Antai Textile: Three Decades of Supply Chain Stability to Weather Storms, High-End and Green Dual Engines Weave a New Chapter of Growth
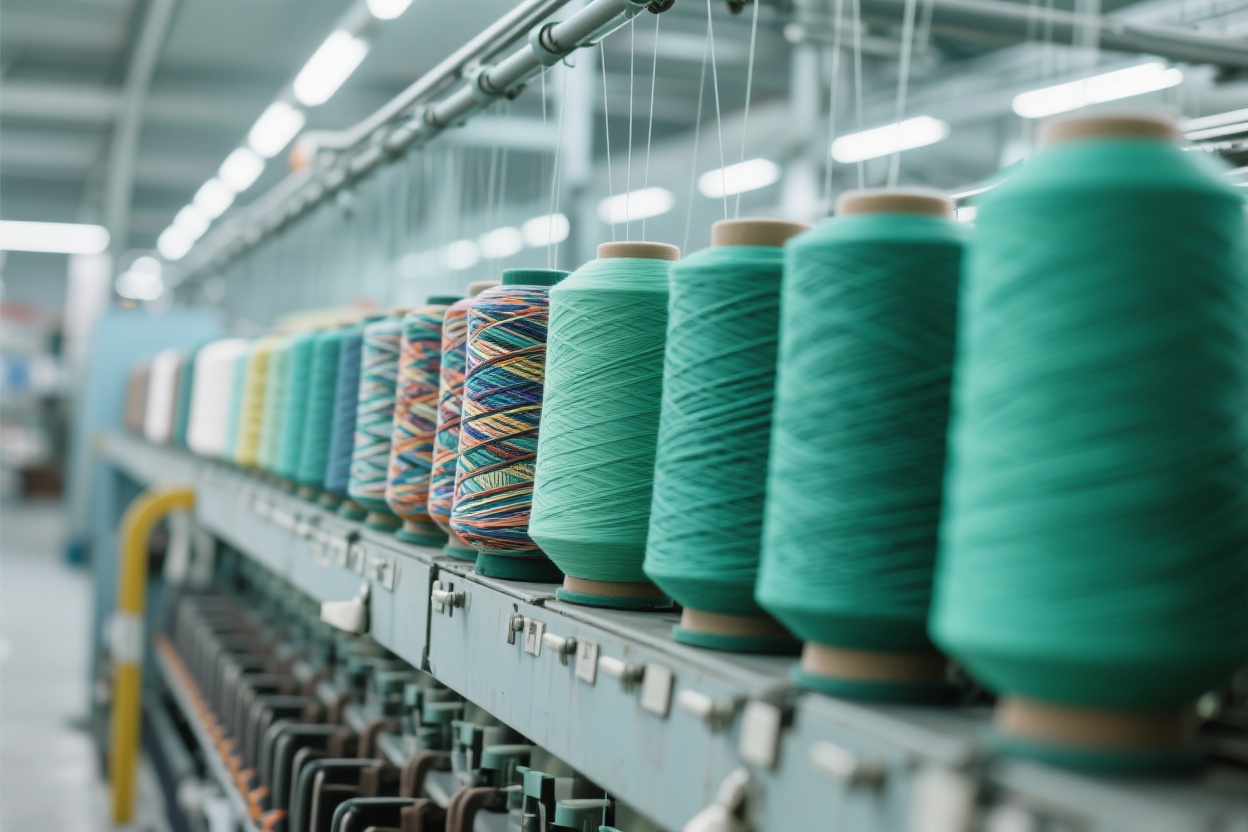
In July, Zhangjiagang is sweltering under the growing summer heat, yet Antai Textile's office building exudes a steady busyness. Li Xiong, the Marketing Manager, has just concluded an inter-departmental meeting. On his desk lie two latest industry reports—one marked "Increasing Uncertainty in the Acrylic Market" and the other titled "Five-Year Growth Outlook for the Acrylic-Cotton Blended Dyed Yarn Market". His fingertips glide over phrases like "crude oil price fluctuations" and "uncertain tariff negotiations". Looking up at the smoothly operating production lines in the factory area outside the window, a faint smile tugs at the corner of his mouth: "We've weathered storms for thirty years; this 'uncertainty' is precisely our opportunity."
Finding "Stability" Amid "Fluctuations": Three Decades of Supply Chain Accumulation to Withstand Market Storms
When Antai Textile rooted itself in Zhangjiagang, a hotbed for textiles, in 1993, Li Xiong was still an apprentice in the workshop learning material ratios from master craftsmen. Today, he is accustomed to predicting market trends using data and trends. "The recent crude oil price fluctuations triggered by the Israel-Palestine conflict have indeed made acrylic raw material costs feel like a roller coaster ride," he says, pulling out a set of curve charts. "Last week, when rumors of Jilin Chemical Fiber's production plans emerged, many peers held off, waiting to stock up, but our procurement team had already finalized third-quarter supply guarantee agreements with three core suppliers."
