Antai Textile: 32 Years of Dope Dyeing Technology Leads the Acrylic Fiber Industry, Yarns Sell Well at Home and Abroad as an Industry Benchmark
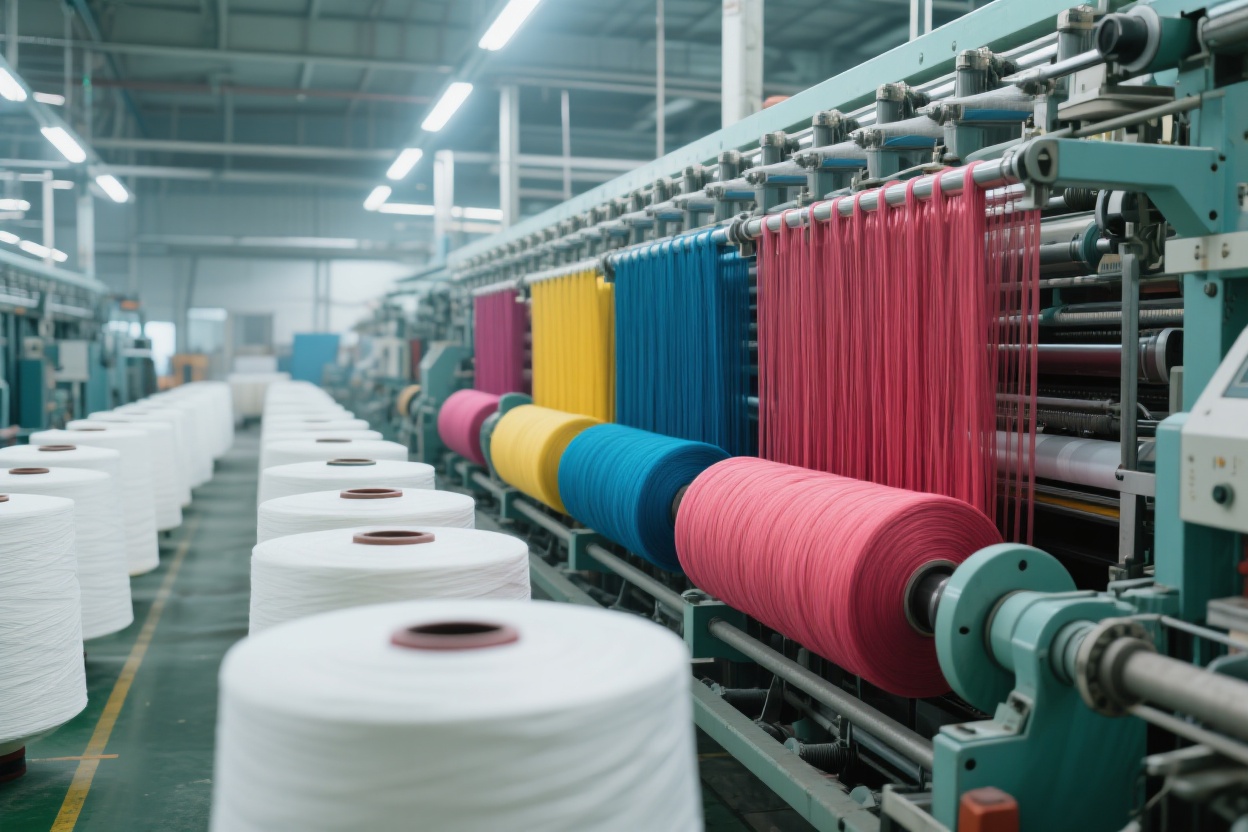
In Zhangjiagang in July, the summer heat is intensifying, but the production workshop of Antai Textile is bustling with orderly activity—dozens of spinning machines are running at high speed, and acrylic tops of various colors flow lightly along the production line, eventually turning into rolls of richly colored yarn. Li Xiong, the Marketing Manager, holding a freshly printed industry weekly report, hurried to the Production Department office. Pushing open the door, he saw Factory Director Huang recording data while looking at the raw material monitoring screen. "Director Huang, look at this set of data," Li Xiong spread the report on the table, "Huilong New Materials specifically mentioned when responding to investors last week that their dope-dyed polyester fibers are in strong demand in the downstream home textile and clothing sectors. Isn't this a 'peer signal' for our colored acrylic tops?"
