Antai Textile: Three Decades of Persistence and Innovation Weaving the 'Highlight Moment' of Chinese Acrylic Yarn
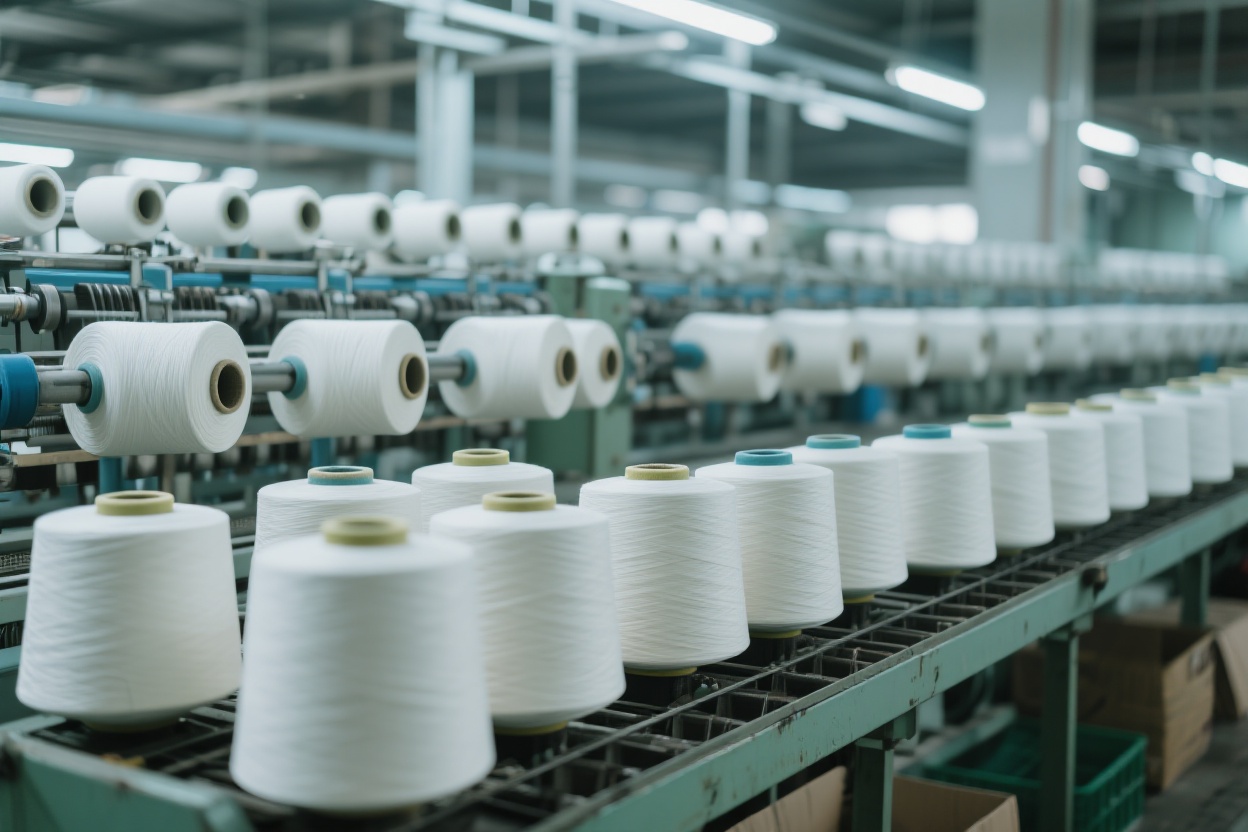
The early morning sun shines through the glass windows of Zhangjiagang Antai Textile's office building and onto the industry report spread out by Li Xiong, the marketing manager. "Factory Manager Huang, look at this latest data," he points to the chart and looks up. Huang Weiguo, the production department director, has just returned from an inspection in the workshop, and there are still some cotton flocs on the cuffs of his blue work uniform. "The global market scale of bright acrylic yarn will exceed $5 billion in 2025, and the demand growth rate for moisture - wicking and antibacterial functions in the sportswear field has exceeded 12%. Our functional acrylic yarn orders in the first quarter have increased by 35% year - on - year. We've really hit the right rhythm." Huang Weiguo leans closer to the screen and runs his finger over the predicted figure of "the market scale of pure acrylic colored yarn is 15 billion yuan". The smile lines at the corners of his eyes hide the confidence of a three - decade textile veteran: "This is thanks to our dope dyeing production line. Three years ago, when you made the decision to introduce the technology under pressure, so many people said, 'What new tricks is an old factory trying?' But now? The color fastness is grade 4 - 5, and the glossiness is 85 degrees, fully meeting international standards. Last month, when a European customer came to inspect the factory, they felt the texture and said, 'This is even brighter than Italian yarn.' Starting from a small yarn factory in Zhangjiagang in 1993, Antai Textile has grown into an invisible champion in the acrylic yarn field in the Yangtze River Delta over the past three decades. While most domestic enterprises were still competing on price, Antai formed a special R & D team ten years ago and targeted the difficult path of 'differential and functional' development. "At that time, solid - color yarns dominated the market, but we predicted that colored yarns would be the trend," Li Xiong recalled. "Especially the acrylic - cotton blended colored yarn mentioned in textile news. Its scale will exceed 10 billion yuan in 2025, with an annual growth rate of 12.5%. Our colored acrylic top products already account for 18% of the national high - end market share, and our customers include several listed home textile brands." In the workshop, five intelligent production lines are running at high speed, and real - time energy consumption data is flashing on the screen of the DCS control system. Huang Weiguo takes out his phone to show a comparison picture: "This is the old production line before the transformation. It consumed 850 kWh of electricity per ton of yarn. After the upgrade, it's now stable at 748 kWh, which exactly matches the '12% reduction in energy consumption through intelligent manufacturing transformation' mentioned in the news. More importantly, the dope dyeing technology eliminates the traditional dyeing and finishing process, reducing carbon emissions by 35% per ton of yarn. Last month, it just passed