Orders Surge 12%! Antai Textile Cracks the Cycle Code of the Textile Industry with Color + Intelligence
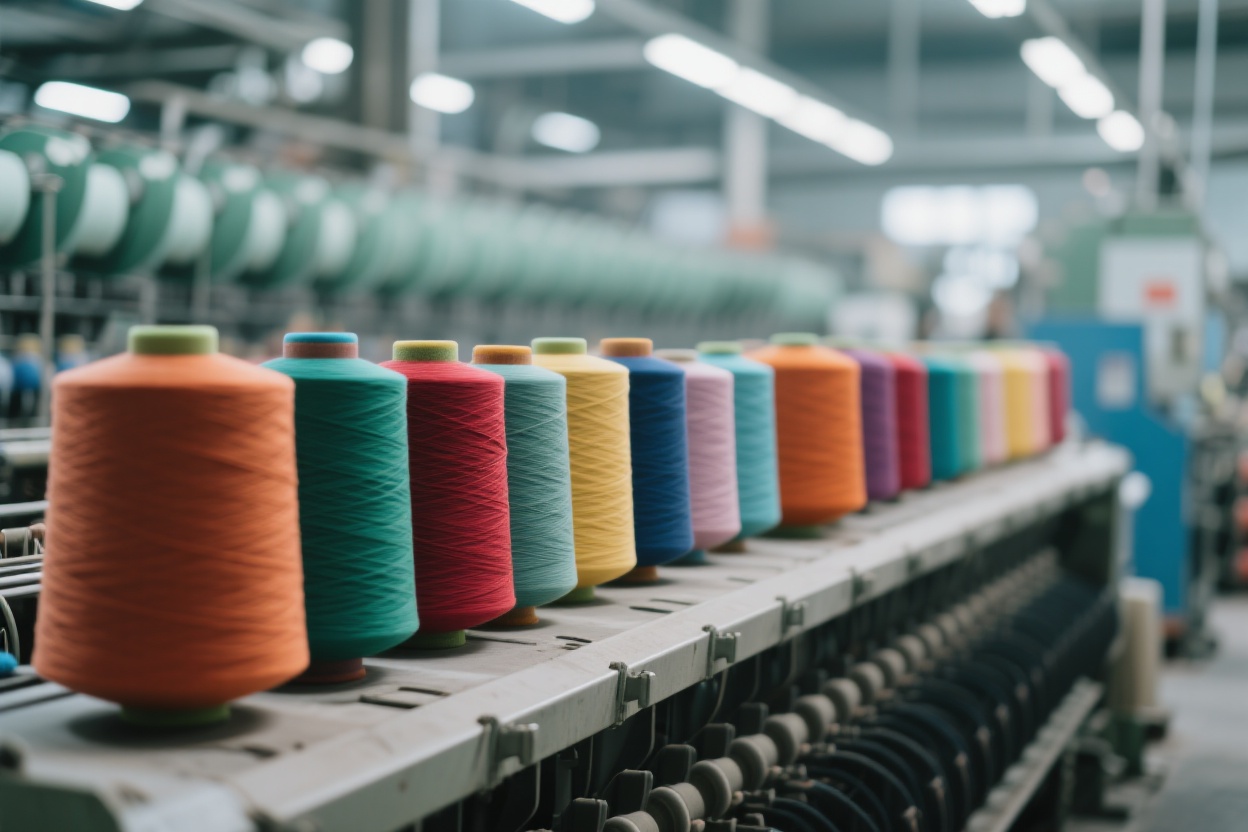
In Zhangjiagang in July, the summer heat is intensifying, but the production workshop of Antai Textile is even hotter than the weather—intelligent production lines are running at high speed, colored acrylic sliver in the dyeing vats is glowing with a uniform luster, and workers in the packaging area are loading newly produced acrylic yarn onto trucks bound for Zhejiang. "In the first five months, the national yarn output increased by 4.9% year-on-year, and our acrylic yarn orders have also risen by 12%, especially for 32-count colored acrylic yarn; customer orders are already scheduled for next month," said Li Xiong, Marketing Manager, holding the latest industry report as he hurried into the production department office, just in time to see Factory Director Huang staring at the acrylonitrile price curve on the computer.
