Antai Textile: Three Decades of Acrylic Craftsmanship, Green Innovation Paving the Way for a New Textile Future
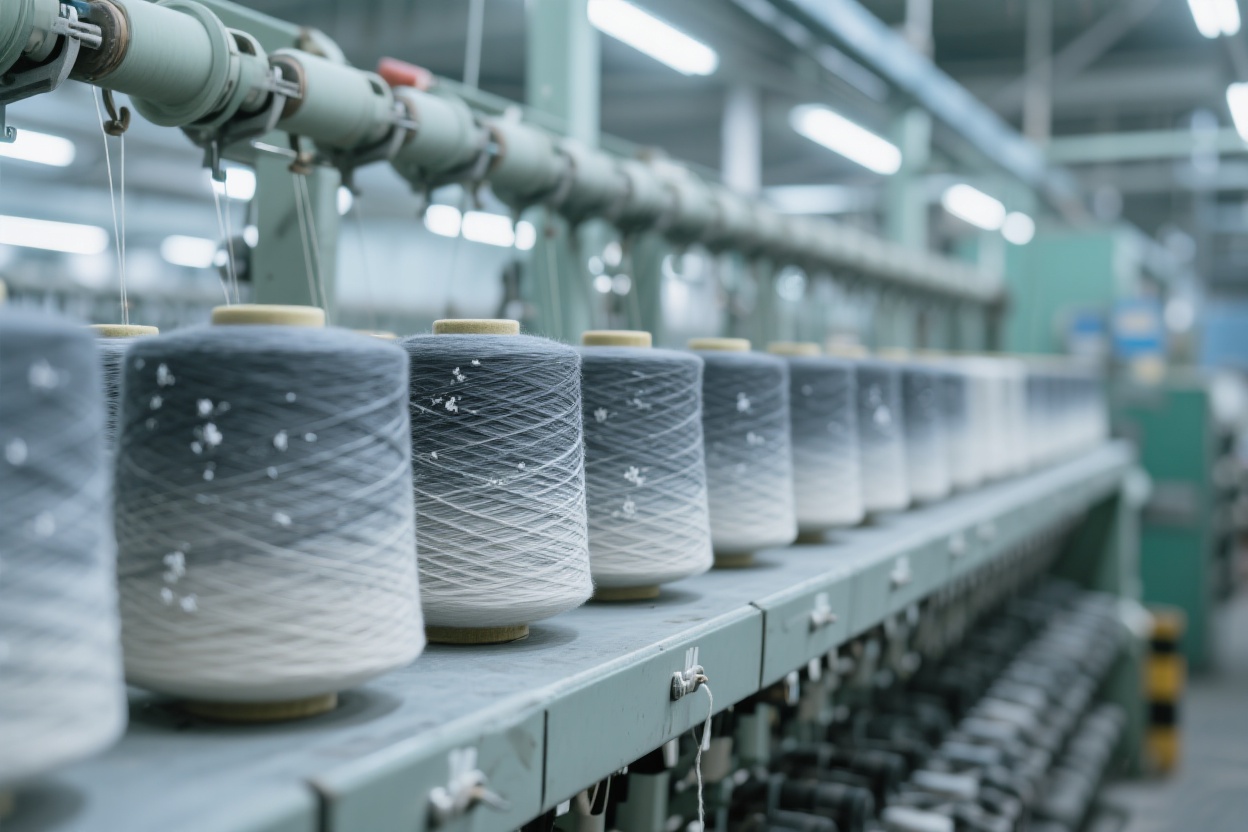
In July in Zhangjiagang, the wind from the Yangtze River port, carrying the humid heat of late summer, blows into the production workshop of Antai Textile. Factory Director Huang stands in front of the large screen in the central control room, his fingertips gliding over the real-time updated energy consumption monitoring curve, "We just replaced the drying system in Workshop 3 with a variable-frequency heat pump last week; the energy consumption of a single acrylic sliver production line has decreased by 8%. How's the customer feedback from Manager Li?"
