Antai Textile: 32 Years of Deep Cultivation in Acrylic Fiber, Driven by Technological Innovation and Green Transformation to Seize the Global Market
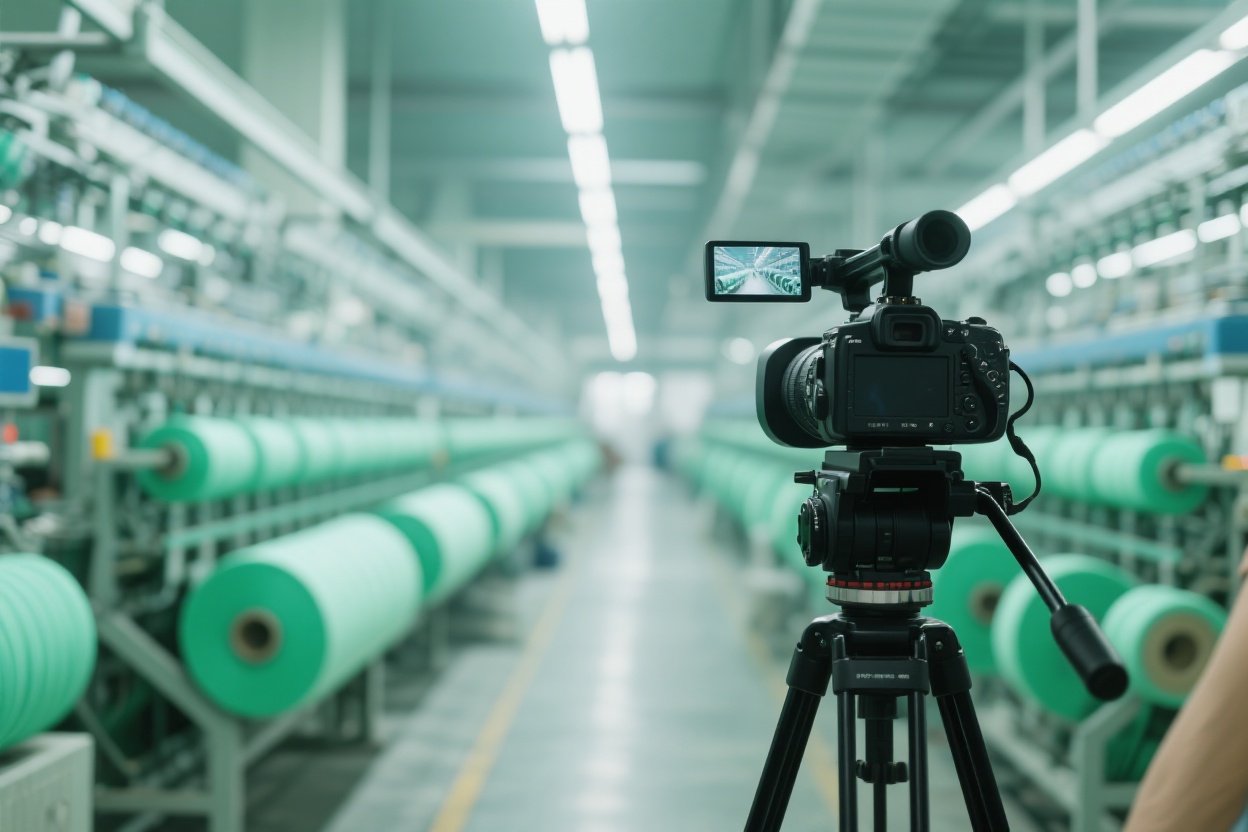
In the midsummer of 2025 in Zhangjiagang, intelligent spinning equipment is operating at a steady rhythm in the production workshop of Antai Textile, with rolls of uniformly colored acrylic sliver slowly output from the production line. Factory Director Huang of the Production Department stood in front of the large screen in the central control room, his fingertips gliding across the real-time data curves: "Look at this energy consumption figure: 820 kWh per ton of yarn, nearly 15% lower than the industry average." In the Marketing Department of the office building, Manager Li Xiong had just hung up a video call with a European client, his notebook densely filled with new requirements: "The procurement volume of 'zero-dyeing and finishing' acrylic products in the EU market has increased by another 20% this quarter." Since establishing roots in Zhangjiagang in 1993, this enterprise, which has deeply cultivated the acrylic fiber field for 32 years, is steadily moving forward in the wave of green transformation and consumption upgrading in the textile industry, driven by the 'dual wheels' of technological iteration and market insight.
