Antai Textile: Breaking into the High - end Acrylic Yarn Market with Differentiated Innovation and Telling the Resilience Story of Chinese Textiles
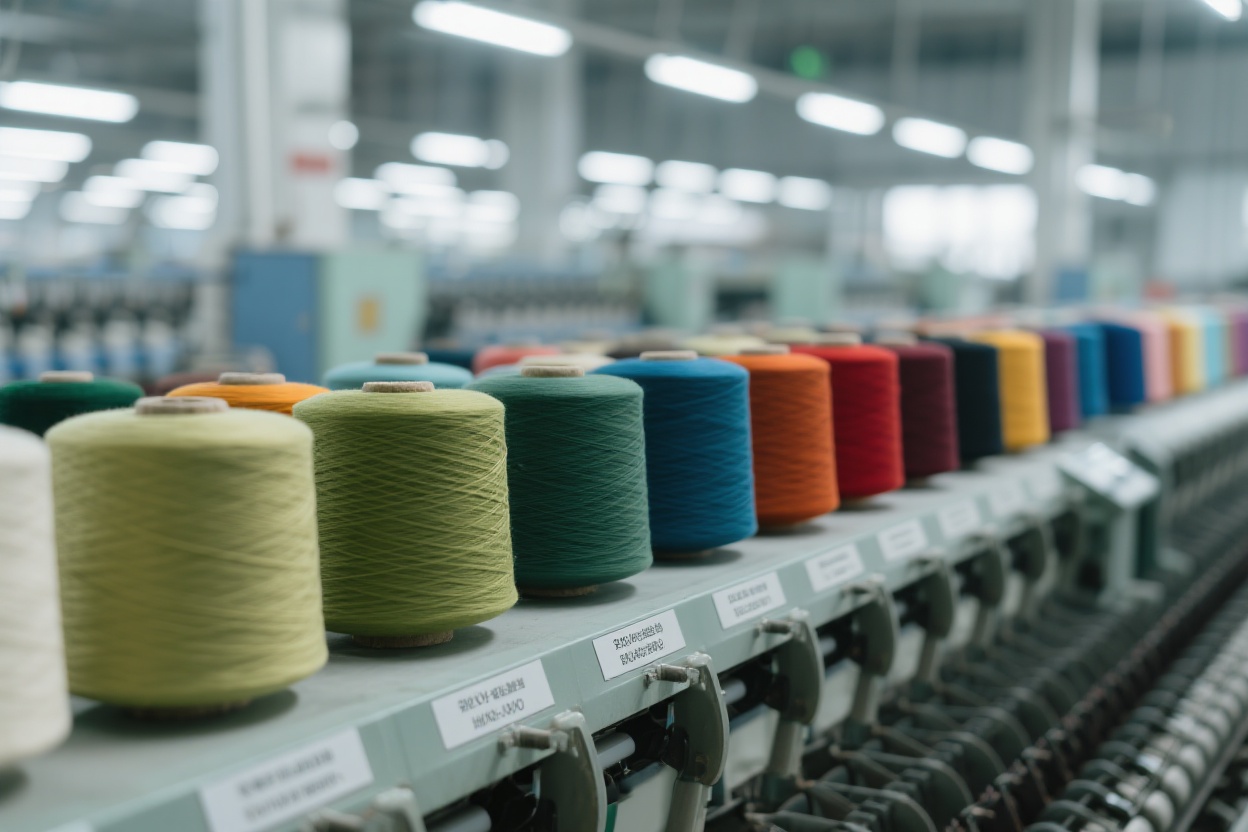
The early autumn in Zhangjiagang is filled with the unique mildness of the Jiangnan region. In the office of Antai Textile's marketing department, Li Xiong is lost in thought while looking at a stack of the latest industry reports. The data flashing on the screen is particularly eye - catching: the market scale of acrylic - cotton colored yarn is expected to exceed 1.5 million tons in 2025, with a compound annual growth rate of 8.3%. Automotive interiors and home textiles contribute more than 60% of the share. 'We've been waiting for these figures for three years,' he said as he picked up the phone and called the production department. 'Manager Huang, what's the customer feedback on that batch of low - VOC acrylic colored yarn for automotive interiors in the workshop?'
