Antai Textile: 32 Years of Deep Cultivation in Dope Dyeing, Weaving a New Future for Green Textiles with a Single Yarn
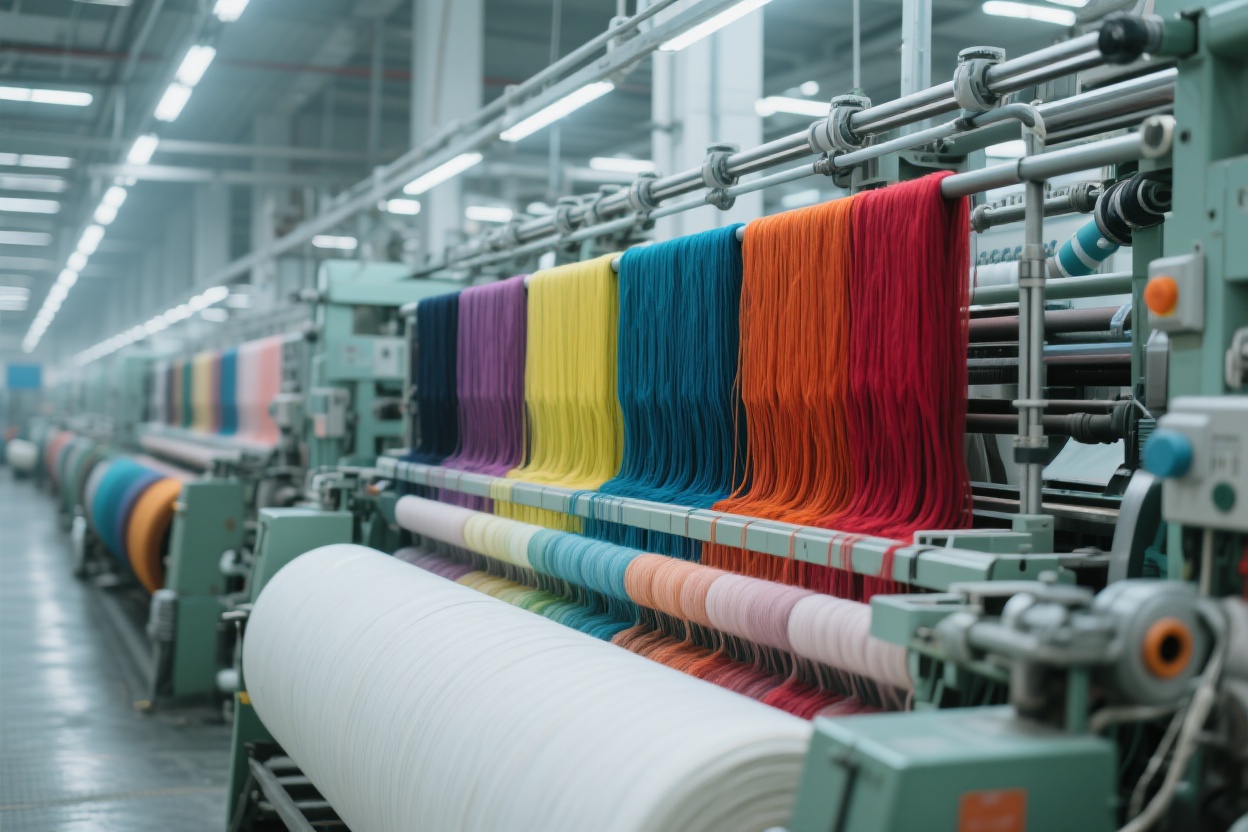
In Zhangjiagang in July, the summer heat is gradually intensifying, yet the production workshop of Antai Textile is filled with orderly busyness—crimson, lake blue, and off-white acrylic slivers flow on the intelligent production line. After drawing and twisting, they quickly turn into rolls of vibrant fancy yarns. Li Xiong, the Marketing Manager, has just finished a video conference with a home textile customer from the south. Holding the latest industry dynamics report, he heads straight to the Production Department office.
