Antai Textile's 32-Year Commitment to the Acrylic Fiber Track: Dual-Drive Forges Core Competitiveness in Colored Acrylic Fiber
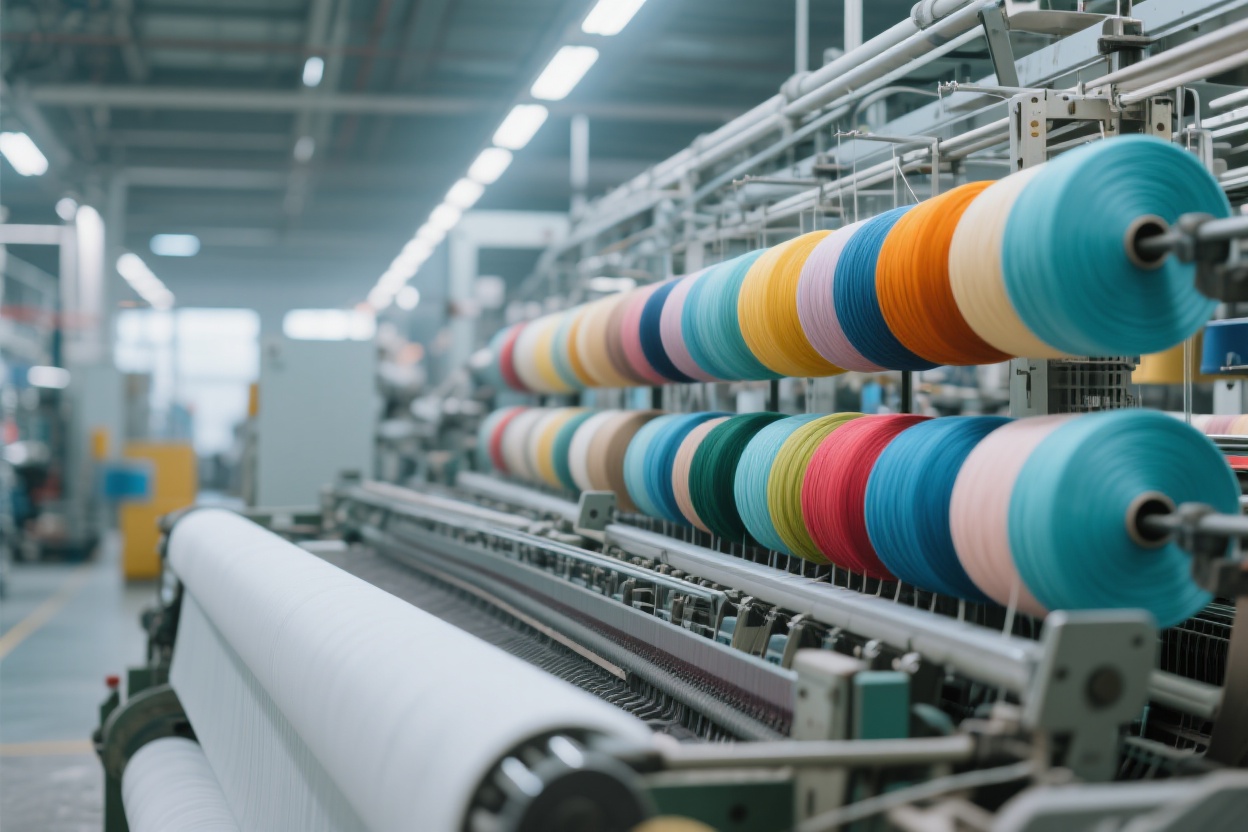
At 7:30 in the morning, as the sunlight in Zhangjiagang, Jiangsu, had just spilled over the glass windows of Antai Textile's administrative building, the latest market dynamics of acrylonitrile popped up on the computer screen of Li Xiong, the Marketing Department Manager: Shandong Haijiang's 130,000-ton/year plant had a temporary shutdown for maintenance, Lihuayi's spot price dropped by 50 yuan/ton, Jilin Petrochemical's new 260,000-ton plant would start production at the end of the month... His fingertips slid across the screen, circled the number "acrylonitrile inventory 45,800 tons, weekly increase of 3,000 tons", and immediately dialed the Production Department: "Director Huang, the wind direction on the raw material side has changed. We need to optimize the cost plan for the urgent order of 'three-color acrylic sliver' we finalized last week, taking advantage of this market trend."
On the other end of the phone, Huang Weiguo, the Director of the Production Department, was standing in front of the central control screen of the intelligent spinning workshop. The jumping parameters on the screen showed the operation status of the third colored acrylic sliver production line - this was the "dope dyeing demonstration line" that Antai Textile had just put into operation in 2024, capable of achieving a full-process closed loop from acrylonitrile raw material to colored fiber. "Don't worry," Director Huang's voice had the unique metallic texture of the workshop, "the process iteration completed last week has reduced the unit consumption of acrylonitrile by another o.8%. Even if raw material prices fluctuate, the cost advantage of our new colors 'Aurora Purple' and 'Mist Gray Blue' can still hold."
