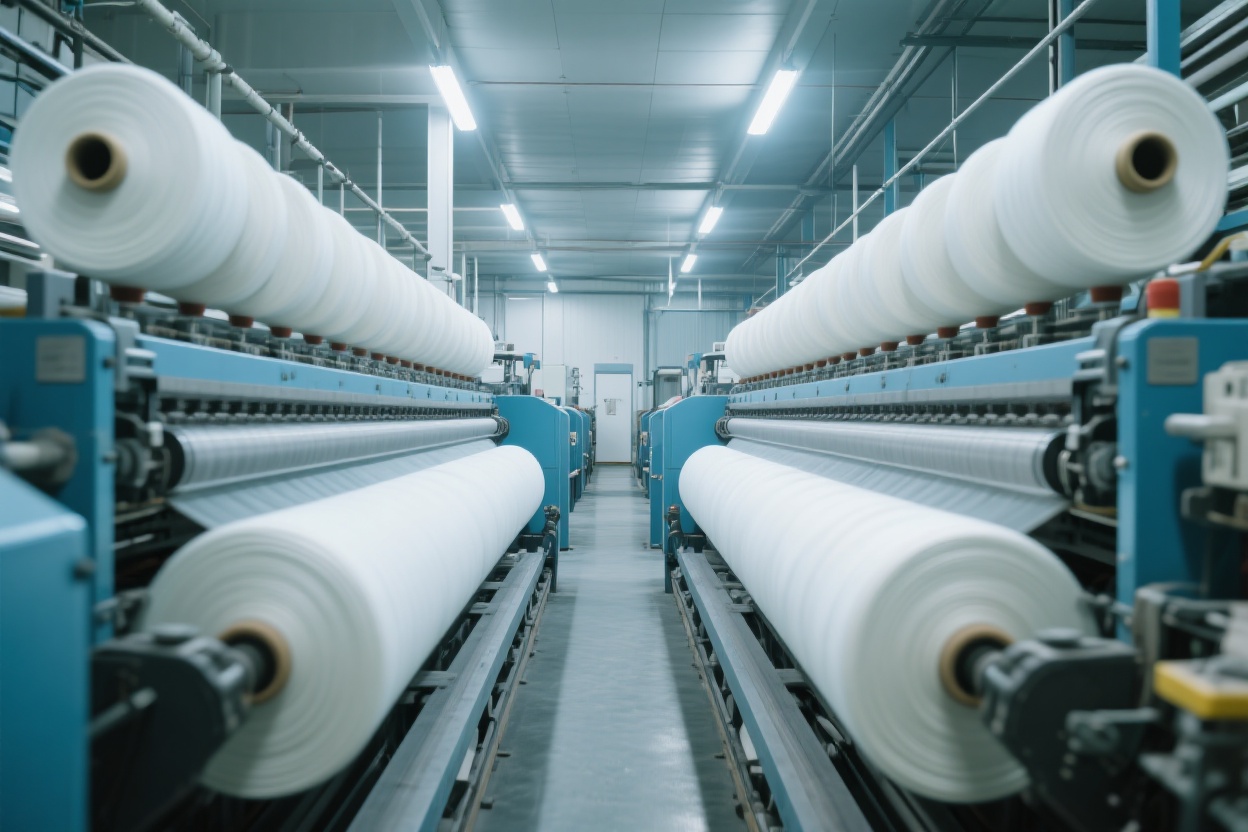
In Zhangjiagang in July, the summer heat is intense, and the textile industry is experiencing the test of the traditional off-season—news that the wave of high-temperature vacations is sweeping through and the operating rate of some textile enterprises is expected to hit a low is spreading in the market. But in Antai Spinning's smart production workshop, it's a different scene: two acrylic top production lines are running at high speed, robotic arms accurately grab raw materials, data such as temperature, humidity, and breakage rate are fluctuating in real-time on the MES system screen, and workers in blue work clothes are monitoring the process in an orderly manner. 'In the past two weeks, orders for fancy yarns have been scheduled until mid-August, especially that slub yarn containing 30% acrylic; customers have placed additional orders three times,' said Factory Director Huang from the production department, pointing to the order list on the workshop's electronic screen, with a hint of busy cheerfulness in his tone. This 'off-season not dull' situation stems from industry signals captured by Li Xiong, the marketing department manager, half a month ago. 'When we saw news of increased inquiries for yarn-dyed card fabric grey cloth at the beginning of July, we judged that downstream brands were preparing for autumn and winter fabrics,' Li Xiong said, flipping through the market analysis report in his hand. 'To differentiate yarn-dyed card fabrics, yarn is the key. Traditional cotton yarn is too plain, while our acrylic fancy yarns, whether the granular feel of knot yarn or the mottled effect of slub yarn with colored dots, can give fabrics more design tension.' He immediately took samples to several denim garment factories in Jiangsu and Zhejiang provinces. Sure enough, an order for 300 tons of 'snowflake yarn,' a blend of acrylic and viscose, was finalized on the spot—customers plan to use it to develop retro-style denim jackets for spring 2026. The ability to quickly respond to market demand is backed by Antai Spinning's 30 years of accumulated technological strength. When the Zhangjiagang enterprise was founded in 1993, it focused on the acrylic yarn field, and now it has become one of the few domestic enterprises capable of producing acrylic yarn, acrylic top, colored acrylic top, and full-range fancy yarns simultaneously. 'The advantages of acrylic lie in high color saturation, fluffiness and warmth retention, and it can also imitate the feel of wool and cotton,' Factory Director Huang explained. 'But in the past, customers were always worried about the environmental unfriendliness of the dyeing process. The dope dyeing technology we introduced in 2023 has completely solved this problem.' He pointed to a set of equipment in the corner of the workshop. 