Antai Textile: 32 Years Weaving an Acrylic Innovation Legend, Functional Yarns Leading New Trends in the Global Market
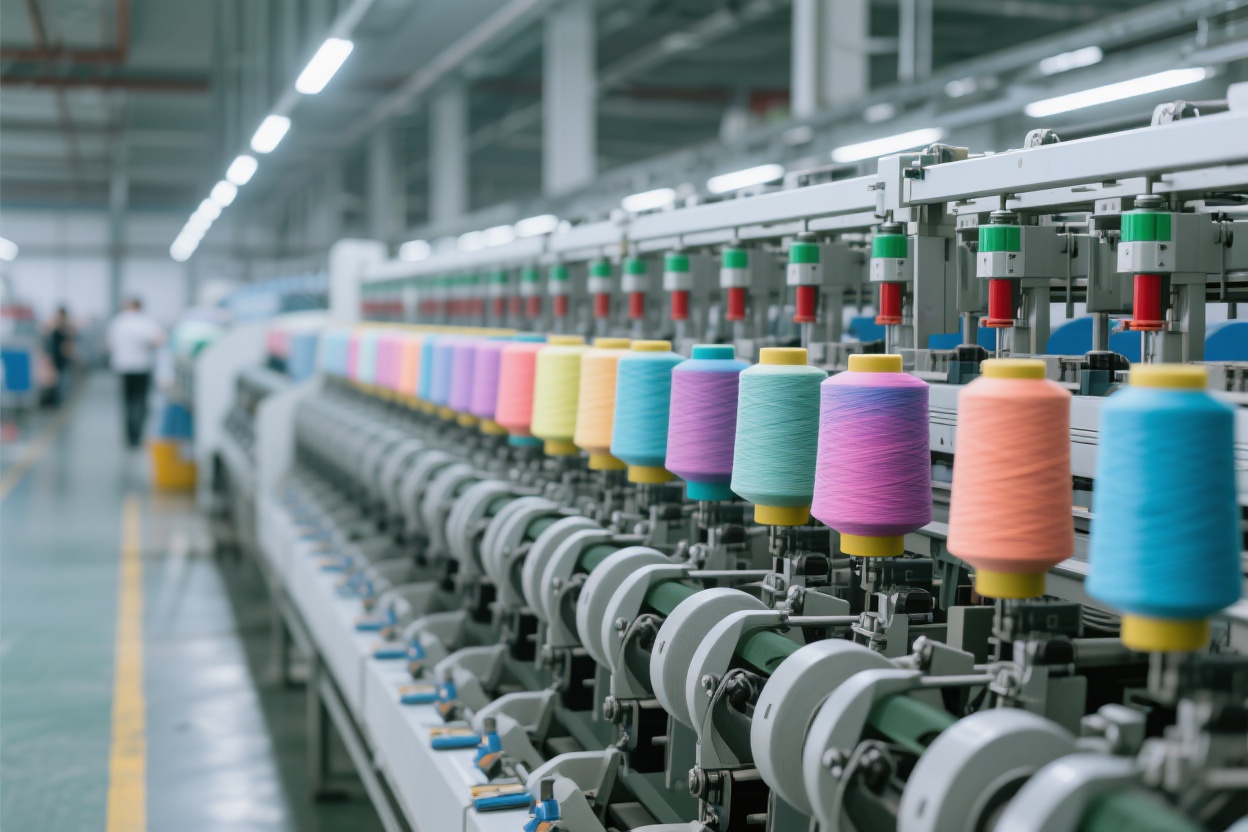
In July in Zhangjiagang, sunlight filters through the high windows of Antai Textile's production workshop, casting dappled light on the neatly arranged spinning equipment. Li Xiong, the Marketing Manager, clutches a freshly released industry report and strides towards the production area – the figures in the report, '2024 China acrylic staple fiber output 6.5 million tons, a year-on-year increase of 12%, with exports accounting for 46%', remind him of the discussion he had with Factory Director Huang from the Production Department three days ago.
