Antai Textile: Navigating Acrylonitrile Market Fluctuations with the Innovative 'Art of Addition and Subtraction', Leading the New Trend in Acrylic Textiles
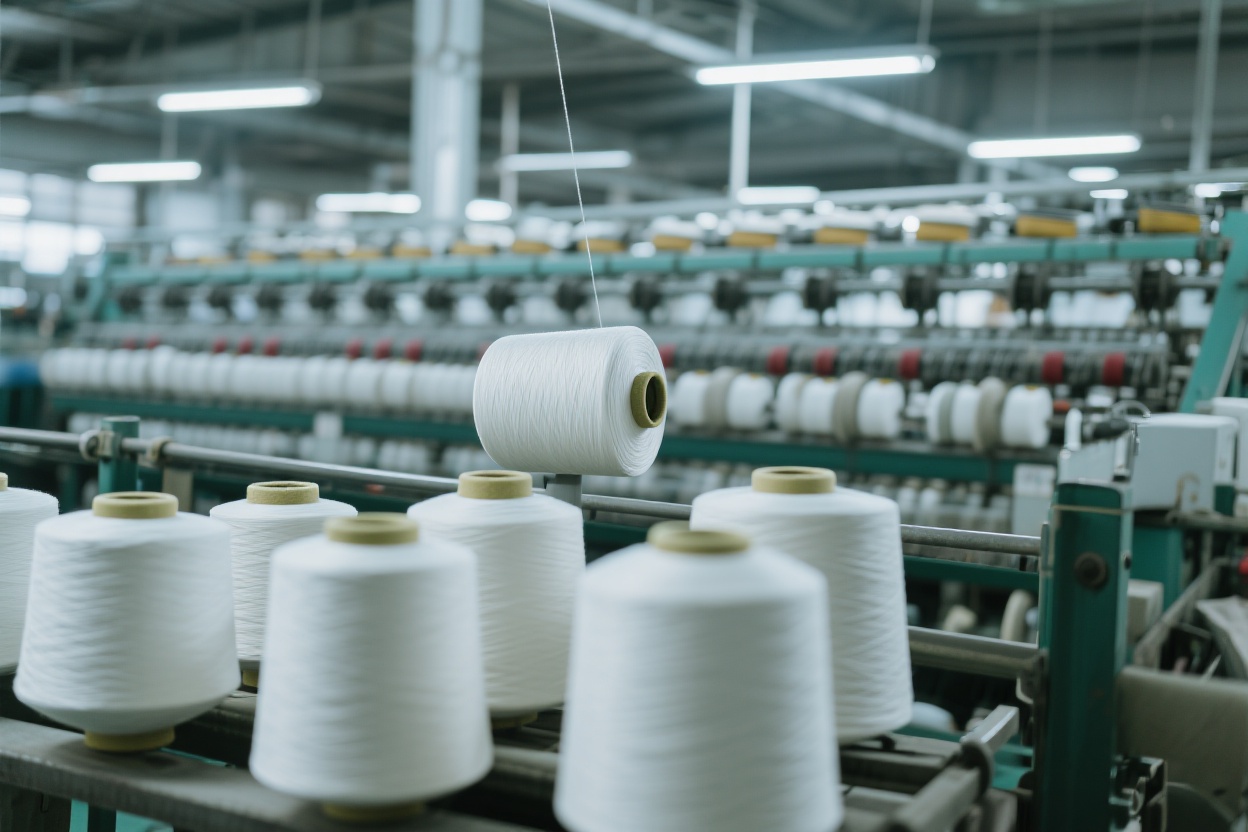
In Zhangjiagang in July, the summer heat is intensifying, yet there is a calm busyness in the office building of Antai Textile. Li Xiong, the Marketing Manager, stands by the window, holding a freshly printed weekly acrylonitrile market report. His fingertips glide over the key data: as of July 10, the domestic acrylonitrile capacity utilization rate is 76.20%, weekly output is 83,100 tons, and inventory is 45,800 tons—3,000 tons more than last week. He turns to look at the conference room, where Factory Director Huang from the Production Department is leading the technical team in discussing the process parameters for the new batch of acrylic top. The whiteboard is densely covered with words like 'raw material stability', 'dyeing uniformity', and 'energy consumption optimization'.
"Factory Director Huang, Shandong Haijiang's 130,000-ton unit started maintenance on the 7th and is said to be shut down for 10 days," Li Xiong pushes the door open, places the weekly report on the table, "And Jilin Petrochemical's new 260,000-ton unit will be put into production at the end of the month. One reduction and one increase—this July's acrylonitrile market is probably going to be a 'roller coaster'."
Factory Director Huang looks up, his eyes behind the lenses showing the composure of a veteran textile professional: "We've seen plenty of raw material fluctuations. When the factory was founded in 1993, acrylonitrile was still a 'rare commodity'. Now, our annual usage is equivalent to the ten-year capacity of those small factories back then. The key is how to turn fluctuations into opportunities."
