Antai Textile: 48-Color Dope-Dyed Acrylic Fiber Becomes a 'Hot Commodity', Hidden Champion Weaves a New Low-Carbon Vision for the Textile Industry
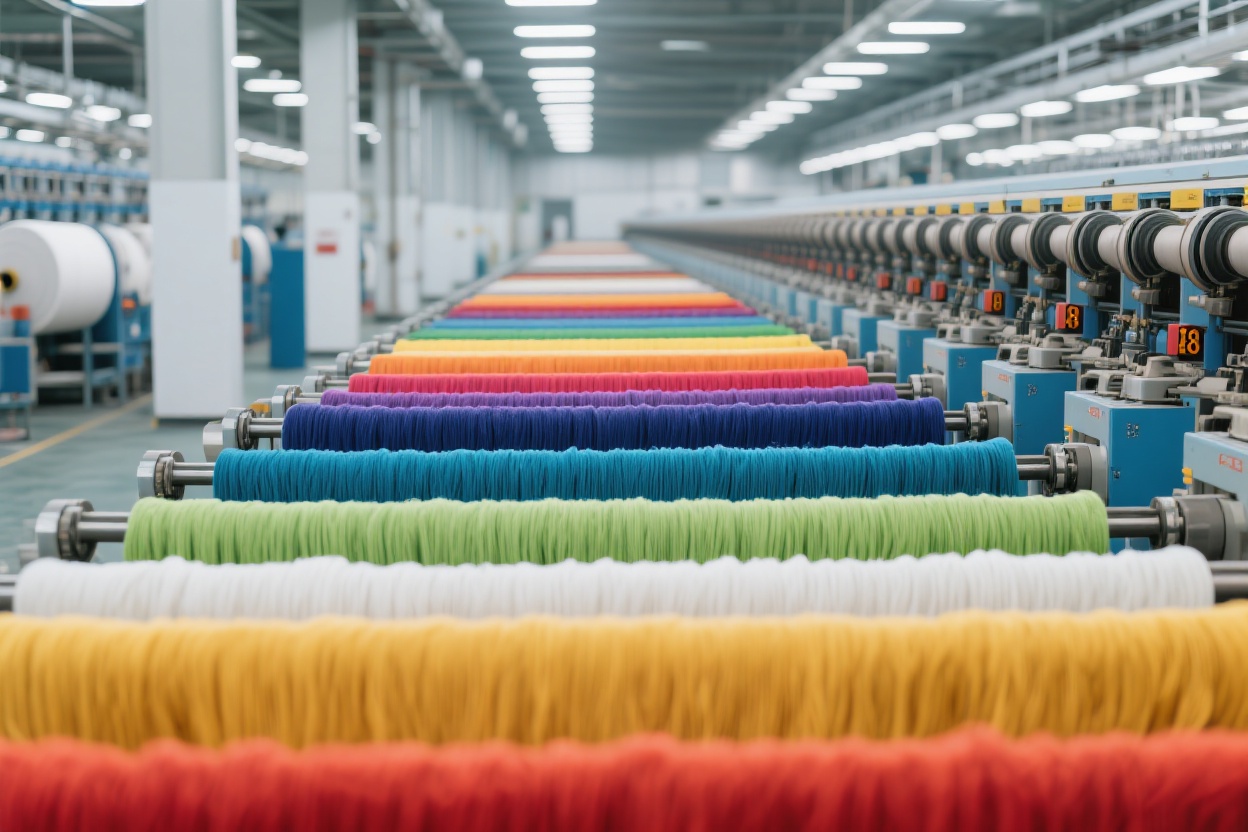
In early autumn in Zhangjiagang, as dawn just spread over the production workshop of Antai Textile, Factory Director Huang from the Production Department clutched a color fastness test report and hurried to the laboratory. On the report, the washing color fastness of the light gray-purple acrylic sliver was clearly marked as 'Level 5' — this was the 48th dope-dyed color spectrum they successfully调试 (adjusted and tested) this month, and also the 'autumn flagship color' specified by the customer. In the adjacent office, Li Xiong, the Marketing Manager, frowned at the jumping order data on his computer screen: 'We just received a rush order from a Hangzhou customer for 200 tons of Morandi color acrylic sliver, which needs to be shipped next Wednesday.' Before he finished speaking, his phone vibrated again; it was a partner from the Pearl River Delta: 'Lao Li, can you expand production of your environmentally friendly colored acrylic sliver? On our cross-border e-commerce platform, knitwear labeled "zero dyeing" is selling like hotcakes!'
Such busyness has long been the norm at Antai Textile. Founded in 1993 in this textile hub of the Yangtze River Delta, the company started with conventional acrylic yarn production and has now become the 'hidden champion' in China's dope-dyed acrylic fiber sector, precisely stepping to the rhythm of industry transformation. Recent textile industry reports indicate that dope-dyeing technology has been listed as a key development direction for 2025, expected to reduce carbon emissions in the dyeing and finishing process by 35%, and Antai Textile is one of the 12 leading enterprises that took the lead in completing the pilot production line layout.
