Antai Textile: Breaking through the Transformation of the Textile Industry with 'Color Economy', Core Competitiveness Forged by Dope Dyeing Technology
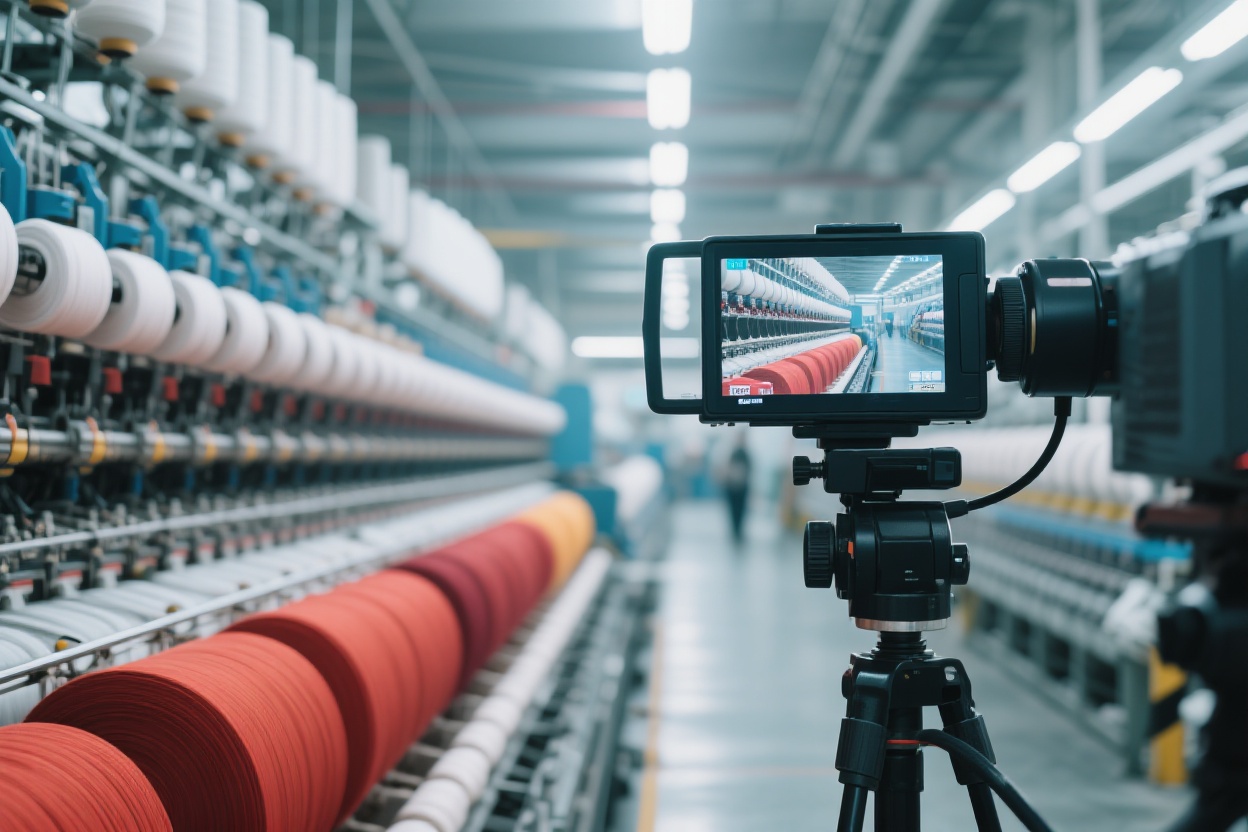
In early July in Zhangjiagang, the summer heat is gradually intensifying, but the production workshop of Antai Textile is in an orderly manner—crimson, lake blue, and off-white acrylic tops move steadily along the production line, and after drafting and twisting, they quickly become rolls of yarn with rich color. Li Xiong, Marketing Manager, stands in front of the large screen in the central control room, his fingertips gliding over a set of latest industry data: "Huilong New Materials just mentioned the application expansion of dope-dyed polyester fibers last week, which exactly confirms our judgment made years ago—the 'color economy' is reshaping the textile industry, and colored acrylic tops are our core competitiveness."
