Antai Textile: Dope Dyeing Technology Solves Environmental Challenges, Peacock Blue Acrylic Top Opens the Door to the ASEAN Market
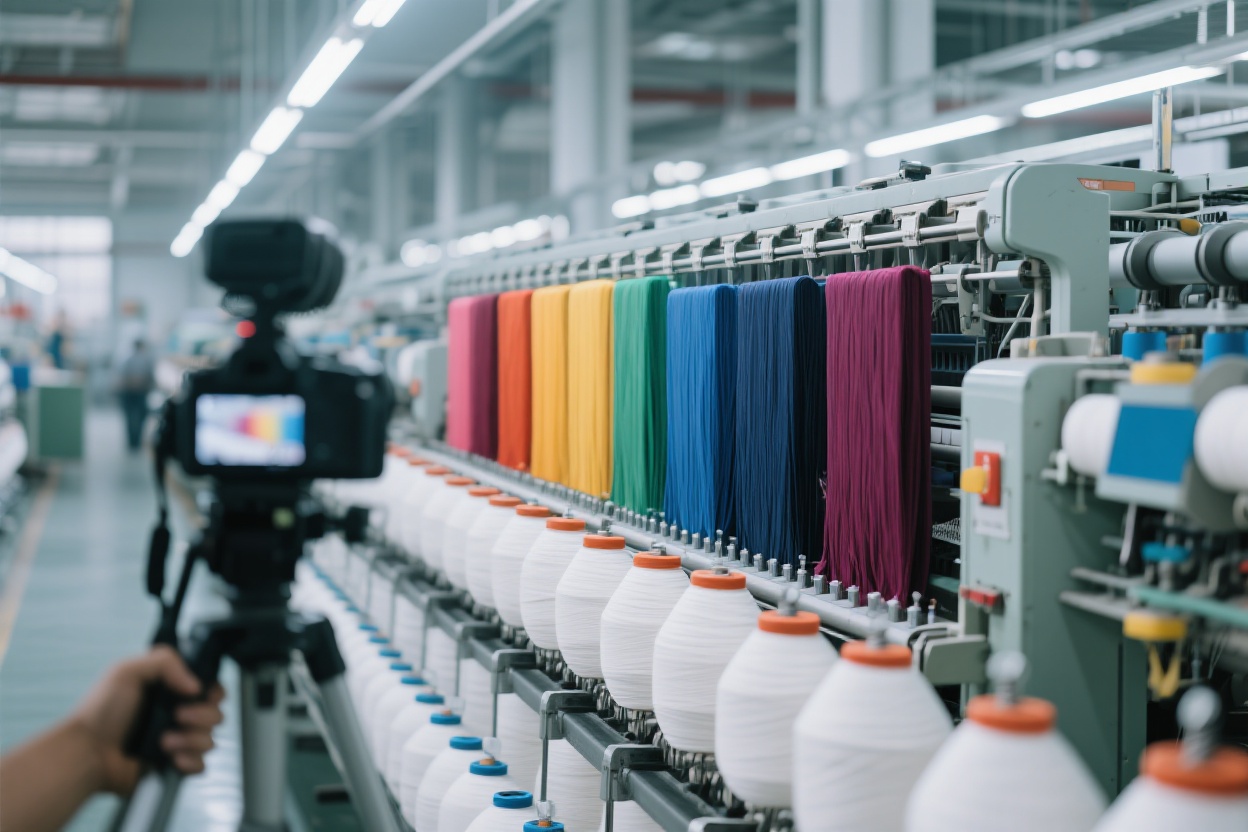
In early autumn in Zhangjiagang, sunlight streams through the high windows of Antai Textile's production workshop, falling on rolls of brightly colored acrylic tops. Factory Director Huang of the Production Department is staring at the peacock blue acrylic top just off the production line, holding a color fastness tester in his hand. "Level 4.5, stable!" He looks up and smiles at Li Xiong, the Marketing Manager beside him, "This batch of samples for ASEAN customers should satisfy them."
Li Xiong runs his fingertips over the fine texture of the acrylic top, recalling the video conference three days ago with the purchasing director of a well-known Southeast Asian home textile brand. "We need more color options, and more importantly, the production process must meet EU environmental standards, and carbon emissions in the dyeing and finishing process must be reduced." The customer's needs are clear and urgent, which is exactly the direction Antai Textile has been deeply exploring in recent years. As a veteran in the acrylic fiber field rooted in Zhangjiagang since 1993, this company, which started with a single acrylic yarn production, has now grown into a comprehensive supplier covering acrylic yarn, acrylic top, colored acrylic top, and fancy yarn. The breakthrough in dope dyeing technology is the "golden key" for them to pry open emerging markets.
