Antai Textile: Weaving a New Chapter in the Upgrade of the Textile Industry Amid the Turbulence of the Acrylonitrile Market
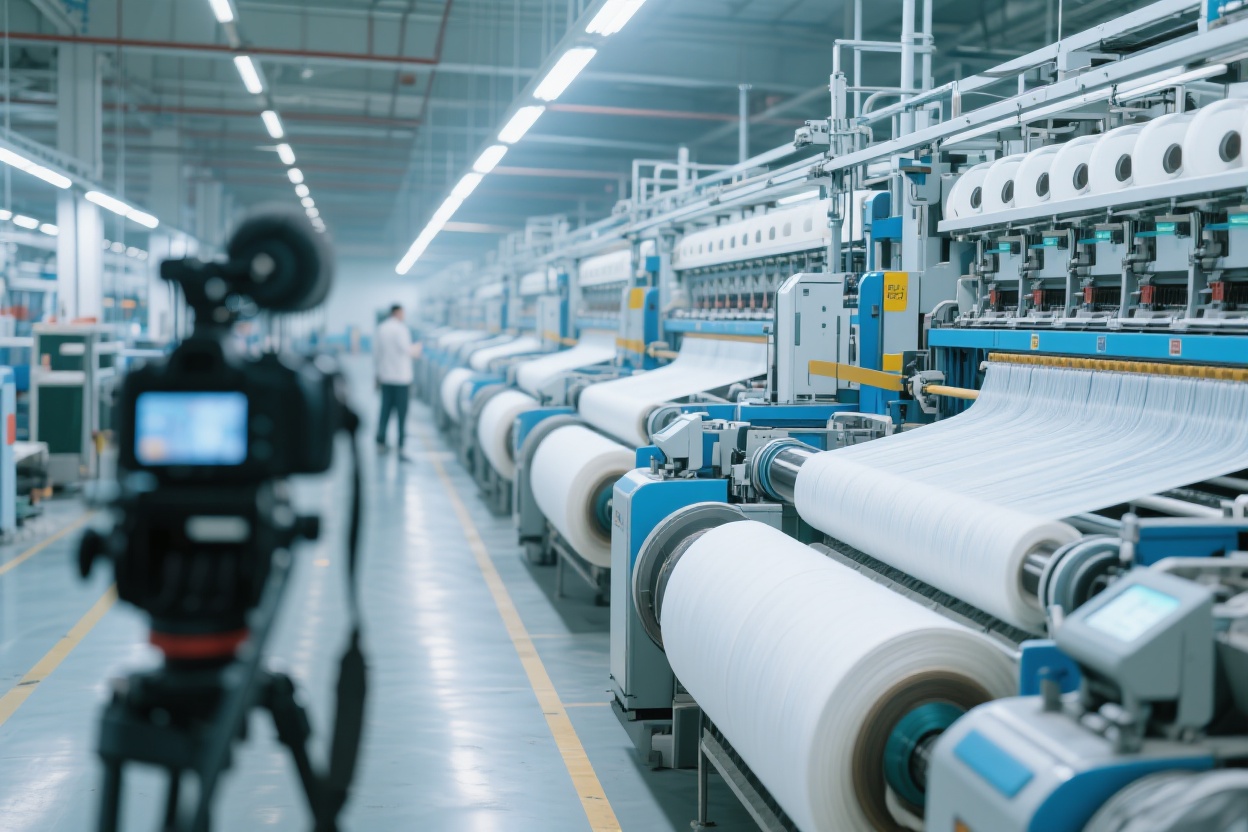
In mid-July in Zhangjiagang, the summer heat was intensifying, yet the conference room of Antai Textile exuded a focused calm. Li Xiong, the Marketing Manager, ran his finger across the latest weekly report on the acrylonitrile industry, then looked up at Factory Director Huang from the Production Department opposite him: 'Brother Huang, the newly received data shows that the acrylonitrile capacity utilization rate has reached 76.20%, inventories have increased by 3,000 tons compared to last week, Jilin Petrochemical's new 260,000-ton plant will start production at the end of the month, and Shandong Haijiang's 130,000-ton plant has been temporarily shut down for a 10-day maintenance... This raw material market is truly 'sunny in the east, rainy in the west' (unpredictable).' Factory Director Huang put down the production schedule in his hand, took the report and examined it carefully, his brows furrowing slightly then relaxing: 'Raw materials are the 'backbone' of acrylic yarn. When there are fluctuations on both the supply and demand sides, our production has to 'step in time'. Look, Lihuayi has lowered its quotation by 50 yuan to 7,900 yuan, indicating that short-term supply is a bit loose. However, after Jilin Petrochemical's new capacity comes online, long-term cost pressures may ease, and Haijiang's maintenance will tighten the local supply somewhat—this 'dynamic balance' is precisely an opportunity for an old factory like ours.' This conversation is a microcosm of how Antai Textile has responded to market changes over the past three decades. Since rooting in Zhangjiagang in 1993, this textile enterprise, mainly engaged in acrylic yarn, acrylic top, colored acrylic top, and fancy yarn, has long been accustomed to navigating the 'tides' of the raw material market. As the core raw material for acrylic fiber, every slight change in acrylonitrile's production capacity, inventory, and price affects the nerves of the downstream industrial chain. The secret of Antai Textile lies in its market acumen of 'staying half a step ahead' and steady and solid production resilience. 'Take Shandong Haijiang's maintenance this time, for example. We got the news from our supply chain partners a week ago,' Li Xiong pulled up the procurement records on his phone. 'We immediately adjusted the procurement rhythm of acrylonitrile and locked in some supply sources before Lihuayi adjusted its price, saving at least 30 yuan per ton in costs. More importantly, this is when our colored acrylic top production line can 'show its strength'.' He explained that in traditional acrylic yarn production, downstream enterprises often need to dye the yarn themselves, but Antai Textile's colored acrylic top adopts dope dyeing technology, embedding color from the source. This not only saves the time and environmental protection costs of the downstream dyeing process but also helps customers lock in profits through the 'finished product' form when raw material prices fluctuate—'Recently, several clothing brand customers in Zhejiang have added an order for 300 tons of sapphire blue acrylic top, precisely taking a fancy to our advantage of 'ready-to-use and controllable cost'.' In the production workshop, Factory Director Huang's confidence comes from the intelligent production line that has been in operation for five years. 