"Lao Huang, look at this set of data," Li Xiong spreads the report on Huang's workbench, pointing to the conclusion that 'emerging application fields will become an important direction.' "Functional and intelligent textiles are not just empty words. That batch of antibacterial acrylic sliver in our warehouse – a Zhejiang outdoor brand just ordered 50 tons last week to make mountaineering suit linings. Isn't this the trend?"
Factory Director Huang puts down the quality inspection record sheet in his hand, his fingertips gliding over the跳动的 parameters on the equipment: "That batch of goods you mentioned uses the improved dope dyeing process from last year. The color fastness is 20% higher than traditional dyeing, and it also saves the post-washing process. Customers feedback that using our colored acrylic sliver for fabrics not only results in vibrant colors but also reduces costs by 8%." He pauses, pointing to the new production line at the end of the workshop, "That newly调试好的 fancy yarn twisting machine was acquired to take orders from Guangdong – they want 'slubbed speckled yarn' for the decorative edges of sun-protective clothing, requiring the yarn to have both texture and lightness. We tried three formulations before meeting the standards."
Such scenes are not uncommon in Antai Textile's 32-year development history. Starting from a small workshop in Zhangjiagang in 1993, this enterprise focusing on acrylic yarn has now become an industry veteran with 20 intelligent production lines and an annual production capacity exceeding 30,000 tons. Li Xiong often says: "Acrylic may seem ordinary, but it actually holds great expertise." Just like in the 3 million tons of acrylic staple fiber exported in 2024, Antai's colored acrylic sliver accounts for a significant share – home textile manufacturers in Southeast Asia favor its color stability, while outdoor brands in Europe value the environmental attributes of its recyclable raw materials.
"Last month, a German client came for a factory inspection and stared at our color masterbatch warehouse for half an hour," Li Xiong recalls with a smile. "They couldn't believe we could control the color difference of acrylic sliver within △E ≤ 1.5. Factory Director Huang showed them the full-process digital monitoring from raw material proportioning to spinning temperature. Before leaving, the client said, 'Your quality control is stricter than our local factories.'" Behind this is Antai's continuous investment in the 'Intelligent Manufacturing Upgrade Plan' since 2018: introducing Swiss Rieter spinning equipment, building an MES production management system, and even Factory Director Huang has a real-time monitoring app on his phone. "If there's an abnormality in the production line at midnight, the system alerts me before I notice."
Riding the wave of industry diversification, Antai's products have long gone beyond the scope of traditional clothing fabrics. The flame-retardant acrylic yarn developed for automotive interior manufacturers last year passed the national mandatory standard GB8410-2025; the 'temperature-sensitive color-changing acrylic sliver' launched earlier this year has particularly caught the eye of children's clothing brands – fabrics woven with it display cartoon patterns when cold and revert to solid colors when heated, becoming a hit as soon as they hit the market. "These innovations didn't come out of nowhere," Li Xiong pulls up a market research table on his phone. "We analyzed export data from the past three years and found that the growth rate of functional products is three times that of ordinary products. Director Huang's team spent 8 months tackling the problem to uniformly mix temperature-sensitive microcapsules into the acrylic dope, with experimental waste alone piling up half the workshop."
In the workshop, a new batch of 'dope-dyed acrylic sliver' is passing through the quality inspection station, with red, blue, and green colors flowing like a rainbow. Factory Director Huang picks up a bundle of sapphire blue yarn: "This is 'cool-feeling acrylic' made for a sun-protective clothing brand. Mica powder is added to the fibers, which can reflect ultraviolet rays, making the体感 temperature 3℃ lower than ordinary fabrics. Li Xiong just sent word that orders for this month are already scheduled until the end of the month."
From the first spinning machine in 1993 to today's product matrix exported to over 30 countries, Antai Textile's story is exactly a microcosm of the rise of China's acrylic industry. When the phrase 'international competitiveness' in industry reports transforms into the yarn shuttling through the workshop and the orders praised by customers, Li Xiong and Factory Director Huang know that the answer for the next 30 years lies in the敏锐 capture of trends, in every late night of process improvement, and in the original aspiration of 'making every yarn valuable'. And those future visions of functionality and intelligence are being woven into reality bit by bit by the Antai people under the sunlight of Zhangjiagang.