Antai Textile: Technological Innovation Drives the Explosion of Functional Acrylic Fibers, and Doubled ASEAN Orders Lead the Industry Transformation
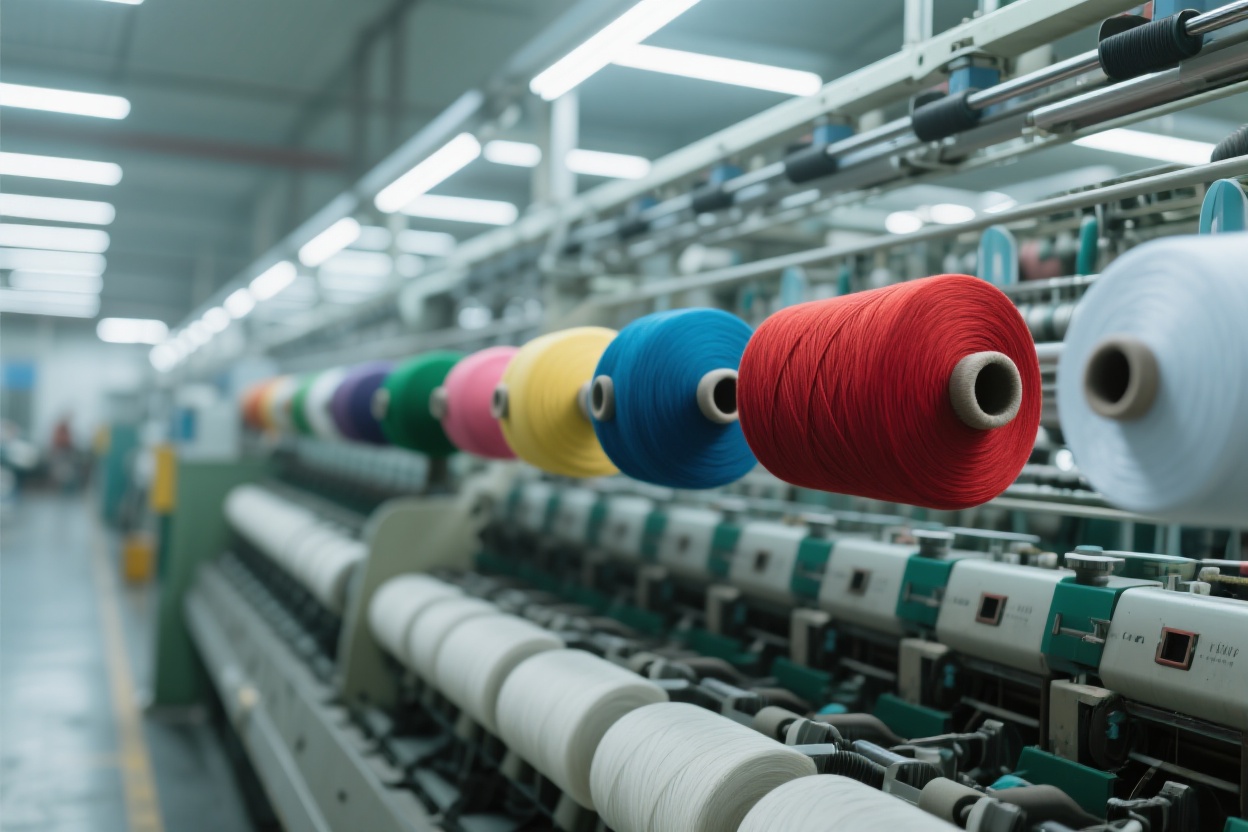
In the early summer in Zhangjiagang, the gentle breeze carries the moist air from the Yangtze River Estuary and blows over the newly sprouted camphor trees in the Antai Textile factory area. Li Xiong, the marketing manager, was clutching a letter of intent for an order from a Southeast Asian customer and striding quickly towards the production workshop. The demand from an Indonesian sportswear brand on this letter specifically asked for “high - color - fastness, environmentally friendly bright acrylic yarn”, and the quantity was nearly double that of the same period last year.
“Manager Huang, take a look at this,” Li Xiong handed the letter of intent to Huang Wei, the production manager who came up to greet him. “The demand for functional yarns from sportswear manufacturers in the ASEAN market has increased significantly. They said that the antibacterial bright acrylic yarn sample we sent last year was in great demand at the local exhibition.”
