Antai Textile: A 32-Year Textile Veteran Breaks Through with Innovative Technologies; Acrylic Yarn Orders Up 20% Weekly Attracts Market Attention
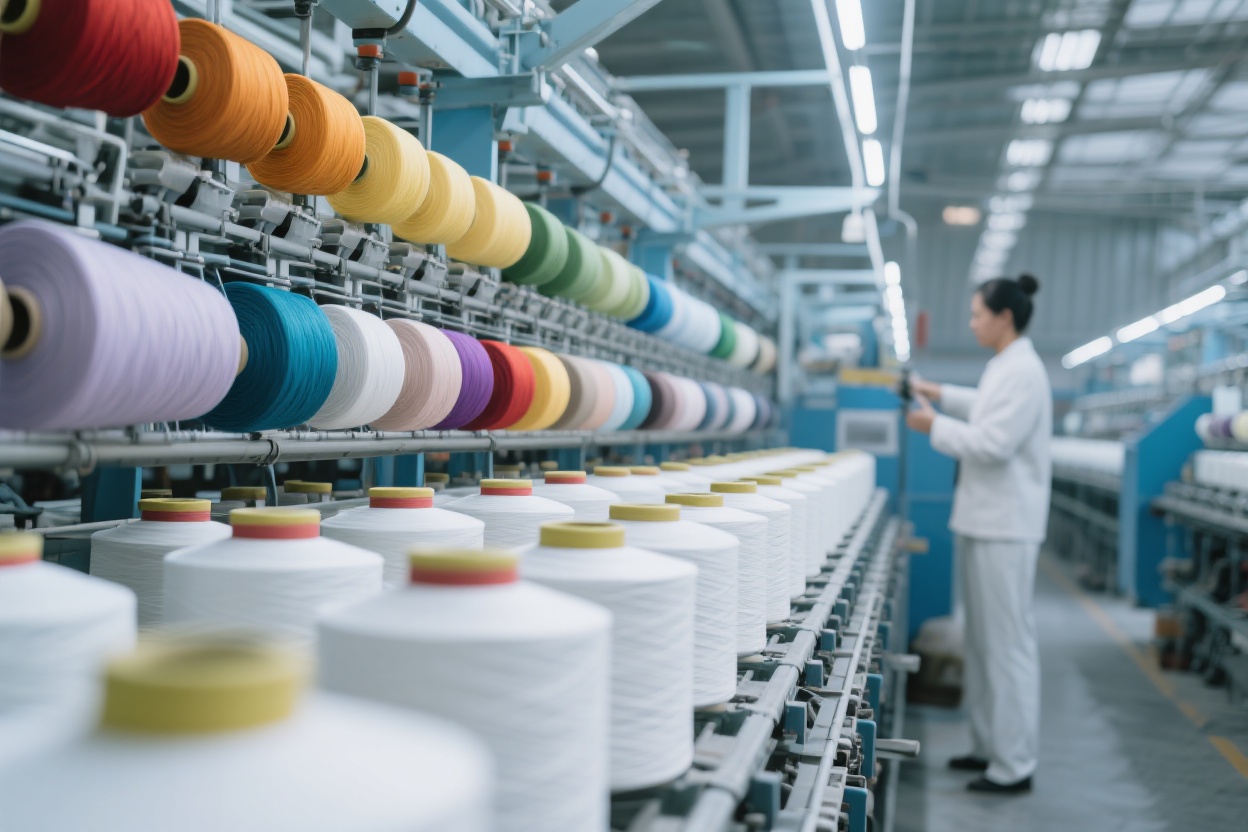
In Zhangjiagang in July, the summer heat is intensifying, but the production workshop of Antai Textile is even hotter than outside the window—rolls of brightly colored acrylic sliver are being uniformly output from the automated production line, soon to be shipped to garment enterprises in Zhejiang. Li Xiong, the Marketing Manager, walked into the Production Department holding the freshly printed industry weekly report and happened to catch Factory Director Huang staring intently at the fluctuating energy consumption data on the central control screen. "Director Huang, the latest cotton sales data is out. The national sales rate is 94.4%, up nearly 9 percentage points year-on-year!" Li Xiong waved the report in his hand. "With the recovery of the end market, our acrylic yarn orders have increased by another 20% this week."
