Antai Textile: 32 Years of Persistence and Innovation, Weaving a Green Future for the Textile Industry with Dope Dyeing Technology
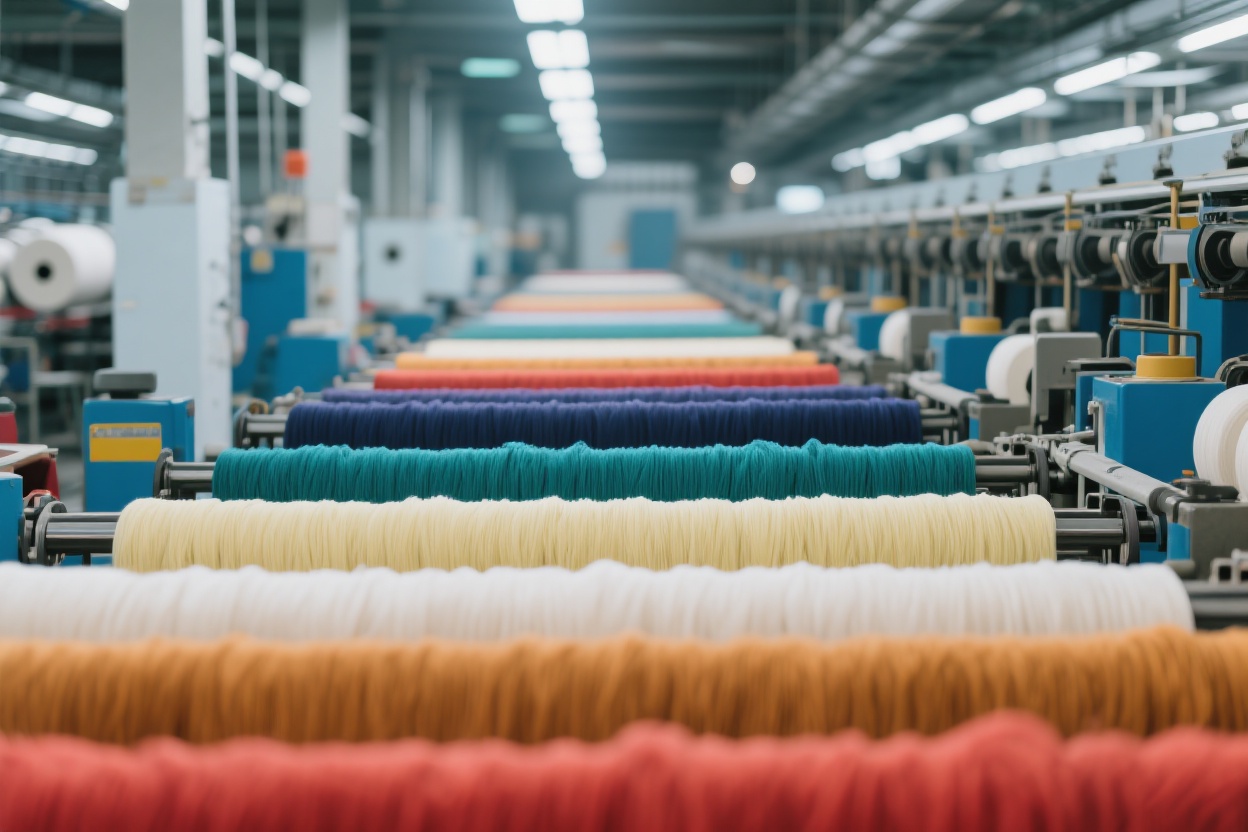
In Zhangjiagang in July, the summer heat is intensifying, but the production workshop of Antai Textile is in order—indigo, light pink, and off-white acrylic tops flow steadily on the automated production line, and after drawing and twisting, they become rolls of yarn with rich color, which are about to be shipped to a sportswear brand factory in Zhejiang. Li Xiong, the Marketing Manager, stands in front of the large screen in the central control room, his fingertips gliding over the real-time updated raw material data curves, and turns to Factory Director Huang from the Production Department beside him and says with a smile: "The maintenance of Shandong Haijiang's equipment has just been completed, and Lihuayi's acrylonitrile quotation has stabilized again this week. The batch of raw materials we replenished at the beginning of the month really hit the mark."