'Look at this acrylic yarn production line. It real-time monitors the conversion rate of acrylonitrile through an IoT system, and the raw material consumption per ton is 2.3% lower than the industry average,' he pointed to the jumping data on the screen. 'After receiving the market warning from Li Xiong last week, we immediately switched the production ratio, increasing the capacity of high-count acrylic yarn from 40% to 60%—high-count yarn itself has high added value and stronger resilience to raw material price fluctuations, which exactly matches the current demand of brand customers for 'lightweight, high-quality' fabrics.' In the workshop, rolls of snow-white acrylic yarn are being wound into bobbins by automatic winding machines, while the adjacent fancy yarn production line is much busier: slub yarn, loop yarn, and speckled yarn constantly change forms as the machines run. These 'creative yarns' that once relied on manual design can now real-time respond to customers' personalized needs through Antai's independently developed pattern database. Thirty years ago, Antai Textile started with a single acrylic top spinning machine; today, it has grown into an industry backbone with an annual production capacity of over 20,000 tons. From initially only being able to produce basic acrylic yarn, it now has more than 20 categories of segmented products such as colored acrylic top and functional fancy yarn, with cooperative customers covering well-known domestic and foreign clothing and home textile brands. Behind this growth is a deep understanding of the entire 'raw material-production-market' chain—while most enterprises are still passively responding to the rise and fall of raw material prices, Antai has long transformed market changes into opportunities for product innovation by establishing a 'raw material price early warning model' and a 'dynamic customer demand database'. 'After Jilin Petrochemical's new plant is put into production, the supply of acrylonitrile will be more sufficient, and we plan to feed this cost dividend back into new product R&D,' Li Xiong's gaze fell on the '2025 Product Plan' chart on the conference room wall, where the words 'bio-based acrylic yarn' were particularly eye-catching. 'This yarn to be launched in the second half of the year uses renewable raw materials to replace part of the acrylonitrile. Current laboratory data shows that environmental indicators have improved by 40%, and European customers are already waiting for samples.' Outside the window, the Yangtze River flows slowly eastward, just like Antai Textile's development course over more than three decades. In the tide of the textile industry, it has not only maintained a keen insight into market changes but also adhered to the original aspiration of 'establishing the enterprise with quality and empowering it with innovation'. As the 'turbulence' in the acrylonitrile market rises again, this enterprise from Zhangjiagang is weaving a new story of transformation and upgrading in the traditional textile industry with every acrylic yarn.