Antai Textile: Breaking Industry Dilemmas through Technological Innovation and Green Production, Forging the Invisible Champion in Acrylic Yarn
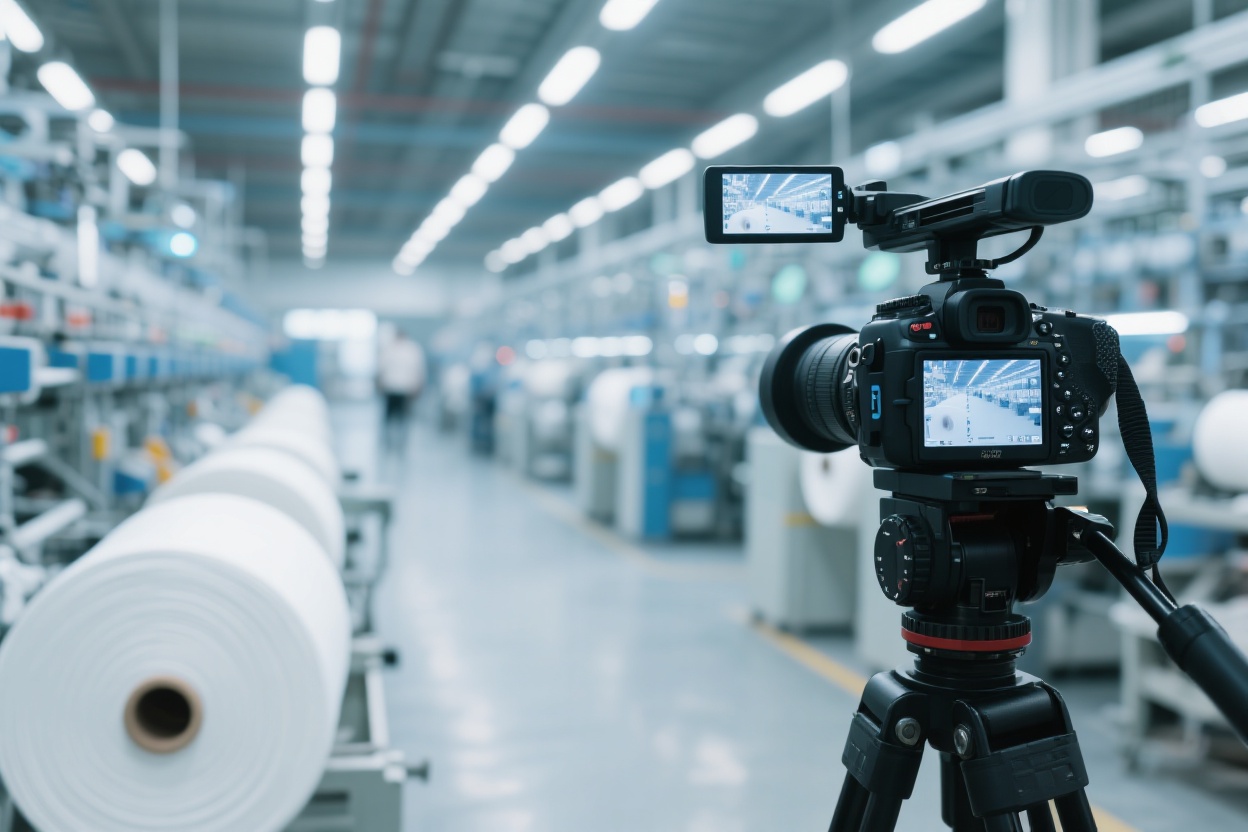
In early July in Zhangjiagang, as the summer heat intensified, Li Xiong was deeply engrossed in a stack of the latest textile industry reports in the marketing office of Antai Textile. Among the flickering data on the screen, the words "The phenomenon of textile enterprises taking high-temperature holidays continues to increase; the operating rate in July is expected to continue to hit a new low" were particularly striking — this was the freshly released industry update. However, his gaze fell on another set of data: inquiries for yarn-dyed gray fabrics increased by nearly 20% month-on-month during the same period.