Huang Wei took the letter of intent and ran his fingertips over the words “color fastness of grade 4 - 5, water - saving process”. The wrinkles at the corners of his eyes relaxed. “This is thanks to the ‘dope dyeing’ technology we mastered three years ago. Do you remember? At that time, the industry used traditional dyeing methods, which consumed a lot of water and the colors faded easily. Our R & D team spent a full eight months in the workshop and finally stabilized the production of environmentally friendly acrylic slivers in 48 color spectra. Now we can save 76% of water, and the color fastness meets the standards. No wonder the market has come to us.”
In the workshop, acrylic slivers with a soft luster were gushing out from the end of the production line. Some had gradient Morandi colors, while others showed the matte texture unique to sportswear fabrics. This is a microcosm of Antai Textile's more than three - decade - long deep involvement in the acrylic fiber field. Since its establishment in Zhangjiagang in 1993, this enterprise that grew up in the textile cluster in the Yangtze River Delta has been focusing on the R & D and production of acrylic yarns, acrylic slivers, colored acrylic slivers, and fancy yarns. Now it has become a benchmark supplier of functional acrylic materials in East China.
“The industry trend is very clear now,” Li Xiong said firmly as he looked at the production line. “Recently, we conducted a market analysis. By 2030, the differentiation rate should be increased from 35% to 55%, and functional products such as flame - retardant and antibacterial ones are the focus. The new conductive acrylic yarn production line we launched this year is targeted at the smart - wear market. Also, the flame - retardant acrylic slivers required by home textile customers have passed European tests.” He paused and added, “The export market is also changing. The share of the European and American markets may drop to 40%, but the annual growth rate in ASEAN and the Middle East is 8%. We just set up an office in Dubai last month. Manager Huang, the high - temperature environment there requires high heat resistance of the yarn. We need to accelerate the mass production of our anti - ultraviolet acrylic yarn.”
Huang Wei nodded and pointed to the new equipment on the other side of the workshop. “Don't worry. The circular - economy production line is also being debugged. Currently, the proportion of recycled acrylic fibers is only 3%, but it will reach 12% in the future. We use recycled PET bottle flakes as raw materials, and the recycled acrylic slivers we produced have been sent as samples to several environmentally friendly home textile brands. The carbon emission intensity can be reduced by 18%. This is a major trend.”
As they were talking, a batch of newly produced acrylic - cotton blended colored yarns was packed and ready to be sent to customers in Guangdong. “Look at this,” Huang Wei picked up a roll of light - gray yarn. “The market scale of pure acrylic colored yarns will increase from 12 billion yuan to 15 billion yuan this year, and that of blended yarns will increase from 8 billion yuan to 10 billion yuan. The growth of functional yarns is even more remarkable, from 5 billion yuan to 7 billion yuan. We have kept up with all three product lines. Last month, we just received a large order from a Zhejiang customer for 100,000 meters of functional acrylic - cotton colored yarns for outdoor tents. They said they were attracted by the tear resistance and color fastness of our yarns.”
From the spinning of the first acrylic yarn in the workshop in 1993 to the present, when the products cover 48 color spectra and the annual production capacity of functional yarns has exceeded 8,000 tons, Antai Textile's thirty - year development is exactly a microcosm of China's textile industry's transformation from ‘scale expansion’ to ‘quality and efficiency’. When the textile clusters in the Yangtze River Delta are facing the challenge of westward relocation of production capacity, Antai chose to strengthen its foundation through technological innovation. While maintaining the core advantages of R & D and production at its Zhangjiagang headquarters, it has engraved ‘green’ and ‘functionality’ into the product genes through technological upgrades such as dope dyeing and the use of recycled raw materials.
“The Southeast Asian customers will come to our factory for an inspection next month,” Li Xiong looked at Huang Wei, and the two smiled at each other. “By then, let them see that we can not only produce yarns that meet international standards but also help them reduce the dyeing cost by 30%. This is the confidence for Antai to stand firm in the industry.”
The sound of the machines in the workshop remained steady. In the sunlight, the acrylic yarns wound on the reels were reflecting the faint light of the textile industry's transformation - the light of technological innovation and the firm steps of an established textile enterprise keeping pace with the times.