Antai Textile: Dope Dyeing Technology Leads Green Transformation, Forging Global Invisible Champion in Colored Acrylic Fibers
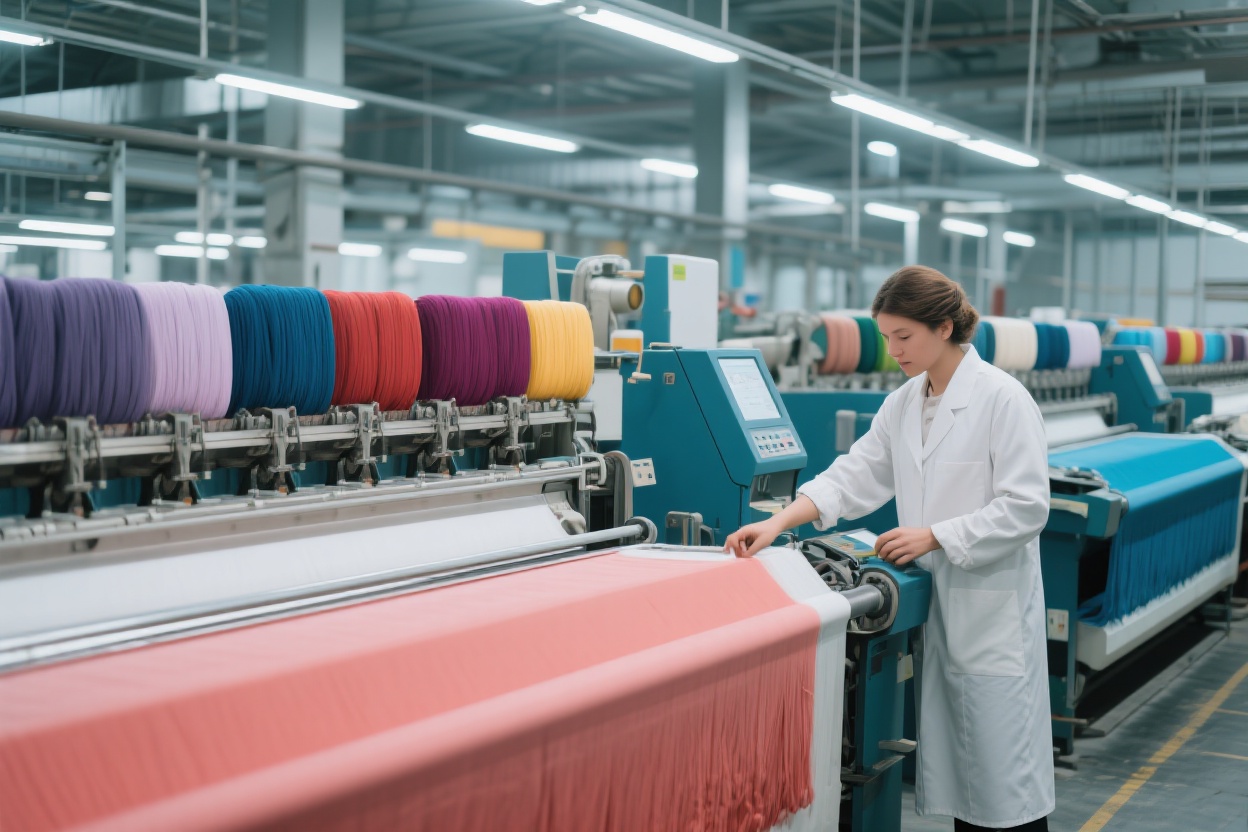
In Zhangjiagang in July, the summer heat is intensifying, but there is a steady bustle in the production workshop of Antai Textile – the dyeing and finishing workshop no longer has the pungent dye smell of traditional dyeing processes; instead, robotic arms are precisely handling rolls of brightly colored acrylic strips. After subsequent processing, these strips will become the core raw material for outdoor jackets and high-end home textiles. Li Xiong, the Marketing Manager, stood in the workshop's visitor corridor, holding a freshly released '2025 Global Dope Dyed Acrylic Fiber Market Report' in his hand, and couldn't help but curl his lips upward: 'Director Huang, look at the procurement demand for outdoor fabrics in Europe, which has increased by 23% year-on-year. Our 'Caiyang Tiao' series is going to be even more sought-after now.'