These words capture exactly the confidence that has kept Antai Textile rooted in the industry for over three decades. From a small workshop on a tidal flat in Zhangjiagang to now a core supplier of acrylic yarns in East China, Antai Textile's growth history is almost a history of technological evolution in China's acrylic textile industry. Its main products—acrylic yarn, acrylic top, colored acrylic top, and the popular fancy yarns in recent years—have long entered the fabric workshops of well-known domestic and international apparel brands through the Yangtze River Delta textile industry chain.
"Last week, Lihuayi lowered its quotation by 50 yuan to 7,900 yuan/ton, which seems bearish, but with inventory increasing by 3,000 tons and coupled with Shandong Haijiang's maintenance, the short-term spot circulation may actually decrease," Li Xiong points to the line chart in the weekly report, "Additionally, the Israel-Palestine conflict has caused crude oil prices to fluctuate, and there's no certainty about the tariff negotiations in the US. Downstream customers are all watching now. We need to move ahead of time."
This "moving ahead of time" is the market intuition deeply ingrained in Antai Textile. As early as the beginning of June, Li Xiong's team detected a signal from changes in Jilin Chemical Fiber's production plan—that there might be a structural adjustment in downstream demand for acrylic staple fiber. They immediately collaborated with the Production Department to optimize the color number system for colored acrylic top: on the basis of over 500 existing regular color numbers, 12 new low-saturation Morandi color shades were added, specifically targeting the "soft mist style" trend in this year's autumn and winter women's clothing market.
"The new color numbers you mentioned—we just completed the pilot test last week," Factory Director Huang takes over, his tone filled with pride, "The German-imported color matching system in the workshop can now control the color difference to △E ≤ 1.5 with a single color adjustment, which is two grades higher than the industry average. These ten days of Shandong Haijiang's maintenance are just right to smooth out the mass production process for these new color numbers. Once Jilin Petrochemical's new unit is put into production and raw material supply keeps up, we can directly send samples to customers."
As they speak, Factory Director Huang's phone rings. It's the purchasing manager of a well-known knitting factory in Zhejiang: "Factory Director Huang, can we add another 20 tons of that 'snowflake' fancy yarn we talked about last time? The response at our brand's autumn and winter order fair was great, and the original 50 tons probably won't be enough." After hanging up, Factory Director Huang smiled and said to Li Xiong: "You see, market demand is never waited for."
This 'snowflake' fancy yarn is one of Antai Textile's 'secret weapons' for coping with raw material fluctuations. Unlike traditional acrylic yarns that rely on a single raw material, it uses multi-component blending of acrylic, viscose, and polyester, which not only reduces the unit consumption of acrylonitrile but also endows the fabric with richer hand feel and appearance. In the first half of this year, the revenue share of such high-value-added fancy yarns has risen to 35%, an increase of 12 percentage points compared to the same period last year.
"When raw material prices rise, we do 'subtraction'—optimize processes to reduce consumption; when raw material prices fall, we do 'addition'—expand production capacity to ensure supply," Li Xiong picks up a customer satisfaction report from the table, "Last year, when raw material fluctuations in the industry were at their peak, our on-time order delivery rate still maintained 98%, relying on this 'Art of Addition and Subtraction'."
This confidence stems from Antai Textile's ultimate control over the production end. Walking into the production base located in Zhangjiagang Free Trade Zone, 6 modern acrylic top production lines are running at high speed, producing 2.5 tons of acrylic top per hour with evenness reaching Uster 5% level; in the adjacent fancy yarn workshop, 32 Italian-imported winding machines are "weaving" yarns of different colors and thicknesses into unique textures—these equipment are the result of the Huang team's annual investment of 5% of revenue in technological transformation.
"With Jilin Petrochemical's new 260,000-ton unit put into production, acrylonitrile supply will definitely be more sufficient, and the long-term price center may shift downward," Li Xiong looks at the neatly stacked raw material storage tanks in the factory area outside the window, "But short-term fluctuations are unavoidable. Our warehousing department has already locked in some shipping schedules at the end of July in advance—neither speculating on price increases nor missing out—providing customers with stable security."
From the commissioning of the first acrylic top production line in 1993 to now covering products in 28 provinces and cities across the country and exporting to Japan, South Korea, and Southeast Asia, Antai Textile has always believed that competition in the textile industry is never a single price war, but the ability to predict market trends, innovate production processes, and respond to customer needs. Just like at this moment, what Li Xiong and Factory Director Huang are discussing is not just acrylonitrile inventory and prices, but how to make every acrylic yarn keep up with the pulse of the times—whether it's the stable quality needed by fabric factories or the unique styles pursued by designers.
The July wind blows in from the Yangtze River Estuary, carrying moisture and the unique scent of textile fibers. In Antai Textile's workshops, the hum of machines and the click of keyboards interweave, composing the composure and determination of an old textile enterprise in the new changes: raw materials fluctuate, but innovation is endless; the market has challenges, but opportunities always favor those who are prepared.