Antai Textile: Intelligently Creating Differentiated Acrylic Yarns, Weaving a New Chapter in Green and Intelligent Transformation of the Textile Industry
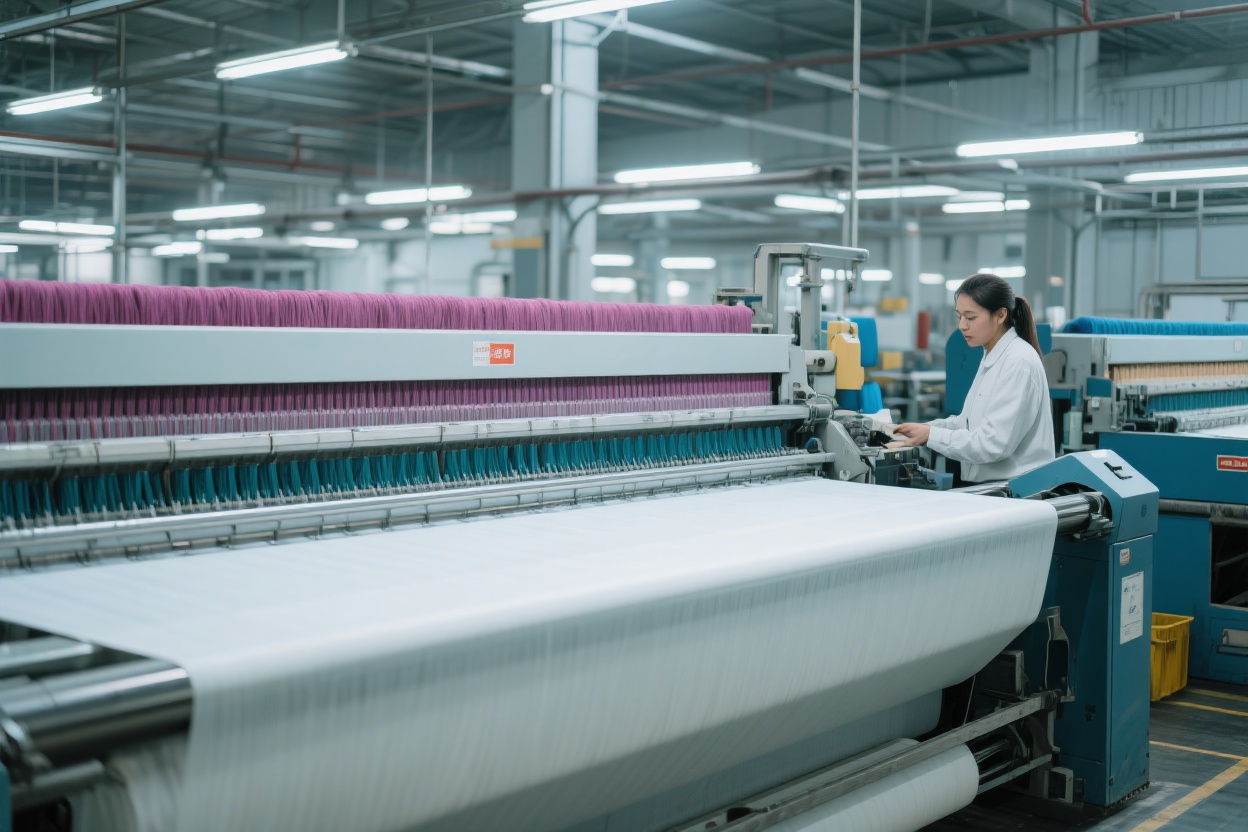
In Zhangjiagang in July, the afternoon sun filters through the glass skylights of Antai Textile's intelligent production workshop, casting tiny light spots on the indigo acrylic sliver. Director Huang of the Production Department is staring at the fluctuating parameters on the screen, tapping lightly on the operation panel – this newly produced batch of "Magic Color Series" colored acrylic sliver has a color fastness 2 grades higher than the industry standard. The order is from a leading knitting enterprise in Zhejiang, which requires delivery of 50 tons within a week. "Manager Li just called and said that downstream garment factories are now afraid of inventory; small-batch, multi-color orders are increasing. Our 'dye-now-spin-now' process has really hit the mark," Director Huang looks up and smiles at the technician beside him.