"Do you remember when we first started researching dope dyeing five years ago, there were hundreds of failed color masterbatch formulas piled up in the workshop?" Director Huang's voice pulls the thoughts back to 2018. At that time, the problems of high water consumption and unstable color fastness in traditional dyeing processes became increasingly prominent, and the industry news that "domestic enterprises have broken through dope dyeing technology" made the Antai team敏锐ly sense the opportunity. "At that time, we judged that environmentally friendly acrylic fiber would definitely become the mainstream." Director Huang recalled that the team plunged into the laboratory, tackling technical difficulties one by one from color masterbatch dispersibility to spinning temperature control. Today, Antai's environmentally friendly acrylic fiber can stably produce 48 color spectrums with color fastness reaching 4-5 grades. More importantly, it saves 76% water compared with traditional dyeing processes - this data is exactly the most confident "green business card" for Li Xiong when communicating with ASEAN customers.
Market changes always confirm the value of forward-looking布局. Li Xiong opens the latest export data report. As the core of national acrylic fiber production capacity (accounting for 62%), the Yangtze River Delta region, with Antai relying on the industrial cluster advantages of Zhangjiagang, has long established an efficient supply chain from raw materials to finished products. But he also noticed that the news mentioned that "central and western provinces attract capacity to move westward with electricity fee discounts, and the ton cost of new projects can be reduced by 800 yuan." "We do not blindly follow the trend to relocate, but digest cost pressures through technological upgrading." Li Xiong explained, for example, combining dope dyeing technology with intelligent spinning equipment, production efficiency has increased by 20%, while unit energy consumption has decreased by 15%. "In this way, even in the face of the cost advantages of the central and western regions, our base in the Yangtze River Delta can still maintain competitiveness."
A more far-reaching layout is hidden in the product structure. The industry differentiation rate was 35% in 2023, and it is expected to rise to 55% by 2030. Functional products such as flame retardant, antibacterial, and conductive have become R&D priorities - this set of data has long been written into Antai's strategic plan. In the functional yarn test area on the other side of the workshop, Director Huang picks up a roll of gray-black acrylic yarn: "This is our newly developed antibacterial and flame-retardant acrylic fiber, used in hotel home textiles and protective clothing, and has passed the EU OEKO-TEX® certification." He revealed that the proportion of orders for such functional products is growing at an annual rate of 12%, and in the fancy yarn workshop, segment dyeing and slub yarn combined with dope dyeing technology have become the "new favorites" of designer brands.
When "circular economy" becomes an industry buzzword, Antai's actions are equally swift. The news mentions that "the proportion of recycled acrylic fiber is expected to increase from 3% to 12%, promoting a 18% reduction in industry carbon emission intensity", and Antai is one of the first 12 leading domestic enterprises to complete the layout of recycled acrylic fiber pilot production lines. "We use recycled PET bottle flakes to make recycled acrylic fiber raw materials, and then directly spin colored yarn through dope dyeing, with almost zero sewage discharge throughout the process." Director Huang pointed to a production line being commissioned, "This line will be put into production next month, and then the recycled acrylic fiber production capacity will account for 15% of our total output, 3 percentage points higher than the industry target."
As they speak, Li Xiong's phone rings; it's a reply from the ASEAN customer: "The sample test has passed! We will place an order for 200 tons next month, focusing on the two color systems of peacock blue and olive green." After hanging up the phone, he looks out at the Yangtze River outside the workshop, where cargo ships come and go on the river. From the first acrylic yarn rolling off the production line in 1993 to now, with products sold far to emerging markets such as ASEAN and the Middle East (demand in these regions is growing at an annual rate of 8%), Antai Textile's 30 years is exactly a microcosm of China's acrylic fiber industry from scale expansion to high-quality development.
"Next, we need to further amplify the carbon emission advantages of dope dyeing technology." Director Huang's gaze falls on the slogan on the workshop wall - "Let every yarn carry a green temperature". The news says that "dope dyeing technology can reduce carbon emissions in the dyeing and finishing process by 35% by 2025", and Antai's goal is to increase this figure to 40% by 2026. Sunlight once again sweeps over those colorful acrylic tops, as if one can see them becoming curtains in Southeast Asian homes and carpets in the Middle Eastern market in the future, carrying Zhangjiagang's craftsmanship and green commitment to a broader world.