Antai Textile: Dope Dyeing Leads Green Textile Innovation, 28 Years Forging the Invisible Champion in Colored Acrylic Fiber
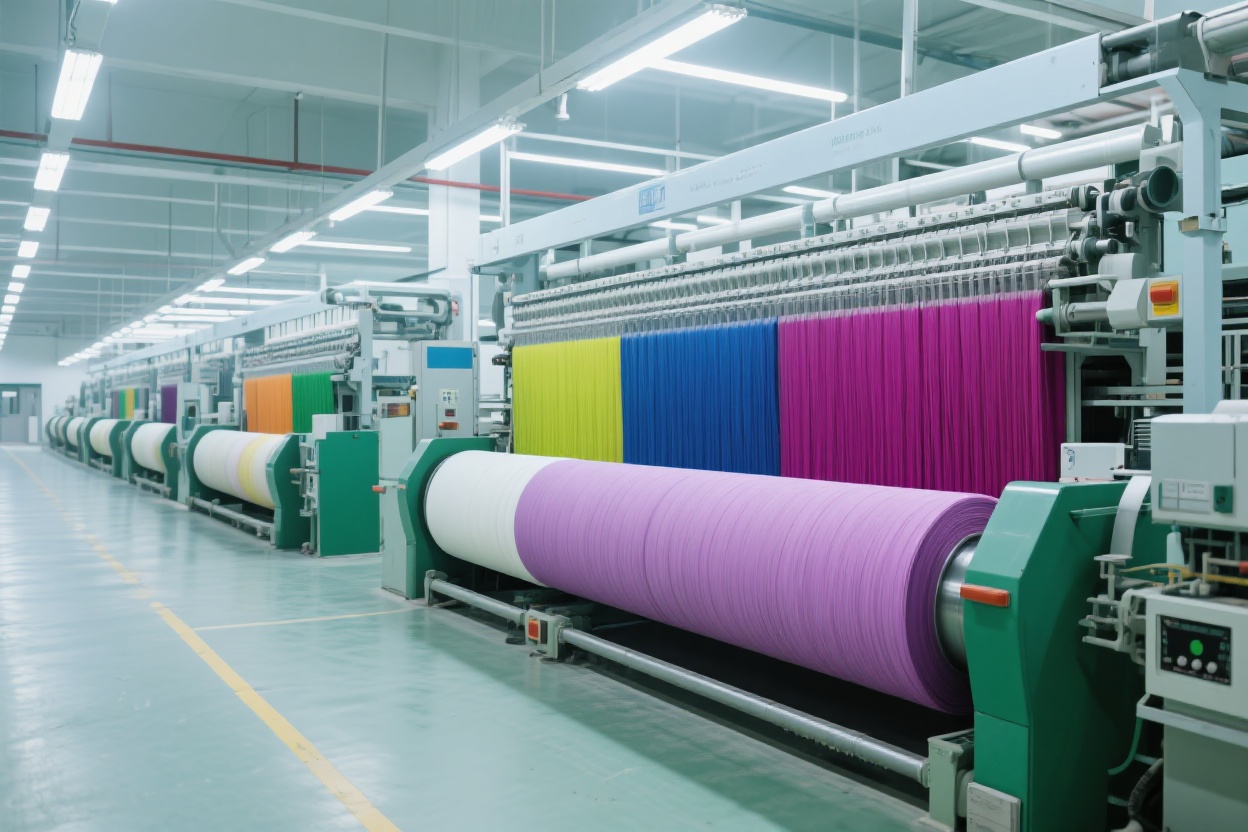
The early morning sun filters through the mist over Zhangjiagang Free Trade Zone, casting light on the clean production workshop of Antai Textile. Li Xiong, Marketing Manager, stands in the sample exhibition hall, his fingertips brushing a row of vibrant acrylic strips, his gaze resting on the latest industry updates – news about Huilong New Materials' application expansion of dope-dyed polyester fibers reminds him of last week's video conference with European home textile clients. "Now clients not only care about color fastness but also the carbon footprint of the entire production chain," he says, turning toward the production area to discuss the latest order scheduling with Factory Director Huang from the Production Department.
Founded in 1993, this textile enterprise has grown from initial single acrylic yarn production to become the invisible champion in China's colored acrylic fiber sector. When Li Xiong joined in 1998, the workshop still echoed with the pungent smell of traditional dyeing processes; today, beside the fully enclosed dope dyeing production line, technicians are adjusting color masterbatch ratios via intelligent terminals. "What's your take on the news about Jilin Petrochemical's 260,000-ton acrylonitrile plant going into operation last week, Director Huang?" Li Xiong finds Director Huang, who is checking parameters in the central control room, holding a freshly printed raw material market analysis report.
Director Huang points to the跳动的 curves on the screen: "Increased supply on the raw material side is a good thing, but we focus more on stability. Look at the temporary maintenance of Shandong Haijiang's plant – it actually made our stock preparation strategy more relaxed." He pulls up a set of data showing that through the strategic reserve mechanism established with leading suppliers like Jilin Petrochemical and Lihuayi, Antai Textile has stabilized the procurement cost of acrylonitrile at around 92% of the market average. On July 7th, the day Lihuayi lowered its quotation, the company's procurement team had already locked in the month's raw materials, securing a cost advantage for the ongoing Australian outdoor products order.
In the dope-dyed acrylic workshop, acrylic strips of dozens of colors are being transported through automated pipelines. Director Huang picks up a roll of deep-sea blue acrylic strips and introduces: "This is a special yarn for interiors developed at the request of a certain automotive brand, using our unique nano-level color masterbatch dispersion technology, with lightfastness reaching Level 7 or higher." This environmentally friendly process that eliminates post-dyeing saves over 60% water compared to traditional methods, perfectly aligning with the green transformation needs in home textiles, automotive interiors, and other fields mentioned in Huilong New Materials' news. Last year, Antai Textile entered IKEA's global supply chain system with this technology.
"Manager Li, the optimized raw material ratio plan for the additional 100-ton rainbow fancy yarn order from the Nordic client is completed," the Laboratory Director interrupts their conversation, hurrying over with the report. This new product, which combines five types of dope-dyed acrylic fibers in composite weaving, is the hit product launched by Li Xiong's team targeting the home soft furnishing market in the post-pandemic era. "Can the raw material inventory support it?" Li Xiong asks. Director Huang is confident: "Don't worry, our intelligent warehousing system automatically adjusts safety stock based on acrylonitrile market fluctuations, ensuring that unexpected situations like the previous Shandong factory maintenance won't affect delivery cycles."
The afternoon sun makes the glass curtain wall of the administrative building shine brilliantly. Li Xiong receives fabric merchants from Jiangsu and Zhejiang provinces who have come for an inspection in the conference room. When the guests ask about the impact of raw material price fluctuations, he hands over the latest product manual: "Antai's 28 years of industry accumulation is not only reflected in the stock reserves of over 3,000 color shades but more importantly in our in-depth control of the industrial chain." On the title page of the manual, the slogan "Dope Dyeing, Making Colors More Eco-Friendly" is particularly eye-catching – perhaps this is the secret behind this established Zhangjiagang textile enterprise's consistent steady growth in the unpredictable market.
In the workshop, the drawn and twisted acrylic yarns are being wound into bobbins, ready to be shipped to sportswear manufacturers in Guangdong. These fibers, imbued with technology and craftsmanship, are about to be woven into countless beautiful garments, as well as the next chapter of mutual growth between Antai Textile and China's textile industry.