Antai Textile's 32-Year Acrylic Innovation Journey: Smart Transformation and Digitalization Drive Export Upward Trend, Technology Weaves New Momentum for the Textile Industry
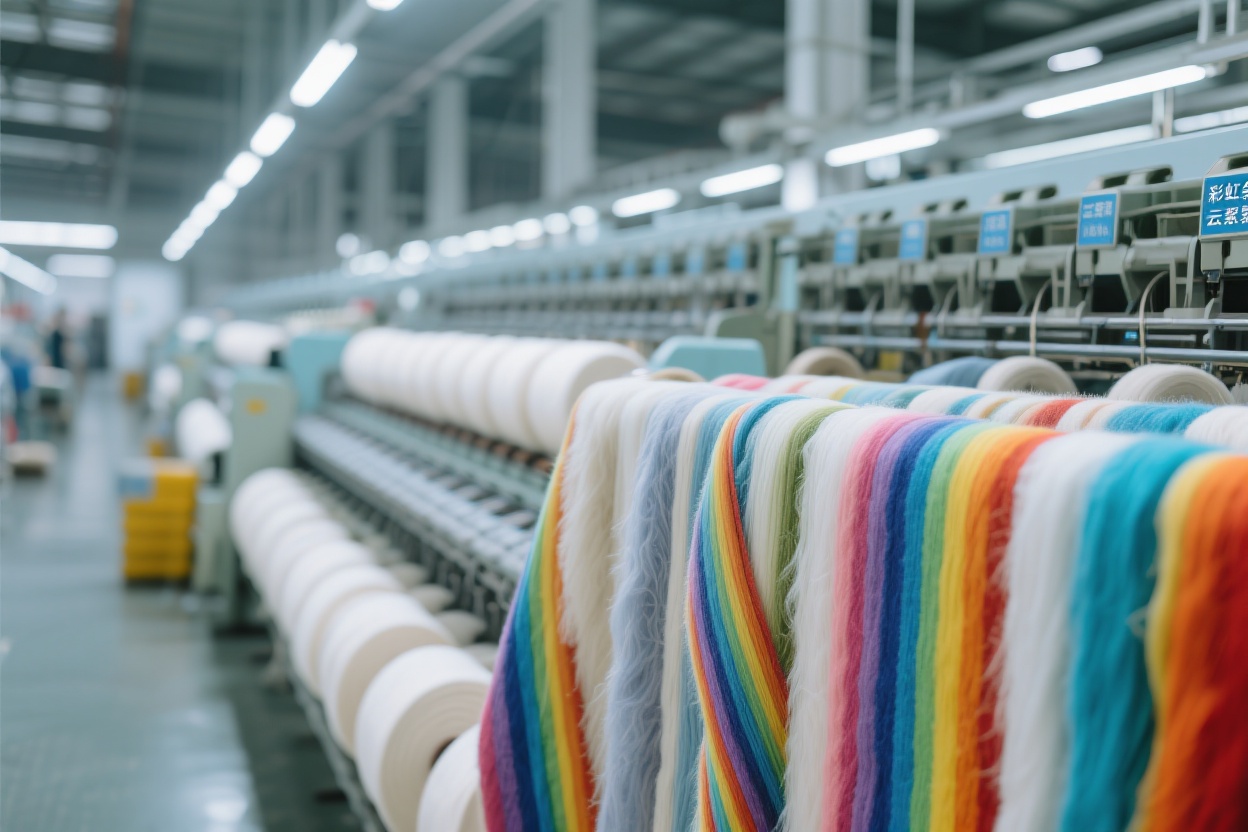
In July in Zhangjiagang, the wind along the Yangtze River, carrying the late-summer humidity and heat, sweeps through Antai Textile's intelligent production workshop. Li Xiong, the Marketing Manager, stands in front of the large screen in the central control room, his fingertips gliding over a set of dynamic data – total textile exports in May increased by 12.3% year-on-year, hitting a five-year high for the same period. 'We have to catch this export warm current,' he turns to Factory Director Huang from the Production Department beside him, as the screen is displaying the real-time progress of a 200-ton colored acrylic sliver order just placed by a Southeast Asian customer.
As a textile 'veteran' rooted in Zhangjiagang for 32 years, Antai Textile has focused on deep cultivation in the acrylic field since its establishment in 1993. From initial single acrylic sliver production to today's full-category matrix covering acrylic yarn, colored acrylic sliver, and fancy yarn, the growth trajectory of this enterprise is just like a microcosm of the transformation of China's chemical fiber textile industry. Li Xiong remembers that ten years ago, overseas customers were still troubled by 'poor color stability of Chinese acrylic', but now the company's 'Rainbow Stripes' series of colored acrylic sliver has passed OEKO-TEX® certification and become the designated raw material for Italian knitting brands.
'Look at this set of data,' Li Xiong pulls up another report. Although the National Cotton Price B Index rose slightly by 0.6% this week, the international Cotton M Index fell by 0.4%. 'When cotton prices fluctuate, the advantages of our acrylic products become prominent,' he explains. Acrylic fiber not only has warmth retention comparable to wool but also costs only 60% of cotton fiber, making it particularly suitable for the small-order and quick-response needs of fast fashion brands. In the first half of this year, the company's 'Cloud Fluff' series of acrylic yarn developed for the export market, which uses a low-melting-point composite process and is 15% lighter than traditional products, has accumulated orders of over 800 tons from South Korea and Australia.
Upon hearing this, Factory Director Huang points to the intelligent color matching system operating in the workshop: 'This is our confidence.' The 'smart transformation and digitalization' project completed last year has reduced the color change time of colored acrylic sliver from 4 hours to 45 minutes, with color number precision controlled at ΔE ≤ 1.5, an industry-leading level. In the fancy yarn workshop, 12 imported German hollow spindle spinning machines are weaving 'slub + segment color' composite fancy yarn. This high-end product, once dependent on imports, now has a monthly production capacity of 300 tons at Antai Textile, supplying domestic leading home textile brands.
'Do you remember that European customer in 2018?' Factory Director Huang recalls with a smile. At that time, the customer came with a test report showing 'excessive pilling rate of acrylic sliver'. The production team spent three months adjusting the drafting multiple and oil agent ratio, finally increasing the pilling grade from level 3 to level 4-5. Now, this customer's annual purchase volume has grown from the initial 50 tons to 500 tons. 'Last week, they also sent an email saying that the children's sweaters made with our fancy yarn sold out in German supermarkets.'
On the order board in the central control room, an outdoor product enterprise from Zhejiang has just added 100 tons of anti-ultraviolet acrylic yarn. Li Xiong says this is a new functional product developed by the company this year. By implanting nano-level sunscreen particles during the spinning stage, its UPF value can reach 50+. 'Now the outdoor sports market is booming, and the gross profit of this high value-added yarn can be 15% higher than that of conventional products.'
From a small workshop by the Yangtze River to a modern textile enterprise with an annual production capacity of over 20,000 tons, Antai Textile's story holds the resilience code of China's textile industry. As the industry accelerates iteration in the wave of 'smart transformation and digitalization', and as the export market seeks a new balance amid global changes, this enterprise with 32 years of accumulation is weaving new momentum for traditional industries through the innovation of every acrylic fiber. Factory Director Huang looks at the national flag fluttering outside the workshop: 'At next month's Shanghai Textile Expo, our "Eco Color Stripes" series will make its debut, which features truly waterless dyeing technology.' In the sunlight, the wrinkles at the corners of his eyes hold the textile people's dedication to quality and, even more, their expectations for the future.