Director Huang of the Production Department put down the process record sheet in his hand and pointed to the operating No. 3 production line not far away: 'Not just Europe. Last week, a Mexican customer just added an order for 500 tons, specifically asking for our 'Turquoise Blue' color – it's made using dope dyeing technology, with color fastness of level 4-5, not fading even after three months of exposure to the sun; it's perfect for outdoor use.'
Behind this dialogue lies the inevitability of Antai Textile's three decades of deep cultivation in the textile industry. When it was founded in Zhangjiagang in 1993, the company started with a single acrylic yarn production; now it has become an invisible champion in China's colored acrylic fiber sector, with its main business covering acrylic yarn, acrylic strips, colored acrylic strips, and fancy yarns, among which colored acrylic strips account for half of the company's revenue. This leap is precisely due to the敏锐 capture of industry trends – when 'dope dyeing technology' became a key term for the green transformation of the textile industry in 2025, Antai Textile had already stood at the forefront.
'As early as 2022, we noticed the bottlenecks of traditional dyeing processes,' Li Xiong recalled. At that time, when the team was researching the European market, they found that environmental regulations were increasingly stringent on carbon emissions and water consumption of textiles. 'Customers clearly said, 'If your acrylic strips still rely on post-dyeing, we may have to reconsider suppliers.'' This sentence became the 'starting gun' for Antai Textile's technological transformation. The company immediately established a special R&D team and joined forces with the College of Textiles of Jiangnan University to tackle dope dyeing technology – this process uniformly mixes color masterbatches into the spinning solution before acrylic spinning, achieving coloring from the source and eliminating the high-temperature boiling and multiple rinsing steps of traditional dyeing.
The process of technological breakthrough was not smooth sailing. Director Huang still remembers the 'color difference problem' in the early stage of R&D: 'The acrylic strips made at the beginning had color differences between different rolls of the same batch, and the color fastness was also unstable. We stayed in the laboratory with the university team for more than three months, adjusting the color masterbatch ratio, optimizing the spinning temperature curve, and printing more than 200 color plates alone.' In the end, the team not only achieved stable production of 48 color spectrums but also increased the color fastness to level 4-5 (far exceeding the industry average of level 3), with a water-saving rate of 76% – equivalent to each production line with an annual output of 1,000 tons saving the water volume of 3 West Lakes every year.
At the end of 2024, when the industry was still discussing the 'pilot test difficulties of dope dyeing technology', Antai Textile's first pilot production line had been operating stably for half a year, becoming one of the first 12 leading domestic enterprises to complete the large-scale layout of dope dyed acrylic fibers. 'Now, our 'Caiyang Tiao' series takes only 72 hours from order placement to finished product delivery, shortening the construction period by 5 days compared to traditional dyeing,' Director Huang pointed to the beating data on the workshop's electronic screen. 'More importantly, the carbon emissions per ton of products are reduced by 35%, fully complying with the EU's 'Carbon Border Adjustment Mechanism' requirements, which gives us full confidence in bidding in South America and the Middle East.'
Today, looking at Antai Textile's customer list, there are long-term cooperations with domestic outdoor brand 'KAILAS', designated purchases by European home textile giant H&M Home, and even Mexican denim clothing manufacturers have made special trips to Zhangjiagang for inspections – what they value is the dual advantages of dope dyed acrylic fibers: 'long-lasting color and environmental compliance'. 'Last week, a Middle Eastern customer saw our 'Desert Yellow' color sample and immediately decided to order 300 tons, saying, 'This color won't turn gray even after a year of exposure in the desert; it's perfect for our outdoor work clothes,'' Li Xiong said with a smile. This kind of market feedback excites the team more than any award.
From a small yarn factory in 1993 to an important participant in the global dope dyed acrylic fiber market today, Antai Textile's 30 years are exactly a microcosm of China's textile industry's shift from 'scale expansion' to 'quality breakthrough'. When green development has become an industry consensus, this enterprise rooted in Zhangjiagang responds to the proposition of the times with technological innovation – in Antai Textile's plan, the next dope dyeing production line has entered the equipment debugging stage, and 20 new special functional color spectrums will be added in the future to provide more precise material solutions for such细分 fields as outdoor fabrics and medical textiles.
'Textiles are not a sunset industry,' Li Xiong looked at the factory flag fluttering outside the workshop, his tone firm. 'When every yarn carries a 'green gene', it can weave a more vibrant future.' And this is perhaps the best answer Antai Textile has given to the industry.