Capture 60% of the market share! Antai Textile Weaves a Global Sustainable Fashion Landscape with High - end Acrylic Yarn
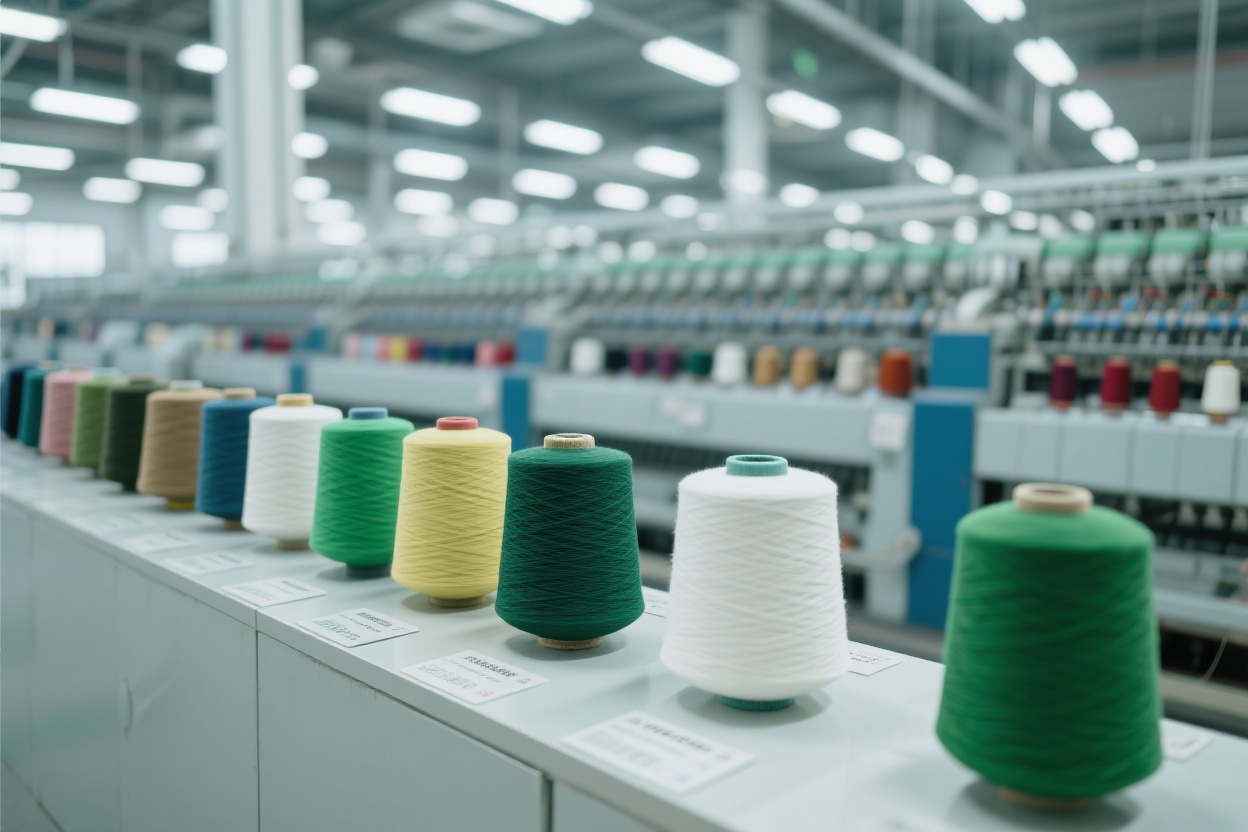
At seven o'clock in the morning, in the production base of Antai Textile in Zhangjiagang Free Trade Zone, Factory Manager Huang of the production department is already standing in front of the intelligent central control screen in Workshop 3. The jumping data stream on the screen shows that a batch of 1.2D ultra - fine denier colored acrylic tops that just came off the production line last night have a color fastness index three grades higher than the industry standard. 'This batch of goods is an urgent order for that new energy vehicle interior supplier in Shanghai. What they want is the feature of 'zero formaldehyde + high wear - resistance'.' Factory Manager Huang pointed to the environmental protection test report on the screen, with a hint of pride in his tone. Such scenes have become the norm in Antai Textile in the past three years. On the desk of Li Xiong, the marketing manager, lies the latest '2025 China Acrylic - Cotton Colored Yarn Market Research Report', in which the conclusion that 'automotive interiors and household textiles contribute more than 60% of the market share' is circled in red. 'In 2023, the proportion of orders for automotive interior yarn in our acrylic yarn orders was only 15%, but it has soared to 30% in the first quarter of this year.' Li Xiong flipped through the customer ledger. 'The demand of downstream brands for high - performance yarn is very obvious - they need high color saturation, to meet international environmental protection standards such as OEKO - TEX®, and to keep up with the small - batch and multi - batch customization rhythm of automobile manufacturers.' As a textile enterprise that has been rooted in Zhangjiagang since 1993, Antai Textile's product matrix - acrylic yarn, acrylic tops, colored acrylic tops and fancy yarns - happens to hit the rhythm of the industry's structural adjustment. Li Xiong remembers that in the early stage of the industry's recovery in 2022, the team keenly noticed two changes: first, the customs data showed that the domestic acrylic import volume decreased from 147,400 tons in 2017 to 51,000 tons in 2023, opening up space for domestic substitution; second, there was an inventory backlog of conventional acrylic varieties, but customers frequently mentioned high - end terms such as 'composite fiber' and 'irregular cross - section' when inquiring. 'At that time, we decided to shift the R & D focus from ordinary acrylic tops to differentiated products.' This decision was quickly translated into a transformation plan for the production line. Factory Manager Huang led the technical team to spend eight months introducing German - imported color - spinning integrated equipment on the basis of the original equipment, moving the dyeing process forward to the fiber stage. This not only reduced sewage discharge by 30%, but also increased the color fastness of colored acrylic tops to above grade 4. 'Previously, if a customer wanted 1000 meters of yarn in 5 colors, it would take at least three days for production. Now, with the automated color - mixing system, batches can be switched in two hours.' Factory Manager Huang pointed to the intelligent yarn - doffing machine running in the workshop. 'Last year, the proportion of our high - end products has increased to 28%, and the goal for this year is 35%, which just coincides with the industry's forecast rhythm.' With the advantage of 56% of the acrylic production capacity in East China, Antai Textile's 'differentiation + greening' strategy is reaping market rewards. At the beginning of this year, the 'antibacterial acrylic fancy yarn' developed by them for a leading home textile brand in Zhejiang, with its moisture - absorbing and quick - drying properties and special AB yarn texture, had a single - month order volume exceeding 500 tons. 'The gross profit of such products is 15% - 20% higher than that of conventional yarns,' Li Xiong revealed. 'More importantly, it has opened up cross - border e - commerce channels. Now, the small - batch customization orders from North America through Amazon are growing at an average monthly rate of over 12%.' Standing at the 30 - year development node, in Antai Textile's workshop, the old equipment from the establishment of the factory in 1993 is still running after intelligent transformation, and there is also an environmentally friendly dye production line that was put into operation in 2024. Factory Manager Huang said that the team is currently working on the 'bio - based acrylic' technology, aiming to make the proportion of renewable components in the raw materials reach more than 50%. 'The report says that the global acrylic colored yarn market scale will reach 22 billion US dollars by 2030, with China accounting for more than 40%.', Li Xiong looked at the neatly stacked export containers outside the window. 'We textile workers of this generation aim to weave the 'Made in China' yarn into the global sustainable fashion landscape.'