Antai Textile: Steering Through Market Storms, Weaving a New Textile Future with 'Intelligent' Manufacturing and Green Initiatives
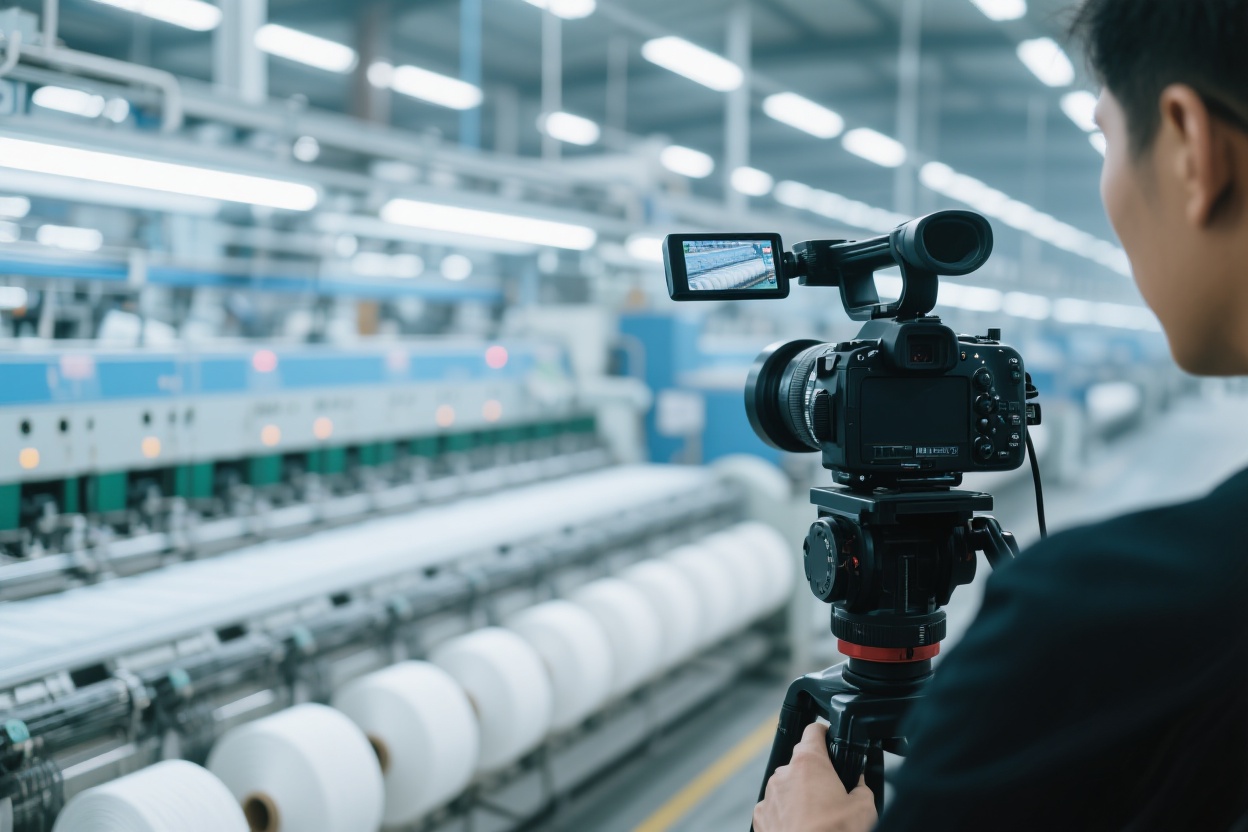
In Zhangjiagang in July, the Yangtze River water, carrying the damp heat of early summer, laps against the embankment, yet there is a calm busyness in the production workshop of Antai Textile — the hum of intelligent spinning machines has a steady rhythm, and on the central control screen, real-time data on the twist and tension of each acrylic yarn spindle is jumping. Li Xiong, the Marketing Manager, stands in front of the data dashboard, his fingertips gliding over the July acrylic price forecast curve. Behind this sharply fluctuating line lie crude oil price volatility triggered by the Israel-Iran conflict, uncertainty surrounding Jilin Chemical Fiber's production plans, and pending U.S. tariff negotiations. 'Uncertainty is indeed increasing, but for Antai, there are opportunities hidden in the fluctuations,' he says, looking up towards the depths of the workshop where Factory Director Huang of the Production Department is leading his team in commissioning newly arrived bio-based raw material proportioning equipment.