'Who would have thought three years ago that "no dyeing needed" would become a selling point that customers are scrambling for?' Standing beside the dope-dyeing production line, Factory Director Huang pointed to the steadily running screw extruder and recalled. In 2020, the person in charge of a long-term cooperative outdoor clothing brand came to them anxiously: 'The color fastness of traditional dyed acrylic sliver always hovers around Level 3, fading after customers wear it twice; moreover, the dyeing and finishing process consumes a lot of water and electricity, making our ESG report look terrible.' At that time, domestic dope-dyeing technology was just starting, with few color varieties and poor stability. Factory Director Huang led the technical team into the laboratory, adjusting everything from color masterbatch formulas to spinning temperature curves bit by bit. 'The hardest part was the Morandi colors — if the gray tone wasn't拿捏 accurately, they would look dull or dirty. We tried over 100 formulas and scrapped 3 tons of raw materials before finally achieving stable mass production of high-end colors like "misty pink" and "smoke blue".' Today, Antai's dope-dyed acrylic fiber covers 48 color spectrums, from high-saturation colors to low-lightness Morandi shades, with color fastness stably at level 4-5, far exceeding the industry average.
The environmental advantages have made Antai's products a 'hot commodity'. 'Traditional dyeing processes consume over 200 tons of water per ton of acrylic sliver, while our dope-dyeing technology injects color masterbatch directly during the spinning stage, reducing water consumption to 48 tons per ton, saving 76% of water,' Factory Director Huang took out an energy consumption comparison table. 'Last year, when supplying a listed company, they calculated: using our colored acrylic sliver saved 30% on water fees and sewage treatment fees alone in the dyeing and finishing process, and their carbon emission report even got a Grade A.' In recent years, with the tightening of the 'dual carbon' policy, more and more customers have taken the initiative to找上门. Antai's dope-dyed acrylic sliver production capacity has expanded from the initial 3,000 tons/year to 12,000 tons/year, yet it still cannot meet the demand.
Facing the market pattern where 'the Yangtze River Delta and Pearl River Delta account for 62% of the national production capacity' and the trend of central and western provinces attracting capacity relocation with electricity price incentives, Li Xiong has his own 'offensive and defensive strategy'. 'We rely on the industrial cluster advantages of Zhangjiagang — raw material suppliers and logistics hubs are all within 50 kilometers. Customers place orders in the morning, and we can provide samples in the afternoon. But just defending isn't enough; we need to "position" ourselves with technology.' Last year, a spinning mill in central and western China tried to seize orders with low prices, but after customers tested the products, they found that Antai's acrylic sliver not only had higher color consistency (batch difference controlled at △E ≤ 1.5) but also had 15% higher breaking strength than the competitor's. 'Now they have instead become our partners, using our dope-dyed acrylic sliver to make fancy yarns and then selling them to the local market,' Li Xiong笑道 (smiled). 'Price wars can't beat technological gaps. What customers want is "accurate color, low loss, and compliance" — that's the confidence built by our 30 years of accumulation.'
From 2 production lines for yarn when it was founded in 1993 to now having 6 intelligent spinning production lines and 3 provincial-level technology R&D centers, Antai Textile's 'stubbornness' is hidden in the details: the color card wall in the workshop displays over 2,000 color samples, all 'exclusive colors' customized for customers over the years; in the laboratory's aging test chamber, acrylic sliver is undergoing extreme temperature tests from -30℃ to 70℃ to ensure stability in outdoor environments. 'Last month, an old customer said that the acrylic yarn they bought from us 10 years ago, made into a carpet, still looks as new in color,' Li Xiong flipped through the customer feedback form, his eyes filled with pride. 'This is Antai's duty — to perfect a single yarn, reassure customers, and let the industry see the possibility of green textiles.'
Now, standing at the starting point of the 2025 industry plan, Antai Textile has already launched a new expansion plan: building 2 more dope-dyeing production lines, aiming to reduce carbon emission intensity by another 10% and expand the color spectrum to 60. 'After the new lines are put into production, we can provide samples of special colors like "aurora purple" and "rattan yellow" requested by customers on the same day,' Factory Director Huang looked at the new workshop under construction in the factory area, his tone firm. And Li Xiong's phone keeps ringing; the latest message is from an overseas customer: 'I heard your dope-dyed acrylic fiber has passed the EU ECO-TEX® certification? We will use it for all our autumn and winter collections!'
Sunlight filters through the workshop's glass windows, shining on rolls of brightly colored acrylic sliver, much like the emerging green vitality of this industry. With 30 years of history, Antai Textile is weaving a new picture of low-carbon transformation in the textile industry with the power of a single yarn.