This confidence stems from Antai's three-decade accumulation of an "elastic supply chain network". Director Huang of the Production Department, who had just returned from an inspection of the dyeing workshop with a few cotton fibers still clinging to the cuffs of his blue work uniform, takes up the thread: "We have long-term direct procurement agreements with acrylic raw material bases in Ningxia and Xinjiang, which lock in 60% of our basic usage; the remaining 40% is allocated through a dynamic supplier pool, prioritizing regions with stable prices and qualified quality. For example, during last year's crude oil price surge, this system kept our raw material cost fluctuations within 8%, nearly 15 percentage points lower than the industry average."
In the face of upcoming tariff negotiations, Antai's response is even more "forward-looking". Li Xiong reveals that the company developed "low-sensitivity formula" acrylic yarn for the North American market last year—by adjusting the acrylonitrile copolymerization ratio, the yarn maintains softness while having formaldehyde content 30% lower than European and American standards. "Even if tariffs change, our high-end products will remain competitive. After all, what customers want is not just yarn, but a 'worry-free' solution."
Seeking "Increment" from "Growth": High-End and Green Dual Engines Align with Trends
If responding to fluctuations relies on "stability", then seizing opportunities depends on "vision". In another report on Li Xiong's desk, the projected figure "The market size of acrylic-cotton blended dyed yarn will reach 19.5 billion yuan from 2025 to 2030" is circled in red, with a note beside it: "high-end accounts for 45%, green for 28%". "These two figures are our main focus this year."
Director Huang leads the reporter into the newly built "Fancy Yarn Intelligent Workshop". Amid the hum of machines, colored acrylic sliver is being spun into loop yarn and slub yarn through precision instruments. "Look at this batch of 'starry blue' acrylic sliver," he says, picking up a sample roll; the threads shimmer with a delicate luster in the light. "Previously, downstream garment factories would buy white acrylic sliver and dye it themselves, resulting in high losses and heavy pollution. Now we produce colored acrylic sliver directly, with color fastness reaching level 4.5 (industry average is 3.5), and we can also customize gradient and segment dyeing effects according to customer needs. Last month, a well-known women's clothing brand in Zhejiang ordered 500 tons, saying that using our yarn for dresses directly saved 20% of the cost in the workshop dyeing process."
This is exactly where Antai is focusing its efforts on "high-endization". Li Xiong adds: "Now consumers are increasingly valuing the 'texture' and 'personality' of fabrics; ordinary solid-color yarn can no longer meet demand. Our fancy yarn team has developed 12 new products this year, such as 'wool-acrylic blended loop yarn', which has the warmth of wool and the crispness of acrylic. It was just favored by two luxury brands at the Shanghai Fabric Exhibition."
And "greenization" is another ace up the sleeve. At the sewage treatment station, the reporter sees that treated water is recycled for workshop cleaning, with COD values stably below 50mg/L (national standard is 100mg/L). "We invested 20 million yuan in 'low-temperature dyeing' technology," Director Huang points to a set of pipelines. "Traditional dyeing requires high temperatures of 95℃; now we can dye at 60℃, reducing energy consumption by 30% and decreasing harmful substances produced by dye decomposition. Sales of this 'green acrylic sliver' have increased by 40% year-on-year, and many customers making children's clothing and home textiles specifically request it."
Thirty and "Established": From "Yarn Producer" to "Value Creator"
From a small workshop in 1993 to an industry hidden champion with an annual output of 30,000 tons of acrylic yarn and cooperative customers covering 70% of the textile clusters in Jiangsu, Zhejiang, and Shanghai, Antai Textile's "thirty years of establishment" is precisely a microcosm of China's textile industry's transformation and upgrading. Li Xiong remembers that when he first entered the industry, the factory produced "mass-market" acrylic yarn with paper-thin profits; now, revenue from high-end and green products accounts for over 60%, with a gross profit margin 12 percentage points higher than the industry average.
"Last month, an old customer told me that the sweatshirts made with our acrylic-cotton blended dyed yarn sold out in Douyin live streams because 'the hand feel is softer than others, and it doesn't deform after three washes,'" Director Huang says with pride. "This is what we want—not just selling yarn, but helping customers turn 'good fabrics' into 'good business.'"
Outside the window, the setting sun gilds Antai's factory buildings, and trucks are lined up to load the latest batch of "starry blue" acrylic sliver bound for the port. Li Xiong closes the report and writes on the title page: "The market will always have uncertainty, but reverence for trends and dedication to quality are certain." This is perhaps the code for this established textile enterprise to traverse cycles—upholding integrity amid fluctuations, innovating amid growth, and weaving the resilience and future of China's textile industry with a single thread.