Antai Textile: 32 Years of Innovation Weave Acrylic Fiber Hidden Champion, Intelligent Production Leads Industry Upgrading
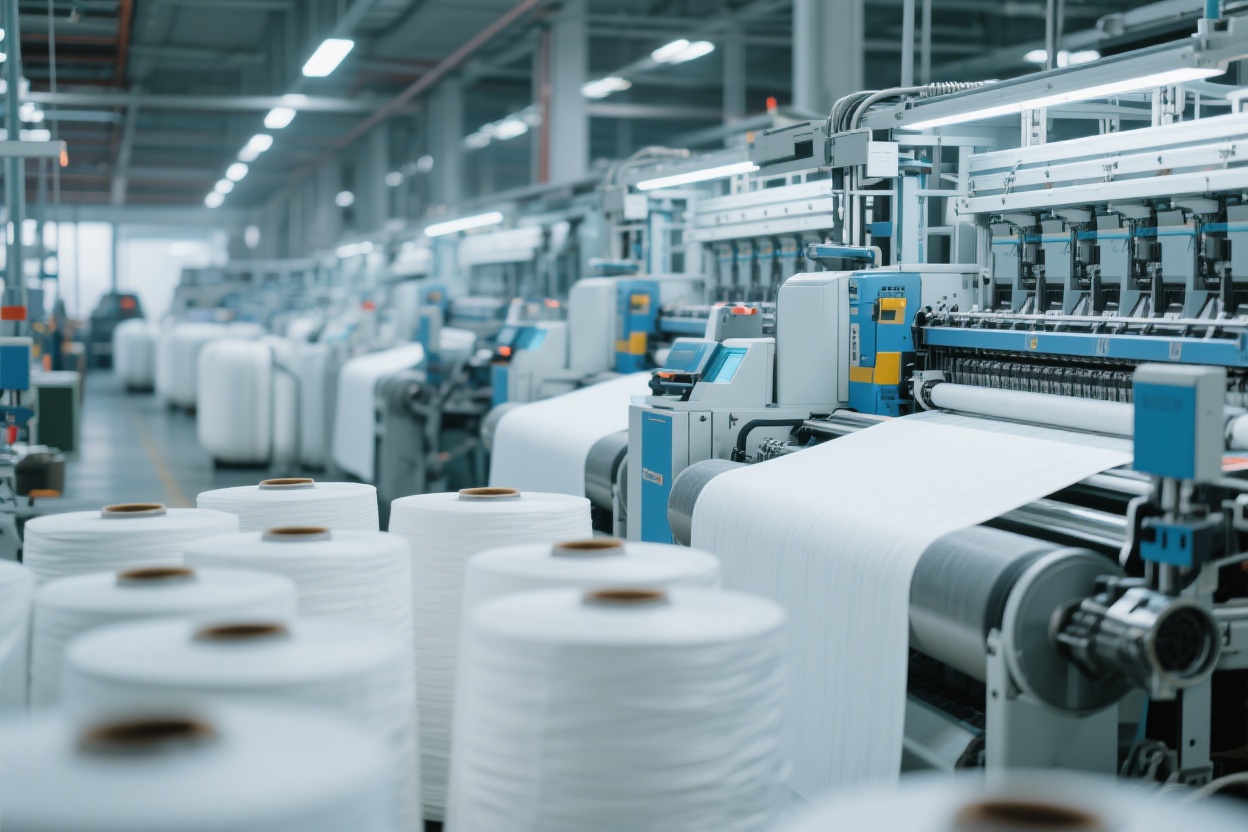
(Main Text)
In July in Zhangjiagang, the wind along the Yangtze River, carrying the late summer humidity and heat, blows into the ventilation ducts of Antai Textile's intelligent production workshop. Factory Director Huang of the Production Department stands in front of the central control screen, his fingertips gliding over real-time data curves—daily average output of acrylic yarn has increased by 8% compared to last month, while energy consumption indicators have decreased by 3.2%. 'Manager Li just sent the market weekly report. Order volume for fancy yarns from clothing brands in East China has increased by 15% year-on-year, especially for our 'Magic Color Acrylic Sliver'; customers are urging us to increase orders,' he turns to the technician beside him with a smile, a hint of imperceptible pride in his voice.
This scene is an ordinary day in Antai Textile's 32-year development history, yet it also reflects how this textile enterprise rooted in Zhangjiagang has always stood at the forefront in the ever-changing market. When it was founded in 1993, Antai was just a small factory focusing on basic acrylic fiber raw materials; today, it has become a hidden champion in the domestic fields of acrylic yarn, colored acrylic sliver, and fancy yarn. Its products cover more than 20 provinces and cities across the country, and are even exported to high-end clothing brands in Southeast Asia and Europe.