Factory Director Huang adjusted his glasses, slid his fingertips on the screen, and pulled up Antai's production report: "Absolutely. We've been developing dope-dyed acrylic fiber technology since 2010, which is quite a few steps ahead of polyester. Look at this color fastness test data: after 12 process optimizations, our colored acrylic tops can withstand more than 40 washes, 15% higher than the industry average. Last year, we supplied a well-known home textile brand in Zhejiang, and they reported that the throw pillows made from our tops didn't fade after half a year of washing. This year, they directly increased their order by 30%."
As they were talking, a raw material market flash popped up on Li Xiong's phone: "Jilin Petrochemical's 260,000-ton acrylonitrile plant will be put into production at the end of the month; Shandong Haijiang's maintenance is also coming to an end. Currently, acrylonitrile inventory stands at 45,800 tons, and Lihuayi's quotation has dropped to 7,900 yuan per ton." Factory Director Huang's eyes lit up: "This is great news! Acrylonitrile is the 'grain' of acrylic fiber. We just signed long-term agreements with three raw material suppliers last month. Now, taking advantage of the price correction, the Production Department has adjusted the procurement plan, increasing the raw material reserve for the third quarter by 20%. This not only locks in costs but also ensures delivery times for downstream customers—last week, that high-end children's clothing customer in Shanghai urgently needed 500 tons of light pink acrylic yarn, and we shipped the goods in three days, thanks to the 'confidence' from our raw material warehouse."
While they were chatting, the Workshop Director hurried in and handed over a production report: "Director, Manager, our acrylic yarn production in the first half of the year increased by 8% year-on-year, especially fancy yarns like slub yarn and loop yarn—orders are scheduled until next month!" Li Xiong took the report and said with a smile: "This aligns with the overall environment. The National Bureau of Statistics just announced that yarn production of enterprises above designated size increased by 4.9% year-on-year; the consumer market has really come alive. Our newly launched 'Magic Color Acrylic Yarn' this year combines dope dyeing with fancy spinning technology, creating a gradient effect on a single yarn. Several clothing designer brands in Zhejiang are scrambling for it, saying it 'has an inherent sense of luxury' when used in autumn knitwear."
From a single acrylic top production line when it was founded in Zhangjiagang in 1993 to now having 8 intelligent spinning lines with an annual capacity of over 10,000 tons, becoming an industry benchmark, Antai Textile's 32 years are a microcosm of China's acrylic fiber industry moving from 'following' to 'leading'. "We also took detours in the early days," Factory Director Huang looked at the R&D building in the factory area outside the window, with a tone of emotion. "In 2015, low-cost dyed acrylic fiber was popular in the market, and many peers followed the trend of price cuts, but we gritted our teeth and invested 20 million yuan to build a laboratory to tackle the environmental protection technology of dope dyeing. Looking back now, that persistence was so worthwhile—traditional dyeing consumes 120 tons of water per ton, while our dope dyeing process only uses 8 tons and reduces sewage discharge by 80%. Now that the country is promoting 'dual carbon' goals, this is our core competitiveness."
Today, Antai Textile's acrylic yarns and colored acrylic tops have not only entered the production lines of hundreds of domestic home textile and clothing enterprises but also been sold to Southeast Asian and European markets through cross-border e-commerce. "Last week, a Spanish customer sent feedback saying that the blankets made from our acrylic yarn sold '300 pieces a day' at the local winter market," Li Xiong flipped through the customer reviews, his eyes full of smiles. "Next, we plan to integrate fancy yarns and dope dyeing technology more closely, such as developing acrylic loop yarn with metallic threads, so that products can not only meet environmental protection requirements but also offer more design variations."
The setting sun filtered through the workshop's glass windows, casting a warm glow on the operating machines. Li Xiong and Factory Director Huang stood side by side beside the production line, watching rolls of packaged acrylic products being transported to the warehouse by forklifts, soon to be shipped across the country. "The raw material market fluctuates, but demand keeps upgrading," Factory Director Huang said. "Antai's duty is to refine and perfect this 'thread' of acrylic fiber, making downstream customers feel at ease in using it and consumers feel comfortable in wearing it." This is perhaps the perseverance of a 32-year-old textile enterprise—weaving the industry's warmth and future into every strand of yarn.