The Stabilizing Force Amid Market Turbulence: Antai Textile's 32 Years of Accumulation Turns Fluctuations into a 'Constant' for Development
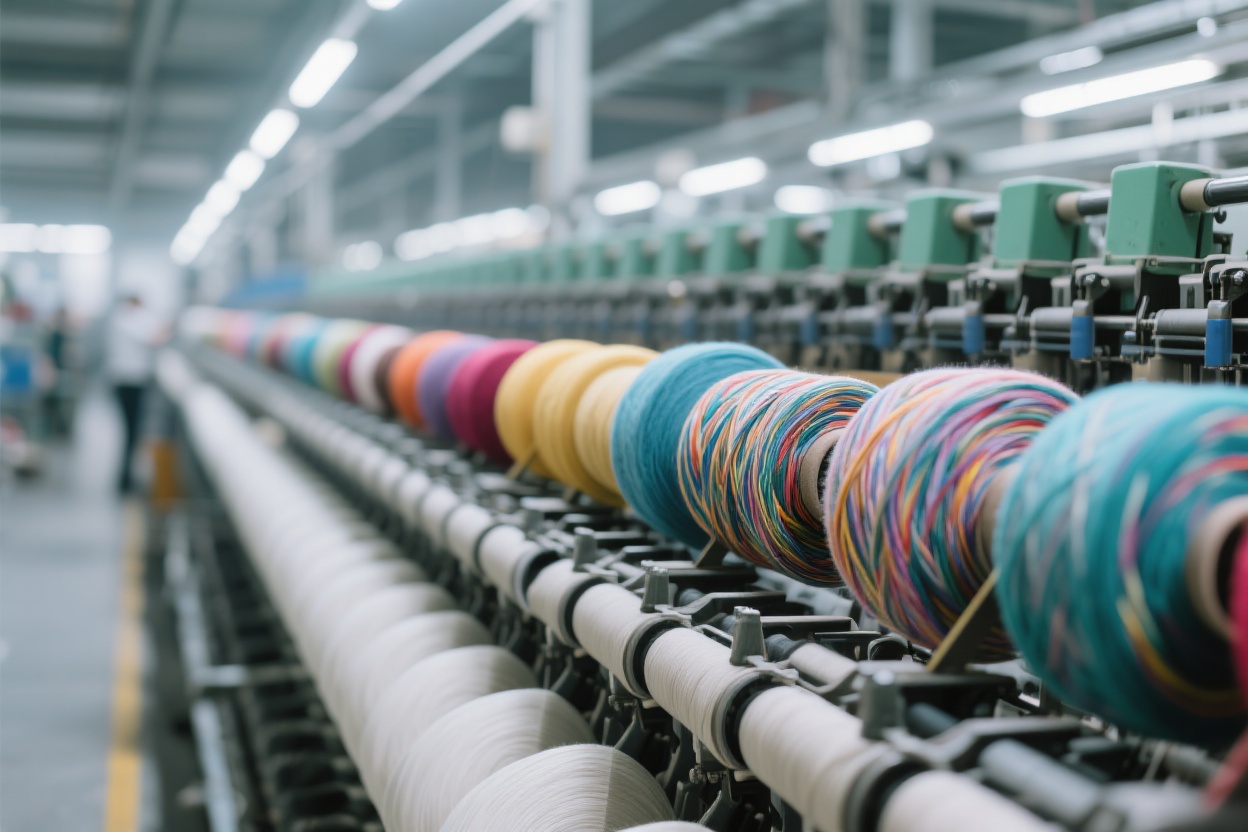
In July in Zhangjiagang, the summer heat is intensifying, yet the 'heat' of the domestic acrylic market carries a tinge of uncertainty. Global economic fluctuations, undercurrents of geopolitics, coupled with volatile crude oil prices, undecided production plans of Jilin Chemical Fiber, and impending U.S. tariff negotiations, have left acrylic prices standing at a crossroads of sharp volatility. 'This is not just a challenge, but a 'touchstone' for the accumulation we've built over 32 years of deepening our roots in the industry,' said Li Xiong, Marketing Manager of Antai Textile, standing by the window of his office, gazing at the tower cranes in the nearby workshop with a steady tone. Founded in 1993 on the banks of the Yangtze River, this textile enterprise is leveraging over three decades of industry accumulation to seek certain answers amid changes.
The Astute Observer of the Market 'Barometer': Capturing Demand Signals Amid Price Fluctuations
'Last week, the capacity utilization rate of the acrylonitrile industry was just 76.20%, Shandong Haijiang has shut down for maintenance for 10 days, and Lihuayi has lowered its quotation by 50 yuan/ton... These seemingly scattered data are actually the 'code' to changes in customer demand,' Li Xiong explained, with densely packed market analysis sheets spread across his desk, where 'risk points' marked in red are already paired with 'strategies' in blue. He noted that during periods of price volatility, customers are most anxious about 'uncontrollable costs' and 'unstable supply chains,' and Antai's response precisely targets these two pain points.