In the office of Li Xiong, Marketing Manager, the spread-out industry report is marked with striking data: in the first half of 2025, yarn output of enterprises above designated size increased by 4.9% year-on-year, and chemical fiber output increased by 5.5%, with the consumer market activity exceeding expectations. 'Behind this set of data is the explosion of consumers' demand for 'personalization' and 'functionality' in clothing fabrics,' Li Xiong points to the report and explains to visiting customer representatives. 'For example, our 'Cloud-Soft Acrylic Yarn'—bulked yarn made using 3D crimping technology—is 20% lighter than traditional acrylic fiber while improving warmth retention by 15%. It was just launched this spring and has become a 'bestselling raw material' for sportswear brands' fleece sweatshirts.'
Such market sensitivity stems from Antai's in-depth tracking of industry trends. In early July, when news came that Shandong Haijiang's acrylonitrile plant had a temporary shutdown for maintenance, Factory Director Huang had already been holding a production scheduling meeting for half an hour. 'Acrylonitrile is the main raw material for acrylic fiber. Although Lihuayi's quotation has dropped by 50 yuan/ton, short-term supply fluctuations still need to be addressed in advance,' Factory Director Huang points to the inventory warning in the supply chain system and says. 'We have long-term agreements with Jiangsu Sierbang and Zhejiang Xingxing Chemical, and raw material reserves can support 45 days of full-load production. Coupled with the flexible scheduling of intelligent production lines, customers' delivery times will not be affected.'
In Antai's dyeing workshop, there are no sewage pools commonly seen in traditional textile factories. Instead, there is a closed-loop water circulation system—the production of colored acrylic sliver adopts the dope dyeing process, which directly incorporates pigments into the spinning solution, eliminating the subsequent dyeing process. This not only saves 60% of water but also achieves stable colors with a color fastness of level 4 or above. 'Now downstream brands are promoting 'sustainable fashion'. Our colored acrylic sliver does not require chemical dyeing and can be directly used for spinning and weaving by customers, which is both environmentally friendly and cost-reducing,' Factory Director Huang strokes a roll of sapphire blue acrylic sliver, showing it like a work of art. 'Last week, a designer brand in Shanghai ordered 5 tons of 'Morandi color series' to make autumn and winter haute couture collections.'
Such technical accumulation comes from Antai's dedication to research and development. Over the past 32 years, the company has invested 3% of its annual revenue in technological transformation. The fancy yarn production line imported from Germany can weave more than 20 textures such as 'slub', 'knot', and 'loop'. The 'conductive acrylic yarn' developed last year was also selected into the Ministry of Industry and Information Technology's 'Textile New Materials Demonstration Catalog'. 'Last year, an intelligent wearable enterprise came to us, saying they needed conductive yet soft yarn for health monitoring bracelet straps. We adjusted the formula within three months,' Li Xiong recalls. 'Now that product has exceeded 10 million US dollars in overseas crowdfunding, and our yarn orders are scheduled until the end of the year.'
At the other end of the workshop, on the newly put-into-operation fully automatic packaging line, rolls of acrylic yarn are affixed with QR code labels. 'Scanning the code allows you to see the raw material source, production time, and quality inspection report,' Factory Director Huang takes out his mobile phone to demonstrate. 'Last month, a European customer came for a factory inspection. After seeing our full-process traceability system, they immediately increased the order quantity from 200 tons to 500 tons.'
From manual spinning machines in 1993 to today's intelligent workshops; from a single acrylic sliver to full industrial chain services covering 'raw materials - yarn - pattern design', Antai Textile's 32 years are a microcosm of China's textile industry transformation and upgrading. When the figure '4.9% growth in yarn output' in industry reports turns into flowing yarn in the workshop, and when the trend of 'active consumer market' is transformed into signatures on customer orders, this Zhangjiagang enterprise has woven its own 'weft and warp life' in the细分 track of acrylic textile with focus and innovation.
As dusk deepens, the lights in the workshop are turned on one after another, illuminating the figures of Factory Director Huang and Li Xiong walking side by side towards the office building. 'Next week, we'll go to Guangzhou to participate in the fabric exhibition and take our 'bionic elastic acrylic yarn' there,' Li Xiong says. 'No problem, the samples are ready, and the tensile resilience is 10% higher than the industry standard,' Factory Director Huang replies. In the evening breeze, the faint sound of yarn shuttling on the loom can be heard—that is the prologue to the next chapter of Antai Textile's story written for the textile industry.