At this moment, Li Xiong, the Marketing Manager, is organizing data in his office. On the desk lies the latest January-April textile industry report released by the Ministry of Industry and Information Technology: the yarn output of above-scale textile enterprises increased by 7.0% year-on-year, and chemical fiber output increased by 5.7%, but total profits decreased by 5.0% year-on-year. "Output has gone up, but profits haven't kept pace; the problem lies in homogeneous competition and inventory backlog," he underlines the key points in his notebook, which was the core of the repeated discussions with Director Huang in the meeting last week. As an established textile enterprise founded in 1993, Antai Textile's main products – acrylic yarn, acrylic sliver, colored acrylic sliver, and fancy yarn – have exactly stepped on the "rhythm" of the current industry transformation. As an important category of chemical fiber, acrylic can be blended with cotton and wool to enhance fabric functionality, and can achieve "zero sewage dyeing" through dope dyeing technology. Fancy yarn, in particular, is the "secret weapon" for clothing brands to create differentiated designs.
"Director Huang, has the color number of this batch of Magic Color sliver been confirmed? The client said they need to catch the autumn new product launch, and the fabric must have a 'breathable luster',' Li Xiong says as he walks into the workshop, where Director Huang is bending over to inspect a roll of slub fancy yarn. "Don't worry. With the imported German color masterbatch proportioning system, 32 basic colors can create more than 2000 gradient effects. It just passed SGS testing yesterday, and the formaldehyde content is one-fifth of the national standard limit," Director Huang points to the intelligent batching tank next to him. "Do you remember the digital workshop we built three years ago? Now the response time from order to production has been reduced from 72 hours to 24 hours, and the cost of small-batch orders is 15% lower than that of peers. That's why the纺纱 factory that relocated westward in Hubei last month would rather pay extra freight to purchase acrylic sliver from us."
Li Xiong smiles knowingly. Recently, "westward relocation" has become a hot topic in the industry, with super spinning factories in Xinjiang and intelligent factories in Hubei starting operations one after another. However, the continuous rise in Zhengzhou cotton prices and the accumulation of negative feedback from downstream consumption have also troubled many cotton spinning enterprises. "What they lack is not production capacity, but differentiated raw materials," Li Xiong pulls out customer feedback from his phone. "The sweater made by that Zhejiang garment factory using our 'cloud pattern acrylic yarn' sold over 100,000 pieces in three days of online pre-sales, precisely because the inherent three-dimensional texture of the yarn eliminates the need for post-printing processes, reducing costs and being environmentally friendly." This is exactly Antai Textile's strategy to cope with industry changes: when traditional cotton yarn faces inventory pressure, they have developed the "dope dyeing + online twisting" technology for colored acrylic sliver, allowing downstream enterprises to directly obtain semi-finished products with strong spinnability and stable color, saving time and environmental costs in the dyeing process. For fancy yarn, they target the demand of young consumer groups for "personalized fabrics", launching more than 50 new patterns every year. The "dandelion fleece" yarn developed last year was also selected as an annual innovative product in China's textile industry.
In the quality inspection area at the end of the workshop, several workers are observing the cross-section of the yarn under a microscope. "This was inspired by the industry standard seminar on 'Seed Cotton Foreign Fiber Cleaning Machine' that I attended last week," Director Huang hands over a test report. "Although we don't do cotton spinning, the 'three foreign fibers' problem is essentially about impurity control. We applied this idea to acrylic sliver production and introduced an AI visual sorting system. Now the impurity content per ton of product is controlled below 0.3 grams, stricter than the EU standard." From the commissioning of the first acrylic sliver production line in 1993 to now having an annual capacity of 300,000 spindles and products covering 28 provinces and cities across the country, Antai Textile's secret lies in these details – when the industry pursues scale, they deepen segmented categories; when the market faces inventory pressure, they use technological innovation to help customers "go light".
In the evening, Li Xiong receives a message from the logistics department: the 20 tons of "starry sky blue" colored acrylic sliver to be sent to Guangdong that day has been loaded. Outside the car window, the lights of Antai Textile's factory area gradually come on, and the hum of machines in the workshop and the discussion in the quality inspection room interweave into a rhythm familiar to textile people. In this summer where yarn output continues to grow but profits are under pressure, this enterprise rooted in Zhangjiagang for 32 years is weaving the story of the traditional textile industry's transformation towards "differentiation, greenization, and intelligence" with rolls of warm acrylic yarn.