Factory Director Huang turned around and pointed to the curve on the screen: "Exactly. Look at this energy consumption indicator. Since we optimized the pre-dyeing treatment process last month, the unit energy consumption of colored acrylic sliver has dropped by another 3%. It just meets the new energy consumption standards launched by the Ministry of Industry and Information Technology. Our technological level is not inferior even in the silk industry." The two smiled at each other, and the topic naturally turned to recent market changes. As a 32-year textile veteran rooted in Zhangjiagang, Antai Textile has always been sensitive to the slightest changes in the raw material market—just a few days ago, the imported cotton inventory at the local port hit a new low for the year, with stock of 40,500 tons, a 3.5% decrease from last week. This has made many cotton-dependent enterprises start to re-evaluate raw material costs.
"The booming cotton sales are a good thing, but with imported cotton inventory dropping so fast, downstream enterprises will definitely look for more cost-effective alternatives." Li Xiong turned to another page of the weekly report, which marked the changes in Antai's product structure over the past three months. "Look, the sales volume of our acrylic/cotton blended yarn has increased by 15% month-on-month, especially the 32-count cashmere-like acrylic yarn, which several knitting factories in Guangdong are scrambling to order. Customers say that with the current volatile cotton prices, using our acrylic yarn not only ensures warmth retention but also has more stable colors than cotton yarn, saving a lot of trouble in the dyeing and finishing process."
Behind this is Antai Textile's early layout for product trends. As early as last year, the company upgraded its colored acrylic sliver production line targeting the "color economy". Through dope dyeing technology, it has realized immediate production and delivery of 120 basic colors, eliminating the post-dyeing process of traditional yarn. "Previously, when a customer wanted a special color, it took 15 days from sampling to delivery. Now our intelligent color mixing system can produce samples in 3 days, cutting the production cycle in half." Factory Director Huang led Li Xiong to the intelligent storage area of the workshop, where robotic arms were neatly stacking packages of acrylic sliver labeled "Haze Blue" and "Dogwood Pink". "Last week, a home textile customer from Shandong just added an order for 50 tons of gradient fancy yarn, saying that when used in autumn and winter blankets, the terminal feedback is that it sells better than solid-color models with a 20% premium."
From the production of a single acrylic sliver when it was founded in 1993 to now being a full-category supplier covering acrylic yarn and fancy yarn, Antai Textile's growth trajectory is exactly a microcosm of the transformation and upgrading of China's textile industry. In Zhangjiagang, a textile industry cluster, the company has not only witnessed the transformation of the local port from scattered storage to a 100-million-ton port but also built a moat through continuous technological investment—investing 5% of its annual revenue in research and development. Its independently developed low-melting-point acrylic sliver has broken the dependence on imports, and last year it also took the lead in formulating the industry's "Testing Specification for Color Stability of Fancy Yarn".
"Yesterday, the textile and apparel sector rose another 0.81%. Although there was capital outflow, the rise of companies like Yunzhongma and Bailong Oriental indicates that the market's attention to differentiated yarn is increasing." Li Xiong closed the report and looked at the neatly stacked containers outside the workshop. "This afternoon, customers from Ningbo will come to inspect our antibacterial acrylic production line. This is a new product developed this year—yarn added with nano-silver ions, which can maintain an antibacterial rate of over 90% after 50 washes, just meeting the functional needs of sportswear."
Factory Director Huang nodded, his gaze returning to the central control screen: "The production line has been debugged, and indicators such as energy consumption and color fastness all meet the standards. Go ahead and negotiate with confidence. Our 32-year-old factory relies on these nine words: 'stable raw materials, exquisite craftsmanship, and quick response'."
As they spoke, the workshop's radio sounded a new order prompt, and another batch of fancy yarn was about to be put into production. Outside the window, the cranes at Zhangjiagang Port were busy loading and unloading goods, and the textile story of this city is being woven into a broader market along with Antai Textile's yarn.