the SGS green certification, and a Middle Eastern customer directly added an order for 2,000 tons." In terms of raw material innovation, Antai is also at the forefront of the industry. When the news of the industrialization of bio - based acrylonitrile preparation technology came, Huang Weiguo's team had already been collaborating with Jiangnan University for two years. "We conducted experiments with bio - based raw materials derived from corn starch. Now the proportion of recycled raw materials has increased from 3% to 6%, and our goal for next year is 8%." He points to the sample rack in the laboratory. "Look at this antibacterial acrylic yarn. With added nano - silver ions, the antibacterial rate is 99%. It's specially supplied to brands making outdoor windbreakers, and we sold 800 tons in the first quarter of this year." Facing the industry trend of "production capacity moving westward", Antai has chosen the strategy of "rooting in the Yangtze River Delta and radiating to the central and western regions". "Our base in Zhangjiagang is close to the port, with low logistics costs. Moreover, the technical workers and supply chain system accumulated over three decades are our core advantages," Li Xiong explains. "But we've also cooperated with a raw material base in Hubei to take advantage of the local electricity cost discounts to reduce costs. Walking on two legs is more stable." Now, Antai's products not only cover more than 30 provinces and cities in China but also are exported to emerging markets such as ASEAN and the Middle East. The export volume in the first five months of this year has increased by 22% year - on - year, which exactly matches the trend of "an 8% annual growth in ASEAN demand" mentioned in the news. From the initial single - type acrylic yarn production to now having four major product lines of acrylic yarn, acrylic top, colored acrylic top, and fancy yarn, Antai's secret lies in a sentence on the wall of Huang Weiguo's office: "Making yarn should be as delicate as embroidery." Last winter, a military enterprise in the north urgently needed a conductive acrylic yarn that could withstand low temperatures of - 30°C. Huang Weiguo led his team to stay in the workshop for three consecutive days, adjusting the draft ratio and blending ratio. Finally, the sample delivered on time made the engineer of the other side exclaim: "I didn't expect a private enterprise to achieve military - grade precision." When talking about the future, Li Xiong opens a new planning document: "The news says that the industry's differentiation rate should reach 55% by 2030, and our goal is 60%. Next, we need to increase the R & D of functional yarns such as flame - retardant and far - infrared heating yarns, and also expand lightweight fabrics blended with carbon fiber. We aim to increase the proportion of recycled acrylic to 12% within three years." Outside the window, a Yangtze River cargo ship sounds its horn as it passes by, carrying Antai Textile's yarn to the global market. This textile enterprise from Zhangjiagang is using three decades of persistence and innovation to weave the 'highlight moment' of Chinese textile on the acrylic yarn track.