This early morning conversation holds the "survival code" of Antai Textile's 32-year development. When it started from a piece of tidal flat in Zhangjiagang in 1993, this textile enterprise had already anchored the niche track in the acrylic fiber field; today, while traditional textile enterprises are still anxious about the rise and fall of raw material prices, Antai Textile has long established a firm foothold in the blue ocean of colored acrylic fiber (dope dyeing acrylic fiber) through the dual-drive of "market acumen + technological strength".
The "Stability" Strategy Amid Raw Material Fluctuations: From "Passive Response" to "Proactive Layout" As the "grain" for acrylic fiber production, the price and supply of acrylonitrile directly affect the nerves of the entire industrial chain. When the news of Shandong Haijiang's plant maintenance came out in early July, many peers began to panic - short-term supply tightening might push up raw material costs. However, in Antai Textile's raw material warehouse, a 30-day safety stock was quietly lying in constant temperature tanks. "This is not luck, but a pattern," Li Xiong pulled out the raw material monitoring chart on his mobile phone, which marked the maintenance cycles of acrylonitrile plants and price fluctuation curves in the past five years. "The peak maintenance season is from the end of the second quarter to the beginning of the third quarter every year. We locked in long-term agreement prices with core suppliers like Jilin Petrochemical and Lihuayi three months in advance. Coupled with the self-built raw material price early warning model, we are not afraid of fluctuations."
What's more critical is the "internal strength" on the production side. Director Huang led the reporter to the "dope dyeing laboratory" in the workshop, where several technicians were debugging a small spinning machine, and the blue spinning solution in the beaker had a uniform luster. "Traditional acrylic fiber dyeing requires multiple processes such as scouring, dyeing, and fixing, which consumes water and electricity and is prone to color differences. Our dope dyeing technology 'plants' pigments into the fibers during the acrylonitrile polymerization stage, with color fastness reaching level 4 or above, saving 70% water and 30% energy." He pointed to the process improvement list on the wall, "Take last month as an example. After Lihuayi lowered its acrylonitrile quotation, we immediately optimized the formula and directly passed on the saved costs to customers. A customer in Zhejiang that makes high-end outdoor clothing immediately added an order for 200 tons of 'anti-ultraviolet acrylic yarn' on the spot."
The "Innovation" Strategy in Industrial Upgrading: From "Following the Market" to "Leading Demand" When the news of Jilin Petrochemical's new 260,000-ton acrylonitrile plant going into production came, Antai Textile's R&D team was already preparing for the next "big move". "Adequate raw material supply means we have more room for innovation," Li Xiong took out a "2025 Q3 Color Trend Report", which circled keywords such as "low-saturation Morandi color system" and "functional composite color". "For example, this 'Cloud Soft Pink' acrylic sliver is blended with 15% recycled acrylic fiber. It can not only meet the aesthetic demand of Generation Z for 'gentleness' but also comply with the ESG requirements of brand customers. It just hit the market last month and received a quarterly order from a fast fashion brand."
This accurate capture of market demand stems from Antai Textile's "customer insight database" accumulated over more than 30 years. From initially providing basic acrylic yarn to local wool mills to now serving more than 200 brand customers at home and abroad (including sports apparel, home textiles, toys, etc.), the company has established a full-chain feedback mechanism covering "raw material - production - application". "At the Shanghai Home Textiles Exhibition last week, a customer proposed 'hoping for better flame retardancy of acrylic sliver'. Our technical team produced a sample in three days - adding an environmentally friendly flame retardant to the dope, achieving a combustion grade of B1 without affecting the hand feel," Director Huang said, picking up a ball of light gray acrylic sliver and twisting it gently; the fiber was soft but not easily deformed. "This is Antai's confidence: others compete on price, we compete on value."
32 Years in Textiles: Writing the Industry Answer with "Specialized, Sophisticated, Distinctive, and Novel" From six old spinning machines in 1993 to today's modern production base covering 200 mu (about 133,333 square meters) with an annual capacity of 30,000 tons; from a single acrylic yarn product to a full-category matrix covering acrylic sliver, colored acrylic sliver, and fancy yarn - Antai Textile's growth history is a microcosm of China's textile industry's transformation from "scale expansion" to "quality improvement". "Last year, we were selected as a 'Jiangsu Provincial Specialized, Sophisticated, Distinctive, and Novel Small and Medium-sized Enterprise', relying on our technological accumulation in the field of dope dyeing acrylic fiber," Li Xiong said proudly. The company currently holds 12 invention patents, among which the "multi-color co-spun acrylic sliver production process" has filled a domestic gap.
In the workshop, robotic arms are neatly stacking rolls of packaged colored acrylic sliver, which are about to be shipped to a toy factory in Guangdong; in the laboratory, samples of the new season's "gradient acrylic yarn" have passed third-party testing; in the meeting room, Li Xiong and Director Huang are looking at the production schedule of the new acrylonitrile plant and discussing the next round of capacity planning... In today's ever-changing textile industry, Antai Textile has proven through 32 years of persistence: true competitiveness has never been about following trends and chasing hotspots, but about, after seeing the trend clearly, calming down to take "professionalism" to the extreme - just like the colored fibers slowly drawn out from the spinning machine, each one hides a dedication to quality, and each strand weaves the future of industrial upgrading.