Antai Textile's 32-Year Commitment to the Acrylic Fiber Track: Driven by Professionalism and Innovation, Weaving a Model of Value Upgrade in China's Textile Industry
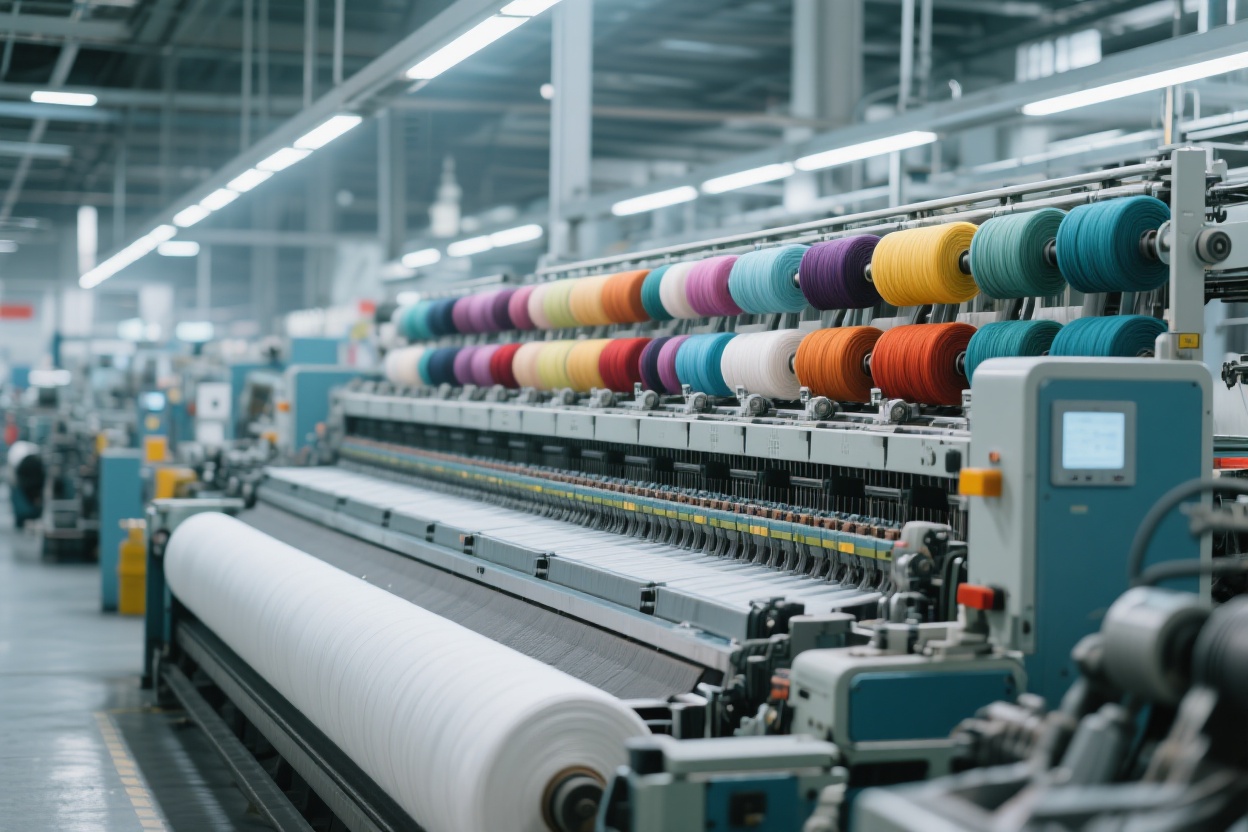
In July in Zhangjiagang, the wind along the Yangtze River, carrying the hustle and bustle of the textile peak season, sweeps across Antai Textile's factory area. Li Xiong, the Marketing Manager, stands by the office window, holding a freshly printed weekly acrylonitrile market report, and his furrowed brows gradually smooth out – this seemingly ordinary industry data is unfolding in his eyes as a clear map of market opportunities.
