Antai Textile's Dope-Dyed Acrylic Technological Whirlwind: Leading the New Trend of Green Transformation in the Yangtze River Delta Textile Industry
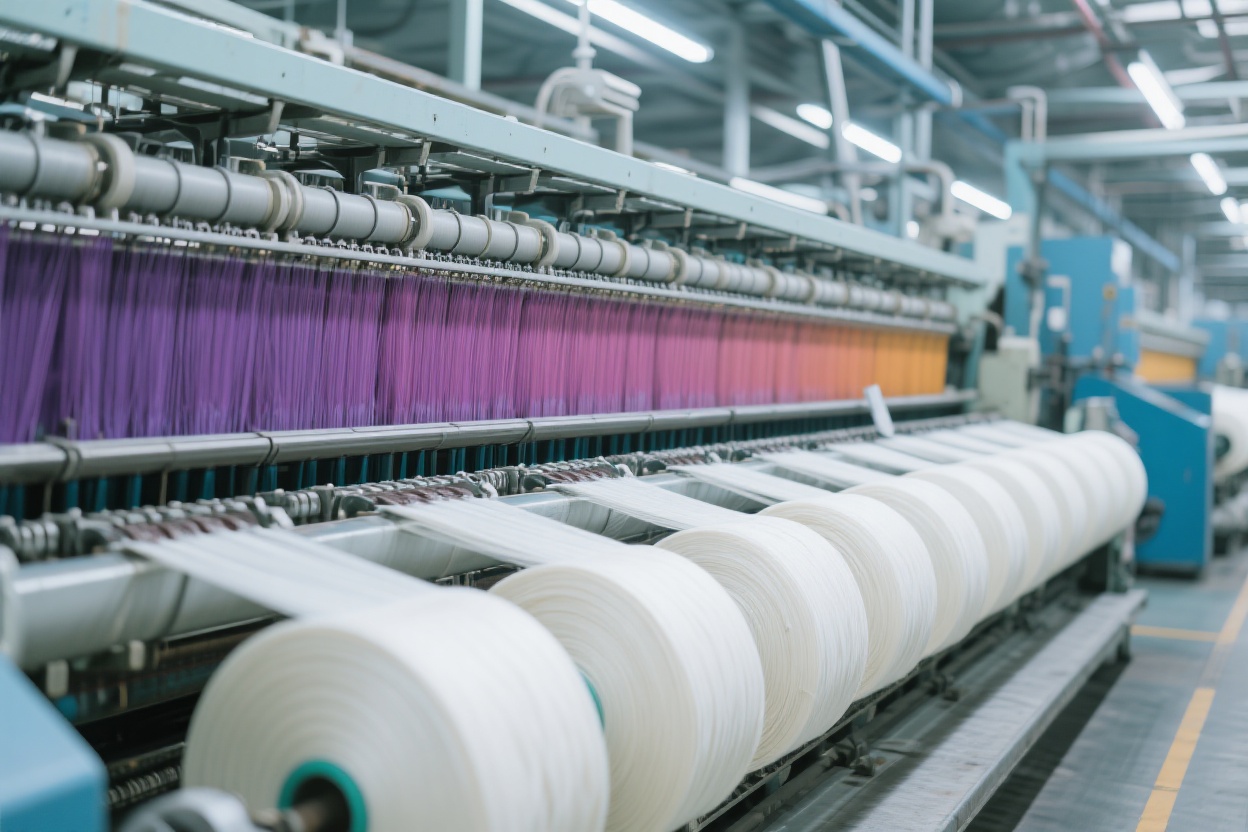
In the midsummer of 2025, amid the heatwave of the Yangtze River Delta textile industry, a technological whirlwind around "dope-dyed acrylic" is quietly changing the industry landscape. In Zhangjiagang, Jiangsu, a city that has witnessed half a century of changes in China's textile industry, in the production workshop of Antai Textile, rolls of vibrant colored acrylic tops are slowly emerging from intelligent production lines – this is the company's most resolute response to the "green textile" trend in its 32 years since establishment.