"Lao Li, you’ve come at just the right time. Look, Shandong Haijiang’s 130,000-ton acrylonitrile unit has temporarily shut down for maintenance, and Lihuayi’s quotation has dropped by 50 yuan, now at 7,900 yuan per ton," Factory Director Huang pointed at the screen, his tone filled with a hint of certainty. "We just signed long-term contracts with two suppliers last month, locking the price at 7,850 yuan, so this fluctuation won’t have much impact. However, you need to check out the new intelligent color matching system in the workshop—it now takes only 40 minutes to mix a color, half the time it used to take, and the color fastness has improved from level 3.5 to level 4. The Zhejiang customer who makes knitted sweaters added another 200 tons of peacock blue acrylic sliver yesterday."
This conversation is an ordinary scene in Antai Textile’s 32-year development history, yet it holds the code for this textile enterprise rooted in Zhangjiagang to navigate through cycles. Since its establishment in 1993, from initially producing a single type of acrylic sliver to now having a full product matrix covering acrylic yarn, colored acrylic sliver, and fancy yarn, every transformation step of Antai Textile has kept pace with industry trends.
In the first five months of this year, the industrial added value of China’s large-scale textile enterprises increased by 3.4% year-on-year, and the active consumer market has made "differentiation" a key word. Li Xiong敏锐ly noticed that competition for traditional white acrylic yarn is becoming increasingly fierce, while downstream clothing brands’ demand for "color as marketing" is exploding. "Look at young people buying clothes now—they look at color first, then style," he said, pulling up customer feedback on his phone. "The Fujian-based company that makes trendy brand sweaters used our gradient fancy yarn last year; their ‘sunset orange’ series sold like hotcakes, and this year they’ve tripled their order volume directly." To seize this wave of demand, Antai Textile invested 20 million yuan last year to upgrade its dyeing workshop, introducing an automatic dripping system and a spectrophotometer, increasing the color reproduction rate of colored acrylic sliver from 85% to 98%, and expanding the number of color numbers from over 200 to more than 500, making it one of the few enterprises in East China capable of quickly responding to "small-batch, multi-color" orders.
The confidence on the production side comes from the "hardcore team" led by Factory Director Huang. Faced with the dual requirements of energy consumption and efficiency in the textile industry, they began implementing "lean production" in 2023: replacing old spinning machines with intelligent equipment with automatic doffing functions, reducing labor by 30% while increasing single-spindle output by 15%; through a waste heat recovery system, reducing steam energy consumption in the dyeing process by 20%, saving nearly one million yuan in costs annually. "Now the per capita output value in the workshop has doubled compared to three years ago, and we just won the title of ‘Green Factory’ in Zhangjiagang City last month," Factory Director Huang said, leading the reporter to the sample cabinet at the end of the workshop—which displays everything from the coarse acrylic sliver of 1993 to today’s slub fancy yarn and colored-spot acrylic yarn. Each sample has a label reading "Customer: XX Brand" and "Application: Sportswear/Home Textiles/Toys," like a three-dimensional history of industry changes.
"The industry talks about ‘worries on the demand side,’ but what we see is ‘exploding segmented demand,’" Li Xiong looked at the trucks waiting to be loaded in the factory area outside the window, his tone firm. "Antai has been in the acrylic business for 32 years, and what we understand best is ‘creating extraordinary value from simple raw materials.’ In the second half of the year, we will also launch a biodegradable acrylic pilot production line, striving to roll out the combined strategy of ‘environmental protection + color’ next year—after all, the spring of the textile industry always belongs to those who can bring new colors to the market."
The machines in the workshop are still roaring, and a new batch of acrylic yarn printed with "Antai Textile" is flowing to the warehouse via conveyor belts. In a week, they will become a bright color on a T-shirt, a soft touch on a doll, or a unique texture in home textile fabrics, continuing to weave the story of this established textile enterprise resonating with the times.