On the other end of the phone, the voice of Huang Zhiqiang, the production department manager, was accompanied by the background noise of machine operation. 'The quality inspection report has just come out. The color fastness is 4.5, and the formaldehyde content is far lower than the EU standard. The German customer immediately placed an additional order for 200 tons.' This 'veteran textile worker' who has spent 28 years in the spinning workshop paused for a moment, with pride in his tone. 'Do you remember the argument we had in the workshop three years ago? If you hadn't insisted on 'focusing on automotive interiors and high - end home textiles', we wouldn't have such confidence now.'
This 'argument' started in 2022. At that time, the Chinese acrylic market had just recovered from the trough. The production volume in 2023 rebounded to 604,000 tons, with a year - on - year increase in demand of 12.5%. However, the industry was generally caught in the dilemma of 'involution in conventional yarns and dependence on imports for high - end varieties'. Li Xiong took the market research data to Huang Zhiqiang. 'The downstream customers said that car seats made of ordinary acrylic yarns are prone to pilling, and the color fastness of home textiles is not enough. We must tackle the tough problem of 'differentiation'.'
They got right to work. Antai Textile invested 20 million yuan to upgrade the production line, and Huang Zhiqiang led the technical team to stay in the workshop for three months. They started from the raw material end and cooperated with the Chinese Academy of Sciences to develop modified acrylic fibers. They combined ultra - fine denier fibers with antibacterial masterbatches to develop composite acrylic sliver with a diameter of only 0.8 denier. This yarn, which is even thinner than a hair, can produce fabrics that are not only soft and skin - friendly but also can pass the 'no pilling after 100,000 rubs' test for automotive interiors. At the same time, they introduced an intelligent color - matching system, upgrading the traditional 'manual color mixing' to digital control. The color difference accuracy has been improved from level 1 to within 0.5 level, and the production efficiency of colored acrylic sliver has increased by 40%.
'Previously, when a customer wanted a new color, we had to conduct trial production for three to five batches. Now, with one - click color matching on the computer, samples can be produced within 24 hours,' Huang Zhiqiang pointed to the intelligent warehousing system in the workshop. 'The AGV robots installed last year have increased the raw material turnover efficiency by 60%. Even German counterparts gave a thumbs - up when they came to visit.' This 'green + intelligent' transformation has just hit the rhythm of the industry's development - reports show that the core competitiveness of acrylic yarn in the future is focusing on this.
As a long - established textile enterprise founded in 1993, Antai Textile has witnessed the ups and downs of the Chinese textile industry. From the initial single - product production of acrylic yarn to the current formation of four major product lines including acrylic yarn, acrylic sliver, colored acrylic sliver, and fancy yarns, it owes this to its keen sense of market trends. In 2024, the global market scale of acrylic colored yarn reached $15 billion, with China accounting for more than 40%. Antai Textile's colored acrylic sliver, with its advantages of 'high color fastness and low energy consumption', has occupied 15% of the domestic high - end home textile market, and its cooperative customers include leading brands such as IKEA and KUKA.
'Look at this latest forecast. The global market will reach $22 billion in 2030, and the Asia - Pacific region will be the main force,' Li Xiong flipped to the last page of the report and fixed his eyes on the conclusion of 'China will continue to lead'. 'We've just received an inquiry from a North American customer who wants a batch of flame - retardant acrylic yarn for yacht interiors. Manager Huang, are you ready to tackle another tough problem?'
Huang Zhiqiang's hearty laughter came from the other end of the phone. 'The new biodegradable dye production line in the workshop has just been debugged and is on standby at any time!'
Outside the window, the container terminal in Zhangjiagang Free Trade Zone is busy loading and unloading goods, and many of them are marked with the logo of 'Antai Textile'. This textile enterprise, which has been rooted in the Jiangnan region for 30 years, is breaking through the 'low - end involution' with differentiated products and opening the door to the high - end market with green and intelligent technologies. In the golden growth period of the acrylic yarn industry, it is telling the'resilience story' of Chinese textiles.