Antai Textile: Weaving the Future of High - end Customization with Iridescent Acrylic Tops, Leading the Industry's Green Innovation Trend with Three - decade Ingenuity
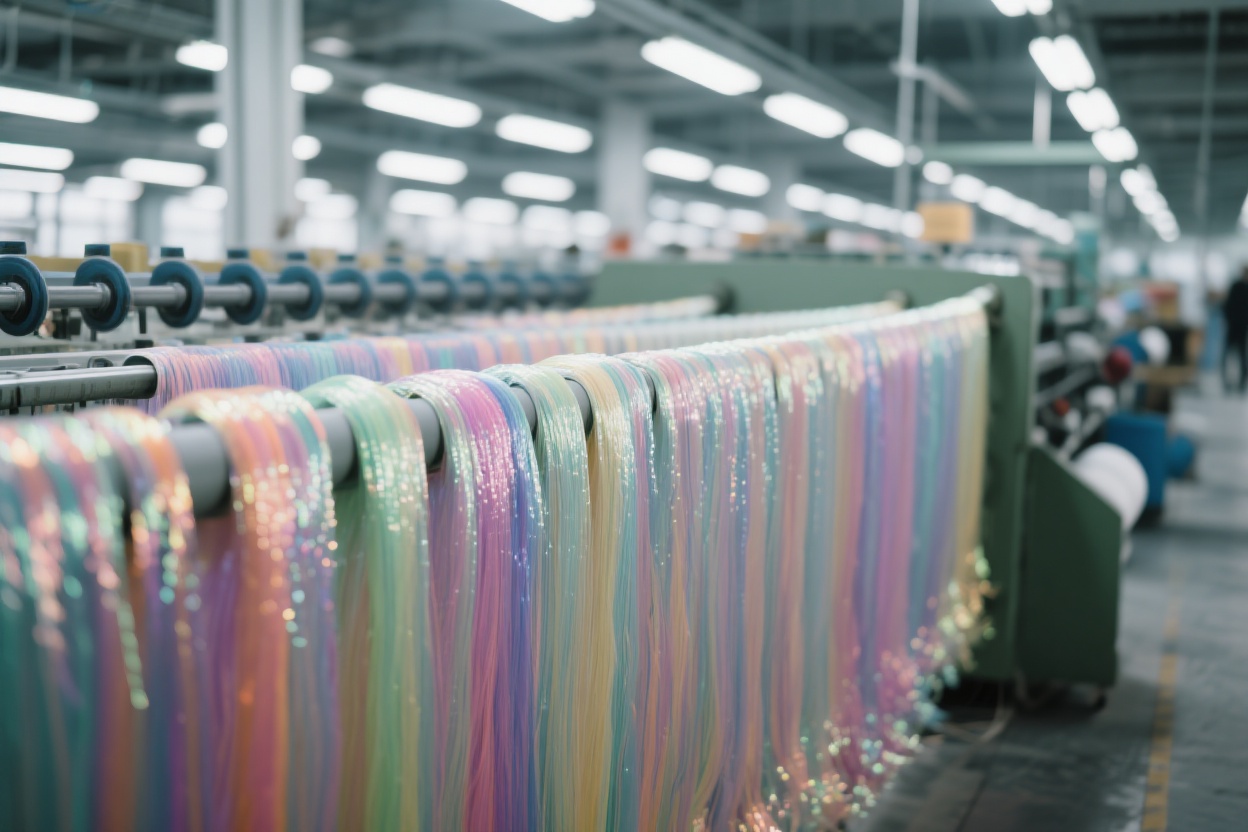
In July in Zhangjiagang, the sunlight shines through the glass windows of Antai Textile's office building and falls on the industry report spread out by Li Xiong, the marketing department manager. A news item popping up on the screen catches his eye - AruGaw has just released the preview of its 2026 'Weaving Spring' custom fashion show, with the theme of 'coexistence of natural textures and colors', indicating the urgent demand for differentiated yarns in the high - end customization market. He picks up his phone and dials the production department: 'Manager Huang, it's time for that batch of 'iridescent acrylic tops' we stocked last year to 'take the stage'.' Behind this conversation lies Antai Textile's over - three - decade industry acumen. Since it was established in Zhangjiagang in 1993, this enterprise mainly engaged in acrylic yarns, acrylic tops, colored acrylic tops, and fancy yarns has been like an experienced weaver, always able to catch the subtlest threads from the industry trends. The 'iridescent acrylic tops' mentioned by Li Xiong are a featured product developed by the team in response to the recent customization trend. Through precise control of the dyeing process, the acrylic fibers present a gradient luster under different light conditions, retaining the warm and fluffy characteristics of acrylic while meeting the designers' imagination of 'breathing colors'. 'Events like the 'Weaving Spring' fashion show essentially release market signals: future clothing will no longer be standardized products but carriers of emotions and aesthetics.' Li Xiong points to the sample book on his desk, in which more than 500 color numbers of acrylic tops are neatly arranged. From Morandi color systems to high - saturation color clashes, each one is marked with corresponding color fastness and environmental protection indicators. 'Last week, we received inquiries from three designer studios, specifically asking for yarns that can 'tell stories'. Our colored acrylic tops avoid the color difference problem of traditional dyeing from the dope - dyeing stage, exactly hitting their pain points.' In the production workshop, Manager Huang is leading the technical team to debug the newly upgraded air - jet spinning equipment. The real - time data jumping on the screen shows that the hairiness of this batch of fancy yarns supporting the 'iridescent acrylic tops' is 15% lower than the industry standard, and the breaking strength is increased by 8%. 'This is not just a simple parameter optimization.' Manager Huang picks up a piece of 'slub acrylic yarn' just off the production line, and the yarn surface shows a natural knot texture. 