This textile enterprise, rooted in Zhangjiagang since 1993, has focused on the R&D and production of acrylic yarns, acrylic tops, colored acrylic tops, and fancy yarns for over three decades, and has long honed the ability to steer through market storms. In the first half of 2025, when the Israel-Iran conflict pushed up crude oil prices, which in turn drove up the cost of acrylonitrile, most peers were still watching, but Antai Textile took the lead in launching its 'dual-track' raw material strategy: on one hand, it locked in some long-term acrylonitrile orders with long-term cooperative petrochemical enterprises to stabilize short-term cost fluctuations; on the other hand, it accelerated the pilot testing of bio-based acrylic raw materials — this new type of raw material based on plant starch can not only reduce dependence on crude oil but also lower carbon emissions during production. 'Speculative restocking by downstream enterprises has brought inventories to a recent low; at this time, whoever can stabilize supply and ensure quality will seize customers,' Li Xiong says with confidence, which stems from the intelligent production base the company has built in Zhangjiagang, Jiangsu: 12 acrylic top production lines, 80,000 spindle spinning equipment, combined with an ERP system and IoT monitoring, enabling full-process traceability from raw materials to finished products, and responding to customers' small-batch customization needs in as fast as 48 hours.
Looking further into the future, Antai Textile has already set its sights on the emerging 'blue ocean'. According to industry forecasts, the market size of China's acrylic-cotton blended dyed yarns will grow from 15 billion yuan to 19.5 billion yuan from 2025 to 2030, with a compound annual growth rate of 4.3%, and high-end and green development are clear growth mainlines. 'This is exactly the field we excel in,' Factory Director Huang says, wiping the sweat from his forehead and pointing to a set of operating 'waterless dyeing' equipment in the workshop. 'Traditional acrylic dyeing requires multiple processes such as scouring, bleaching, and dyeing, which consumes a lot of water. However, our colored acrylic tops adopt the melt coloring process, incorporating color masterbatches during the spinning stage, allowing downstream enterprises to directly blend them, saving more than 80 tons of water per ton of yarn.' The colored acrylic tops produced by this process not only have a color fastness of above level 4 (industry average is level 3) but also can accurately reproduce difficult-to-dye colors such as red, blue, and purple, and have now become the designated raw material for many domestic and foreign sportswear brands.
Facing the market competition pattern of 'high in the east, low in the west', Antai Textile's strategy is to 'build walls with technology and expand territories with services'. In the eastern coastal areas, relying on the intelligent production capacity of the Zhangjiagang base (the penetration rate of intelligent equipment has now reached 45%, and is planned to exceed 60% by 2027), it focuses on personalized orders from high-end brands, such as the 'Yunrou' series of fancy yarns customized for light luxury home textile enterprises. Through a special slub twist process, the acrylic yarn has both the fluffiness of wool and the crispness of polyester; in central and western China and emerging markets, it launches cost-effective basic acrylic-cotton blended yarns, and has gradually established a warehousing network covering Chengdu-Chongqing and Wuhan by virtue of stable quality and fast delivery cycles. 'Raw material price fluctuations and international trade frictions are common problems in the industry, but for Antai, the 30-year accumulated process database and flexible production scheduling capacity are our 'risk-resistant buffer',' Li Xiong adds. The company's R&D center, upgraded with an investment of 20 million yuan last year, has successfully developed 12 acrylic yarn formulas suitable for different blending ratios, which can adjust the ratio in real-time according to fluctuations in cotton and acrylic prices to help downstream customers control costs.
From the commissioning of its first acrylic top production line in 1993 to now becoming an industry 'hidden champion' with an annual capacity of over 30,000 tons, Antai Textile's story is a microcosm of Chinese textile enterprises seeking stability amid changes and pursuing progress amid trends. When the market is anxious about short-term price fluctuations, it is honing its technological 'internal strength'; when the industry is transforming towards green and high-end development, it has already prepared mature solutions. As Factory Director Huang often says to the workshop workers: 'What we spin is not just fibers, but trust.' In the early morning light of Zhangjiagang, Antai Textile's intelligent workshop is still operating, and the acrylic fibers wound on the spindles are weaving new possibilities for the upgrading of traditional textiles towards 'intelligent' manufacturing.