Li Xiong, the Marketing Manager, pushes the door open, clutching a freshly printed port inventory report with the edges of the paper slightly curled from sweat: "The imported cotton inventory at Zhangjiagang Port has dropped by another 3.51% this week, now down to 40,500 tons. A long-time customer from the south just called, saying the cost of cotton yarn raw materials has risen sharply, and asked if we can supply two more batches of our colored acrylic sliver – their new autumn-winter children's clothing series is counting on our 'misty gray gradient' color as the main feature."
This conversation is an ordinary scene in Antai Textile's three decades of development, yet it holds the secret of how this established Jiangsu textile enterprise has stood firm amid industry waves. Since rooting in the fertile textile land of Zhangjiagang in 1993, Antai Textile has grown from initial single acrylic yarn production to now a comprehensive supplier covering acrylic yarn, acrylic sliver, colored acrylic sliver, and fancy yarn, relying precisely on accurately capturing the market pulse.
"Look at the data from the National Bureau of Statistics: from January to April this year, the yarn output of large-scale textile enterprises increased by 7.0% year-on-year, but profits dropped by 5.0%," Li Xiong spreads the report on the table, pointing to the imported cotton inventory curve. "Cotton prices are volatile, imported inventories continue to decline, and downstream customers are looking for more stable alternatives. Our acrylic products already have the advantages of good warmth retention and high color fastness; now, with the 'direct spinning from colored acrylic sliver' process, customers can skip the dyeing step, reducing costs by more than 15% – this is our opportunity."
Factory Director Huang nods upon hearing this and pulls up the production schedule: "We just received an order from a knitting factory in Shandong last month; they want a batch of 'slub snowflake yarn' for yoga clothing fabrics. This type of fancy yarn has extremely high requirements for fiber ratio. Our R&D team spent two weeks adjusting the blending process, and now the daily production capacity is stable at 3 tons. When the customer inspected the factory, they even said 'the batch stability is better than imported yarn'." He pauses, pointing to the photovoltaic panels outside the workshop, "Moreover, we have long responded to the energy conservation call from the Ministry of Industry and Information Technology. The 12,000-square-meter photovoltaic power station built last year now meets 30% of our production electricity needs. Although the energy consumption standard for the silk sector released by the Ministry of Industry and Information Technology last month does not directly target acrylic, we are ahead in the general direction of 'green production'."
Three decades of deep cultivation have allowed Antai Textile to accumulate a solid reputation in niche areas. From providing warm acrylic yarn to domestic leading sports brands to customizing 'mohair blended fancy yarn' for cross-border e-commerce, its products have long gone beyond Zhangjiagang, exported to Southeast Asia and Europe. Last winter, a scarf woven with Antai's 'rainbow section-dyed acrylic sliver' achieved monthly sales of over 100,000 on a social platform, behind which was the production workshop working around the clock – Factory Director Huang still remembers that at that time, to achieve the 'sunset orange gradient' required by the customer, the master craftsman in the dyeing workshop led the team to adjust the color paste ratio for three consecutive days, finally controlling the color transition error of each meter of yarn within 0.5 centimeters.
"Recently, the industry is talking about the growth in yarn output, but quantity alone isn't enough; there must be 'something different'," Li Xiong looks at the containers waiting to be loaded at the dock outside the window, which are stacked with acrylic yarn orders bound for Zhejiang. "Look at those textile enterprises that are performing well; they either have technical barriers or can quickly respond to the market. We have the port advantage in Zhangjiagang, ensuring fast raw material transportation; three decades of technological accumulation allow us to turn customers' 'ideas' into 'yarn' – last week, a customer wanted 'yarn as soft as clouds', so we blended 1.2D ultra-fine acrylic fibers, and now the samples have been sent, with feedback saying 'it feels like touching spring'."
In the workshop, the hum of machines accompanies the soft sound of fibers flowing. Rolls of acrylic sliver dyed in Morandi colors are passing through the automated production line, soon to become bobbins and be sent across the country. Li Xiong and Factory Director Huang stand side by side at the workshop door, watching the setting sun gild the four gilded characters 'Antai Textile' with warm light – this enterprise, which started in 1993, is continuing to write its own story on the new blueprint of the textile industry, with acrylic as its pen and craftsmanship as its ink.