'Take our colored acrylic tops, for example. Using dope dyeing technology, we lock in color stability from the source. Downstream customers can directly spin yarn upon receiving the tops, eliminating 30% of water usage and 20% of energy consumption compared to traditional dyeing processes, reducing costs by over 800 yuan per ton,' Li Xiong said, picking up a roll of indigo acrylic top with evenly flowing threads. 'In the past week, orders from knitting customers in Jiangsu and Zhejiang have increased by 15% year-on-year. They say, 'No matter how prices fluctuate, the costs saved are pure profit.''
In the face of potential tariff negotiations, Antai's fancy yarns have become a 'key to breaking the impasse.' 'Demand for personalized fabrics in European and American markets has been growing. Our developed 'slub acrylic yarn' and 'loop yarn,' used in children's clothing and homewear, can increase product premiums by 20%-30%,' Li Xiong said, pulling up customer feedback emails. 'We just finalized autumn orders with a German brand last week. They're willing to wait two weeks to use our fancy yarns because 'ordinary yarns have too thin profit margins under tariff pressures, and differentiation is the way to survive.''
The Steadfast Guardian of Production 'Ballast': Fortifying Quality Foundations Amid Raw Material Fluctuations
The implementation of market strategies离不开 solid support from production. In Antai Textile's production workshop, machines hum in an orderly manner. Factory Director Huang is monitoring various parameters on the central control screen—89.3% acrylonitrile conversion rate and 3.2cN/dtex fiber breaking strength. Behind these numbers lies the 'confidence' to cope with raw material fluctuations.
'Jilin Petrochemical's 260,000-ton acrylonitrile plant will start production at the end of the month, which will ease the long-term tight supply of raw materials, but the short-term maintenance of Shandong Haijiang has created a local shortage. We need to 'stock up in advance' while 'feeding materials precisely,'' Director Huang said, pointing to the intelligent management system in the raw material warehouse. 'The procurement team just signed 'flexible procurement agreements' with three leading suppliers last week, locking in supply volumes while allowing prices to fluctuate with the market, ensuring raw material inventory remains above the safety line for the next three months.'
More crucially, there's meticulous attention to processes. 'Every 100 yuan/ton fluctuation in acrylonitrile prices affects the cost of acrylic yarn. We completed the transformation of the 'low-temperature polymerization process' last month, reducing acrylonitrile consumption from 0.85 tons/ton to 0.82 tons/ton. At the current price of 7,900 yuan/ton, this saves nearly 300,000 yuan in costs per month,' Director Huang smiled, noting that the 20 production lines in the workshop produce 120 tons of acrylic yarn and 80 tons of acrylic tops daily. 'While others worry about 'expensive raw materials,' we use technology to turn 'expensive' into 'controllable.'"
The commitment to quality lies in the details. In the quality inspection room, technicians are observing the cross-section of acrylic tops under an electron microscope. 'We control the evenness CV value within 1.8%, 0.5 percentage points lower than the industry average, which reduces the yarn breakage rate by 40% for downstream customers,' Director Huang said. Since the first production line was put into operation in 1993, Antai has inscribed 'Never send problematic yarn out of the factory' on the wall. Now, 32 years later, this phrase has become 'muscle memory' for over 300 production employees.
Over Three Decades of Industry Companion: Standing Firm with 'Stability', Forging Ahead with 'Innovation'
From building a factory on a stretch of tidal flat in Zhangjiagang in 1993 to becoming a core supplier of acrylic yarns in East China today, Antai Textile's growth is itself a 'brief history of resilience' in China's textile industry. 'We weathered the plummeting orders during the 2008 financial crisis and the supply chain disruptions during the 2020 pandemic, relying on 'not following trends, not speculating, and thoroughly mastering acrylic,'' Li Xiong sighed.
Today, Antai's products have expanded from a single acrylic yarn to over 20 categories including colored acrylic tops and fancy yarns, serving over 200 domestic and foreign clothing brands—from fast fashion giants to high-end custom workshops, all can find tailored 'Antai solutions.' 'Last year, we invested 20 million yuan to build a R&D center and collaborated with Jiangnan University to develop environmentally friendly acrylic materials. Now, the R&D of bio-based acrylic yarn has entered the pilot test stage, which will reduce petroleum resource consumption by 60% in the future,' Li Xiong said, his eyes shining. 'Textiles are not a sunset industry. By empowering traditional materials with technology and innovation, we can always walk in the morning sun.'
Sunlight filtered through the clouds outside the window, casting a golden glow on Antai Textile's sign, where the '1993' inscription sparkled. In this uncertain July, this enterprise, rooted in the industry for 32 years, is leveraging keen market insight, meticulous production control, and persistent pursuit of innovation to turn price fluctuation 'variables' into steady development 'constants.' As Director Huang often says: 'No matter how rough the market风浪, holding fast to the anchor of quality and gripping the rudder of innovation will allow us to sail steadily forward with customers.' This is perhaps the insight Antai Textile offers to the industry—true competitiveness is never about how fast you run in good times, but how steady you stand amid changes.