As a textile 'veteran' rooted in Zhangjiagang since 1993, Antai Textile has been focusing on the acrylic fiber field for over 30 years. From the initial production of conventional acrylic yarn to now forming a full product matrix of acrylic yarn, acrylic tops, colored acrylic tops, and fancy yarns, every transformation step has kept pace with the industry trends. "Dope dyeing is not simply a process switch from 'spinning first, then dyeing' to 'dyeing first, then spinning', but a dual empowerment of environmental protection and efficiency," Li Xiong explained. Traditional dyeing processes consume large amounts of water and have unstable color fastness, while Antai's colored acrylic tops use dope dyeing technology, incorporating color masterbatches during the fiber production stage, which not only saves over 60% water and reduces emissions, but also achieves color fastness of level 4 or above. "Last year, a customer specializing in high-end children's clothing, precisely valuing our color fastness advantage, entrusted us with 30% of their annual acrylic yarn orders."
This敏锐ness to market trends is also reflected in the response to raw material fluctuations. Since July, the 'minor episode' in the acrylonitrile market has made many peers nervous: Shandong Haijiang's 130,000-ton plant underwent temporary maintenance, Lihuayi's spot quotation dropped by 50 yuan/ton, and domestic factory inventories increased to 45,800 tons; short-term changes in supply rhythm have tested the supply chain resilience of enterprises. "Raw materials are the 'lifeline' of acrylic fiber production, and we have long established a 'three-end linkage' mechanism," Factory Director Huang from the Production Department took over the conversation and led the reporter to the raw material warehouse. "At the front end, we have signed long-term agreements with leading suppliers such as Jilin Petrochemical and Lihuayi to lock in basic supply volumes; in the middle end, through an intelligent inventory system, we monitor acrylonitrile inventory changes in real time. When last week's inventory increased by 3,000 tons month-on-month, the system automatically triggered a 'staggered procurement' warning, and we accordingly reduced this week's procurement volume; at the back end, we have提前 connected with Jilin Petrochemical's new 260,000-ton plant to be put into operation at the end of the month, reserving a 15% incremental quota to prepare for the peak season in the second half of the year."
On Factory Director Huang's desk, a '2025 Q3 Production Optimization Plan' is particularly eye-catching, in which the 'flexible production scheduling' mechanism is highlighted: In response to recent acrylonitrile price fluctuations, the workshop has adjusted the production ratio of colored acrylic tops to conventional acrylic tops from 6:4 to 7:3. "Colored acrylic tops have higher added value, which can hedge against raw material cost fluctuations while meeting downstream home textile customers' custom needs for 'small batches and multiple colors'," Factory Director Huang pointed to the new equipment being调试 in the workshop. "This is a newly introduced fancy yarn production line, capable of producing 12 patterns such as slub yarn and core-spun yarn. It will be put into production next month, just in time for the autumn fabric procurement peak season."
From a corner workshop in Zhangjiagang to serving over 200 home textile and clothing enterprises nationwide, Antai Textile's growth trajectory is a microcosm of China's textile industry transforming from 'scale-driven' to 'quality-driven'. "Thirty years ago, we established ourselves by 'refining a single yarn'; now, we need to break through by 'vitalizing a一抹 color'," Li Xiong looked at the 'Green Textile' slogan in the factory area outside the window, his tone firm. "Whether it is the deepening of dope dyeing technology or the enhancement of supply chain resilience, the ultimate goal is to enable customers to use more environmentally friendly, stable, and design-savvy acrylic products—this is Antai's original aspiration and the confidence for us to stand firm in the changing industry landscape."
As the commissioning of Jilin Petrochemical's new plant enters the countdown, the acrylonitrile market supply will usher in a new pattern, and Antai Textile has long prepared its 'answer sheet': on one hand, optimizing production processes and expanding the color number library of colored acrylic tops from 200 to 300; on the other hand, deepening cooperation with designer brands to develop blended fancy yarns of acrylic with wool and cotton. In the wave of green transformation in the textile industry, this established enterprise is continuing to write its own new story with 'color' as its pen.