"Director Huang, I just saw that Huilong New Materials mentioned the application expansion of dope-dyed polyester. Isn't that exactly the 'old friend' field of our colored acrylic sliver?" Li Xiong puts the report on the table and points to a section, "The demand for green fibers in home textiles and apparel fabrics is becoming increasingly clear. With our 30 years of deep cultivation in dope-dyed acrylic, we now have more confidence."
Director Huang of the Production Department puts down the process parameter sheet, his eyes behind the lenses smiling: "Absolutely. Do you remember when we first started the factory in 1993, when our first acrylic sliver production line was just put into operation, customers were still纠结 that 'colored sliver is not as bright as post-dyeing'. Now, who doesn't praise our color fastness and environmental friendliness?" He stands up and walks to the workshop monitoring screen, pointing to the real-time data flow, "Take this batch of light gray acrylic sliver shipped to Zhejiang, for example. It uses the latest dope dyeing process, with color masterbatch evenly dispersed, and the batch color difference is controlled within △E ≤ 1.5. Customers use it for high-end knitted sweaters, directly weaving in the later process, eliminating the dyeing环节, and energy consumption is reduced by nearly 30%."
The topic naturally turns to the raw material end. Li Xiong flips to another piece of data: "The acrylonitrile inventory reached 45,800 tons last week, and Jilin Petrochemical's new 260,000-ton plant will also be put into operation at the end of the month. The raw material supply is becoming more and more sufficient."
"Our Production Department has been monitoring this news even earlier than you," Director Huang takes over, his tone showing the rigor of a technical person, "Raw materials are the foundation. We have long adjusted our procurement strategy—signed long-term agreement prices with two leading suppliers. Combined with the capacity release of the new plant, the procurement cost of acrylonitrile has decreased by 5% compared with the same period last year. More importantly, our intelligent batching system can automatically adjust the proportion parameters according to the slight differences in raw material batches. Look at the evenness CV value of this acrylic yarn, which is stably within 1.8. Customers all say 'Antai's yarn runs smoothly on the machine'."
Just as they are talking, Li Xiong's phone rings. It's an order confirmation from a fabric supplier in Hangzhou: "We need 50 tons of siro-spun acrylic yarn, T21S, specified to use our wine-red colored acrylic sliver as raw material." After hanging up the phone, he smiles at Director Huang and says, "You see, the price of pure polyester yarn at Hangzhou Juqian is stable, indicating solid demand in the basic market, but customers now value 'differentiation' more. Our this wine-red acrylic yarn was just used by a designer brand in Shenzhen to make sample clothes last month. The yarn has a subtle slub texture, made using our fancy yarn technology. The customer said 'it has more design sense than ordinary solid-color yarn'. This order has just been confirmed, and they will increase the order next quarter."
Since setting its first roots in Zhangjiagang in 1993, Antai Textile has been deeply engaged in the acrylic fiber field for 32 years. From the initial single acrylic sliver to the current full range of products covering colored acrylic sliver, acrylic yarn, and fancy yarn, it relies on this tacit cooperation of 'market acumen + technical precipitation'. Li Xiong remembers that three years ago, a European customer specifically requested 'degradable acrylic yarn'. At that time, there were few attempts in the industry. The company immediately joined forces with university R&D teams to replace part of the acrylonitrile with biomass-based raw materials. After hundreds of tests, it finally produced products that meet EU environmental standards, which have now become the main export products.
"In fact, what customers want is not just yarn, but 'peace of mind'," Director Huang looks at the slowly moving spindles in the workshop, his tone firm, "Stable raw materials, stable quality, stable delivery, plus a little differentiated ingenuity—this is the foundation of Antai's existence."
Outside the window, the Yangtze River water in Zhangjiagang flows quietly, just like the development of Antai Textile over more than 30 years—not chasing temporary hotspots, but only deepening and refining in the细分 field. From the adherence to dope dyeing technology, to the fine management of the raw material supply chain, and then to the innovative breakthroughs in fancy yarns, this textile enterprise rooted in the south of the Yangtze River is weaving the future of green textiles with the power of 'a single yarn', as well as a story of mutual growth and prosperity with upstream and downstream partners.