'A while ago, we saw that Shenghong Dyeing launched a full - process fluorine - free solution, and we immediately initiated the 'green production campaign'. Now, from raw material screening to dyeing and finishing processes, we use environmentally friendly auxiliaries across the board. For example, in the setting process of this yarn, we use the self - developed biological enzyme treatment technology, which not only reduces energy consumption by 20% but also has passed the OEKO - TEX® Standard 100 certification, obtaining the 'passport' to enter the high - end EU market.' Thirty years ago, Antai Textile started with a single acrylic top spinning machine. Now it has built a full - industrial - chain production line covering raw material R & D, spinning, dyeing, and testing, with an annual production capacity exceeding 8,000 tons. Its products are long - term suppliers to well - known domestic and foreign clothing brands and home furnishing enterprises. 'Many people say that acrylic is a 'niche fiber', but we insist on making a 'big deal' out of it.' Li Xiong says proudly. The 'antibacterial acrylic yarn' developed by the company has been applied to outdoor clothing brands, and the 'flame - retardant acrylic tops' have become the designated raw material for high - speed train seat fabrics. 'The 'dope - dyed acrylic imitating cashmere' technology攻克 by the technology department last year controls the cost at one - third of that of cashmere but can achieve 90% similarity. Now the orders are scheduled until the end of the year.' As the textile exhibition season in the second half of the year approaches, Li Xiong and his team are busy preparing for the New York International Apparel Fabrics and Home Textiles Sourcing Show in late July. In the sample room, several fancy yarns integrating Chinese traditional patterns are particularly eye - catching - this is the 'Oriental Aesthetics' series customized for the North American market. 'Exhibitions are not only for product display but also windows to observe global trends.' Li Xiong looks out of the window at the busy logistics trucks in the factory area. 'From Zhangjiagang to New York, from acrylic tops to custom yarns, what Antai aims to do is always to be the 'invisible tailor' who weaves the industry trends into the products.' The machines in the workshop are still roaring. A message pops up on Manager Huang's phone: the first batch of 'iridescent acrylic tops' just off the production line has been sent to a Shanghai designer studio via a logistics company. The light from the screen shines on his glove full of cotton wool. Those hands have woven Antai's early days and are now weaving the future of the textile industry, where green and innovation are intertwined.