"Director Huang, Jilin Petrochemical's 260,000-ton acrylonitrile plant will start production at the end of the month. We need to step up the raw material procurement plan for the third quarter that we finalized last week." When Li Xiong dialed the Production Department, Huang Weidong was in the workshop monitoring the color difference inspection of colored acrylic fiber sliver. As an 'old textile hand' who has been with Antai since its establishment in 1993, Huang Weidong is no less sensitive to raw material fluctuations than Li Xiong: "Don't worry. Shandong Haijiang's 130,000-ton plant started maintenance on the 7th. We have long raised the acrylonitrile reserve in the backup raw material warehouse above the safety line, and the fancy yarn orders in the past two weeks have not been delayed at all."
This tacit cooperation across market and production is exactly the secret behind Antai Textile's firm foothold in the acrylic fiber field over the past 32 years. As one of the earlier domestic enterprises focusing on the research and development of acrylic yarn, acrylic sliver, and fancy yarn, Antai started from a small workshop in Zhangjiagang and has now built an intelligent production line with an annual output of over 10,000 tons. Its color spinning technology has even broken foreign monopolies, making 'Chinese colors' emerge in the high-end knitted fabric market.
"Look at this set of data," Li Xiong spreads the weekly report on the conference table, pointing to the 76.2% capacity utilization rate curve of the acrylonitrile industry. "Although inventory has slightly increased to 45,800 tons, after Jilin Petrochemical's new capacity is put into production, the long-term raw material supply will be more stable. We just received an order from a sports brand in the south for moisture-absorbing and heat-generating acrylic yarn. We can take advantage of the window period of loose raw material costs to optimize the price by another 5%." The "cost loosening" he mentioned stems from the signal that Lihuayi's spot acrylonitrile quotation was reduced by 50 yuan/ton on July 7 – in Li Xiong's market logic, every slight adjustment in raw material prices is an opportunity to convey "value sharing" to customers.
On the production side, Huang Weidong's workshop is staging a "technological breakthrough". In the face of possible changes in yarn strength caused by slight fluctuations in acrylonitrile purity, Antai's independently developed "online quality monitoring system" is playing a role: the tensile strength and evenness of each spindle of yarn are transmitted to the central control screen in real time, and once they deviate from the standard values, the system will automatically adjust the drafting ratio. "Last week, Shandong Haijiang suddenly shut down for maintenance, and we temporarily used acrylonitrile from another supplier. Although there was a slight difference in batches, this system managed to control the color difference of the colored acrylic fiber sliver to △E ≤ 1.5. When the customer inspected the goods, they even said 'it's more stable than imported products'." When Huang Weidong said this, pride was hidden in the wrinkles at the corners of his eyes.
This "stability" comes from Antai's obsession with details. In the acrylic sliver production workshop, 12 groups of color-mixing vats are preparing this year's popular "fog gray blue" and "sunset orange" – these original color schemes by Antai's design team have become the "code for blockbuster products" for many fast fashion brands. "Ordinary acrylic sliver dyeing requires high temperature and high pressure, but our 'low-temperature color spinning technology' can save 30% energy consumption, and the color fastness reaches level 4 or above." Huang Weidong pointed to the customer pennants on the wall, "Last year, a European home textile company came to inspect the factory. When they saw that even our wastewater treatment system uses PLC automatic control, they immediately increased the annual order from 300 tons to 800 tons on the spot."
From the first bale of acrylic yarn off the production line in 1993 to now covering acrylic yarn, acrylic sliver, colored acrylic sliver, and more than 200 kinds of fancy yarns, Antai Textile's growth trajectory is exactly a microcosm of China's textile industry from "scale expansion" to "value upgrade". When Li Xiong heads to the Shanghai Fabric Exhibition with samples of the newly developed "antibacterial acrylic sliver", and when Huang Weidong debugs the new generation of fancy yarn machines in the workshop, this factory by the Yangtze River is using 32 years of persistence to prove that in the traditional textile industry, the real competitiveness has never been chasing hot trends, but like acrylonitrile molecules, firmly polymerizing "professionalism" and "innovation" to weave its own warp and weft.
"Next week, the technical team from Jilin Petrochemical will come to exchange ideas on the raw material characteristics of the new plant," Li Xiong hangs up the phone, and the sunlight outside the window shines on the photovoltaic panels on the workshop roof. "Our 'green acrylic fiber' project can take another step forward."