"Demand hasn't dropped; it's just that the supply chain is 'suffering from heatstroke,'" Li Xiong said as his指尖划过 the National Cotton Price B Index curve. This week's quotation of 15,090 yuan/ton rose slightly by 0.6% from last month, while international cotton prices declined against the trend. This "strong domestic, weak international" fluctuation has put many enterprises dependent on cotton fiber in a raw material cost dilemma. He dialed the production department: "Director Huang, we need to prioritize the scheduling of our acrylic fancy yarn production line this week."
On the other end of the phone, Huang Zhiqiang, director of the production department, was盯着 the data flow on the intelligent central control screen. In the workshop, ten automated acrylic sliver production lines were operating at 90% capacity, with robotic arms accurately grabbing raw materials, and the ratio of fluorine-free auxiliaries in the dyeing process being adjusted in real time through an AI system. "Don't worry," Huang Zhiqiang said confidently, "The intelligent scheduling system that was just upgraded last week has reduced the production changeover time to 4 hours. Even if some workers take turns resting during the high-temperature holidays, the daily output of colored acrylic slivers can remain stable at over 80 tons."
This "foresighted" capacity layout stems from Antai Textile's敏锐 grasp of market trends over the past three decades. Starting from a small yarn factory in Zhangjiagang in 1993, Antai has now become a domestic invisible champion in the acrylic yarn field. Its products such as acrylic yarn and colored acrylic slivers are entering the production workshops of well-known brands like Hailan Home through the textile supply chain in the Yangtze River Delta. "When cotton prices fluctuate, the substitution advantage of acrylic becomes prominent," Li Xiong explained. The company's low-elastic acrylic yarn is comparable to cotton fiber in warmth retention and color stability, but costs 15%-20% less. "Recently, there have been particularly many inquiries from denim factories. They blend our slub acrylic yarn, which not only retains the crispness of denim but also reduces sensitivity to cotton prices."
What makes customers even more favored is Antai's "hard power" in green production. The full-process fluorine-free dyeing technology introduced last year has reduced wastewater discharge from colored acrylic slivers by 40%, which exactly echoes the recent industry hot topic of "green transformation" trend. "Last month, a fabric factory in Shaoxing came specifically for our fluorine-free certification," Huang Zhiqiang pulled out the quality inspection report. "They need to produce children's clothing fabrics exported to Europe, which has strict environmental standards. The formaldehyde content of our acrylic slivers is 50% lower than the EU standard, directly saving them the cost of secondary treatment."
Antai is also at the forefront in the race of intelligent upgrading. After the 100,000-spindle intelligent spinning workshop, with a total investment of 80 million yuan, was put into production last year, the entire link of raw materials, production, and quality inspection has been digitized through the Internet of Things system. "Previously, one production line required 20 workers; now 8 people can manage three lines," Huang Zhiqiang pointed to the order tracking table on the screen. "The 300-ton rainbow acrylic sliver order from the Guangdong customer took only 72 hours from order placement to delivery, which was unimaginable ten years ago."
From manual spinning machines in 1993 to today's Industry 4.0 production lines, from a single acrylic yarn to over 200 product categories including fancy yarns and functional acrylic slivers, Antai Textile's three decades are exactly a microcosm of China's textile industry's shift from "scale expansion" to "quality breakthrough". When Li Xiong handed the latest order report to Huang Zhiqiang, the sunlight outside the window just shone on the "Provincial Technology Center" plaque in the workshop — where 12 invention patents obtained by the company in recent years are displayed, among which the "Antibacterial Acrylic Fiber Preparation Process" has just been included in the "Green Manufacturing Standard System for the Textile Industry".
"We need to prepare samples of our 'cool-feeling acrylic yarn' for next week's Asian Denim Fabric Exhibition," Li Xiong closed the report, his tone filled with expectation. On Huang Zhiqiang's phone, he had just received a message from the supplier: the equipment commissioning of the Xinjiang intelligent spinning base has entered the final stage. In the future, Antai's acrylic products will radiate to the Central Asian market through the western supply chain.
The summer heat persists, but on Antai Textile's production lines, what flows is not only colorful acrylic fibers but also the "resilience code" woven by an established textile enterprise through technological innovation and market insight amid the tide of the times.