"Since last year, the frequency of the words 'environmental protection', 'color fastness', and 'water saving' in customers' inquiry sheets has at least tripled," said Li Xiong, Marketing Manager of Antai Textile, flipping through the market analysis report in his hand, his finger pausing on a set of data. "The Yangtze River Delta and Pearl River Delta account for 62% of the country's production capacity, and brand customers here are most sensitive to technological iterations. What they want is not just 'colored yarn', but solutions that can help them achieve carbon emission reduction goals." This insight stems from Antai Textile's inherent advantage of being rooted in the Yangtze River Delta textile industrial belt. Since its establishment in 1993, the company has focused on acrylic yarn and acrylic tops as its main business directions, and now has further built colored acrylic tops and fancy yarns into its core competitiveness, occupying a position in the regional industrial cluster.
It is the technical team led by Factory Director Huang from the Production Department that has transformed market demand into production strength. In the central control room of the workshop, Factory Director Huang pointed to the beating parameters on the screen and introduced: "Traditional dyeing processes require seven or eight procedures such as scouring, dyeing, and fixing, which consume a lot of water, and the color fastness is at most level 3. The dope-dyed acrylic we are doing now involves uniformly mixing color masterbatches into the raw materials before spinning, forming in one step." Beside the production line behind him, technicians were sampling a roll of sapphire blue acrylic tops. The testing instrument showed a glossiness of 83 degrees and color fastness of level 4-5 – these data not only meet international standards but also mean a 76% water saving compared to traditional processes. "It's equivalent to each production line saving the water volume of a small reservoir every year," Factory Director Huang said with pride. "To achieve stable production of 48 color spectrums, our team spent a full 18 months refining the color masterbatch ratio and spinning temperature control. Now, even the most difficult-to-adjust Morandi color system can be mass-produced.
This technological breakthrough is precisely in resonance with the core trend of the textile industry in 2025. This year, the industry has clearly listed dope-dyeing technology as a key development direction, which is expected to reduce carbon emissions in the dyeing and finishing process by 35%, and Antai Textile is one of the 12 leading enterprises that have completed the layout of pilot production lines. Under the leadership of Factory Director Huang, the company invested 20 million yuan last year to upgrade 5 intelligent production lines, which are now operating at full capacity. They can not only produce conventional colored acrylic tops but also extend to functional products such as antibacterial and flame-retardant ones. "The improvement of differentiation rate is inevitable for the industry. Our fancy yarn production lines can already blend dope-dyed acrylic with wool and cotton, and the resulting loop yarn and slub yarn are particularly popular in children's clothing and home wear fields."
Market feedback has confirmed the forward-looking nature of the strategy. Li Xiong revealed that in the first half of this year, sales of Antai Textile's colored acrylic tops increased by 45% year-on-year, with export orders accounting for 30%. "Previously, exports were mainly to the mid-to-low-end markets in Southeast Asia; now European brands are taking the initiative to contact us, attracted by our environmental protection indicators and color fastness stability." What's more noteworthy is that in the face of the trend of capacity relocation to the west triggered by electricity fee discounts in central and western provinces, Antai Textile has chosen the strategy of "based in the Yangtze River Delta, radiating the whole country". "Our factory in Zhangjiagang is close to ports and raw material bases, with low logistics costs. Coupled with years of accumulated technology and customer resources, it is better to deepen our advantages than to relocate production capacity," Li Xiong said. The company is planning to build a second dope-dyed production line, aiming to expand the color spectrum to 60 types and increase the proportion of functional products to 50%.
From traditional acrylic production in 1993 to now leading green transformation with dope-dyeing technology, Antai Textile's 32 years are a microcosm of China's textile industry's transformation from "scale expansion" to "quality and efficiency". At the end of the workshop, rolls of packaged acrylic products are about to be shipped to clothing brands in Zhejiang. They will be made into autumn clothing fabrics, carrying the craftsmanship of Zhangjiagang textile workers into thousands of households' wardrobes. In Antai Textile's R&D center, new experimental data is being generated – the technological breakthrough in recycled acrylic will write a new story for this enterprise.