"We predicted three years ago that dope dyeing technology would become the key to breaking the industry's bottleneck," Li Xiong pulled out a 2022 market research report, on the yellowed pages, a line was circled: "Carbon tariff policies in the global textile industry will force emission reductions at the upstream material end." At that time, the domestic acrylic fiber industry still mainly relied on traditional dyeing and finishing processes, with carbon emissions per ton of yarn in the dyeing process as high as several hundred kilograms. Antai Textile immediately formed a special team, led by Factory Director Huang, to tackle the stable production technology of dope-dyed acrylic sliver in collaboration with the Textile Research Institute of Jiangnan University. "The most difficult part was color fastness and batch consistency," recalled Factory Director Huang. "We adjusted 137 sets of formulas, and finally completed the pilot production line layout in 2024, becoming one of the first enterprises in the industry to achieve large-scale production of dope-dyed acrylic sliver." Today, this technology has enabled Antai Textile's colored acrylic products to reduce carbon emissions in the dyeing and finishing process by more than 35%, exactly aligning with the industry's main direction of 'green production' in 2025, and also allowed it to seize the initiative in cross-border e-commerce channels—data shows that in 2023, the export volume of domestic acrylic blended products exceeded 450,000 tons, and Antai Textile's colored acrylic sliver, relying on the 'low-carbon label', has seen orders from the US and EU markets account for 60% of total overseas orders.
Changes in market demand have always been the 'compass' for Antai Textile to adjust its product strategy. Li Xiong has recently been frequently traveling to and from the headquarters of sportswear brands in the Yangtze River Delta: "What customers want is not just 'colored', but more importantly 'functional'." He picked up a roll of light gray bright acrylic yarn: "This is our newly developed 'cool-feeling antibacterial yarn', which is added with nano-level cooling particles and antibacterial additives. Its moisture absorption and sweat-wicking rate is 40% higher than that of ordinary acrylic fiber, and we have already received a 3,000-ton order from a leading sportswear brand." Behind this is the company's precise capture of demand trends: In 2023, the proportion of domestic industrial textiles in the apparent consumption of acrylic fiber has risen to 18%, and the demand for functional bright acrylic yarn in the sportswear and casual wear market has an annual growth rate of over 12%. To meet this incremental demand, Antai Textile introduced bio-based acrylonitrile preparation technology in 2024, relying on the 10,000-ton demonstration unit put into operation by Wanhua Chemical, increased the proportion of renewable raw materials to 8%, and with the new polymerization process, the raw material cost of functional bright acrylic yarn has been reduced by 10%. "Cost has decreased, but quality cannot be compromised," said Factory Director Huang, pointing to the intelligent testing equipment in the workshop. "Each meter of yarn undergoes 32 quality inspections, and indicators such as breaking strength and evenness are all uploaded to the system in real-time; unqualified products cannot leave the workshop at all."
From the initial single acrylic yarn production to the current full-category layout covering acrylic yarn, acrylic sliver, colored acrylic sliver, and fancy yarn, Antai Textile's development trajectory is a microcosm of the transformation and upgrading of China's acrylic fiber industry. Over the past 32 years, the company has witnessed the consumption shift of acrylic fiber from 'warmth necessity' to 'functional upgrading' and has also personally experienced the industrial transformation from 'scale expansion' to 'quality winning'. Today, in the track of the acrylic-cotton blended dyed yarn market with an average annual growth rate of 4.3%, the proportion of Antai Textile's high-end products has increased from 35% in 2023 to 42%, green product market share has exceeded 25%, and it is steadily moving towards the 2030 goal.
"Next month, our second bio-based dope dyeing production line will be put into operation," said Factory Director Huang, looking at the sunset outside the workshop with eyes full of expectation. And on Li Xiong's schedule, the next stop is Southeast Asia—where 20% of the new global demand for acrylic blended products is generated. In the wave of greenization, functionalization, and high-endization of the textile industry, this enterprise from Zhangjiagang is continuing to write the growth story of Chinese textile enterprises, with 32 years of accumulation as the sail and technological innovation as the oar.