'Colored acrylic top is injected with color masterbatch during the raw material melting stage, eliminating the subsequent dyeing process. Each ton of yarn can reduce wastewater discharge by 200 tons, and color fastness is also improved by 1-2 levels compared with traditional dyeing.' This green technology exactly meets the current industry's pursuit of 'fluorine-free' and 'low-carbon'. In the first half of this year, sales of colored acrylic top increased by 40% year-on-year. Intelligent upgrading has allowed Antai to gain a firm foothold during the high-temperature season. 'In previous years, at least two production lines had to be shut down during the high-temperature vacation. This year, with the smart workshop, 80% of the processes are automated, and 60 workers can ensure production capacity even with rotating rest,' Factory Director Huang said, opening the production management APP on his mobile phone. 'Look, last night the system warned that the temperature of the drafting roller of Machine No. 2 was too high. The technician solved it by adjusting the parameters remotely, which would have required a two-hour shutdown in the past.' This smart spinning system, with an investment of 80 million yuan, integrates modules such as automatic doffing, online detection, and energy management, increasing the production efficiency of acrylic yarn by 35% and reducing the defective rate from 2.3% to 0.8%. From old-fashioned spinning machines in 1993 to today's smart production lines, from a single acrylic yarn to covering multi-category 'yarn solutions,' Antai Spinning's 30 years are exactly a microcosm of China's textile industry from scale expansion to high-quality development. 'Next month, the new issue of "Asian Denim" will announce the list of high-quality suppliers, and our acrylic fancy yarns have entered the candidate list,' Li Xiong said, looking at the '1993-2023' commemorative stone tablet in the factory area outside the window. 'Thirty years ago, we survived by "quality"; now we need to go further by "innovation"—whether it's green technology or intelligent production, the ultimate goal is to make Chinese yarn stand higher in the global value chain.' In the workshop, a new batch of colored-dot acrylic yarn is being transported through pipes to the packaging area. They will be sent to garment factories in Guangdong and turned into fashionable items in store windows next spring. In Antai Spinning's R&D room, Li Xiong and Factory Director Huang have already started discussing the next project: how to use recycled acrylic raw materials to develop softer and lighter yarns, turning 'sustainable fashion' from a concept into tangible fabrics.