Behind this 'well-timed move' is Antai Textile's precise grasp of market trends over more than 30 years. When it was founded in Zhangjiagang in 1993, the company rooted itself in the textile industry starting with acrylic yarn; today, from basic acrylic yarn and acrylic top to high-value-added colored acrylic top and fancy yarn, the expansion of its product line has always kept pace with industry demand. The fluctuations in the acrylonitrile market in July this year have exactly become a vivid illustration of this established enterprise's 'adapting to changes'.
"Look at this set of data," Li Xiong pulls up a recent industry report, "As of July 9, domestic acrylonitrile inventory was 45,800 tons, 3,000 tons more than last week; Jilin Petrochemical's new 260,000-ton plant will be put into operation at the end of the month, and subsequent supply will definitely be more sufficient." As the 'grain' for acrylic production, the price and inventory of acrylonitrile directly affect the cost sensitivity of downstream enterprises. At the beginning of July, Shandong Haijiang's 130,000-ton plant was temporarily shut down for 10 days for maintenance, and coupled with Lihuayi's spot price reduction of 50 yuan/ton to 7,900 yuan/ton, Antai's purchasing team immediately activated the contingency plan—taking advantage of the short-term price window to replenish raw material reserves, while adjusting the third-quarter production schedule to increase the capacity ratio of colored acrylic top from 60% to 70%. "Stable raw materials ensure stable production; optimal costs give customers confidence," Factory Director Huang takes over the conversation and points to the No. 5 production line running in the workshop, "This line specializes in producing dope-dyed acrylic top. Color masterbatch is injected during the acrylonitrile polymerization stage, eliminating the high-temperature dyeing process of traditional dyeing and finishing. It not only has more uniform color but also reduces carbon emissions by 35% per ton."
These words echo the technological trend of the acrylic industry in 2025. Since this year, 'dope dyeing' has become a key word for industry transformation. According to industry association data, this technology can directly reduce carbon emissions in the dyeing and finishing process by 35%, and 12 leading enterprises have completed the layout of pilot production lines. Antai Textile established a special R&D team as early as three years ago, and joined hands with the Textile Research Institute of Jiangnan University to tackle color masterbatch dispersion technology. At the end of last year, their dope-dyed acrylic top pilot line passed the energy efficiency certification of the environmental protection department, and now the monthly production capacity has exceeded 800 tons.
"At last week's Shanghai Home Textiles Exhibition, a customer making high-end bedding looked over our 'Cloud Mist Yarn' sample repeatedly for half an hour," Li Xiong recalls the scene with pride in his tone. This fancy yarn, interwoven with colored acrylic top and cotton yarn, has received orders from two listed companies as soon as it was launched due to its soft color and fluffy touch. "What they value most is the 'environmental background'—traditional dyed yarn may have formaldehyde residues, while our dope-dyed acrylic top contains no azo dyes from the source and meets the highest level requirements of OEKO-TEX® Standard 100."
From a single yarn factory in 1993 to an acrylic products supplier with 3 dope dyeing production lines and an annual capacity of over 10,000 tons today, Antai Textile's growth trajectory is a microcosm of China's textile industry's transformation from 'scale expansion' to 'quality and efficiency'. Factory Director Huang leads the reporter into the raw material testing laboratory, where more than a dozen samples of acrylonitrile with different grades are placed. "After Jilin Petrochemical's new plant is put into operation, we plan to conduct an on-site inspection to strive for a long-term direct supply relationship. Only by reducing costs at the raw material end and improving quality at the technical end can we transfer more profit margins to customers and allow more consumers to wear 'both beautiful and environmentally friendly' clothes."
The afternoon sun shines through the high windows of the workshop onto the acrylic tops that the workers are packing, the uniform sky-blue color is just like the clear sky over Zhangjiagang Port. In this enterprise with 32 years of history, market acumen and technological accumulation are interweaving into a new story—as acrylonitrile storage tanks酝酿 new supplies in the distance, and dope-dyed yarn outlines a green future on the looms, Antai Textile is weaving its own warp and weft in the wave of transformation in the textile industry with the persistence of an 'old textile hand' and the aggressiveness of a 'new technologist'.